SSADT(대표 이호덕)가 초미세 패터닝 기술을 기반으로 발광다이오드(LED) 전공정 서비스업을 시작한다. 나노 단위 패턴을 웨이퍼에 도장처럼 찍어내는 `임프린트 공정`을 도입한다. 공정 단가는 낮추고 수율은 97% 전후로 끌어올린다. 소비자거래(B2C) 시장에는 크롬 없는 손톱 광택 용품(글리터)을 내놓는다.
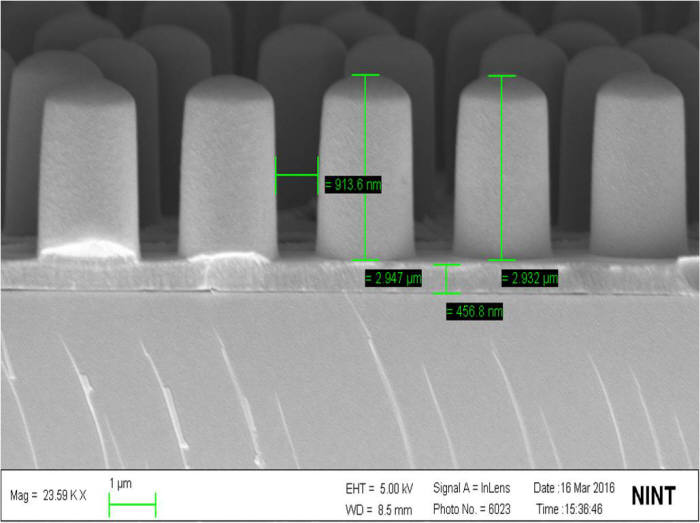
SSADT가 시작하는 LED 전공정 서비스는 웨이퍼 PSS(Patterning Surface Substrate) 공정이다. 웨이퍼 위에 화합물반도체를 성장시키기 전 패턴을 새기는 공정이다. 미세 패턴이 돌기처럼 올라와 재료 간 갈라짐 현상(크랙)을 방지한다. LED 광원 제조 수율을 90% 이상으로 끌어올리려면 이 과정이 필수다.
SSADT는 이 공정에 임프린트 방식을 도입한다. 기존에는 포토마스크에 빛을 쏘는 `노광 방식`이 주류였다. 노광장비 가격이 비싼 것은 물론이고 노광기 상태에 따라 수율 편차가 발생했다. 임프린트 방식은 몰드 하나를 생산한 뒤 도장 찍듯 패턴을 생산한다.
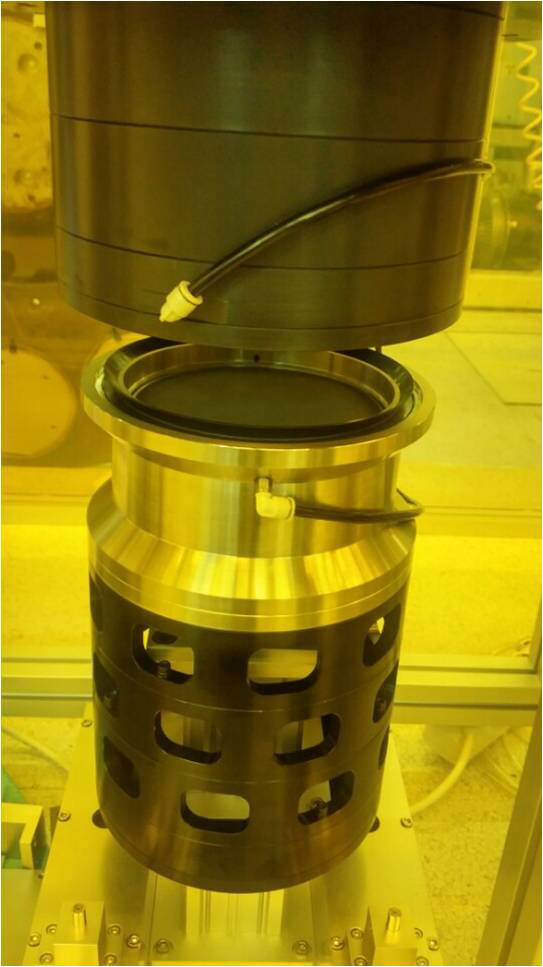
다양한 패턴 대응은 어렵지만 동일 패턴을 연속적으로 찍어내는 데 유리하다. 공정 간소화로 생산원가가 노광 공정 대비 70%에 불과하다. 패턴 불량률은 50% 이상 감소한다. LED 광원 전체로 보면 97~98% 수율 확보가 가능하다. 4인치, 6인치처럼 웨이퍼 크기가 커질수록 원가 절감 효과가 크다.
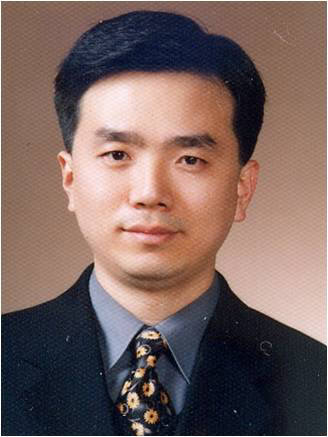
SSADT는 2013년부터 이 공정 기술과 장비를 연구개발(R&D)했다. 공정 효율은 싱가포르 재료연구소(IMRE)와 공동 개발로 검증했다. 양산용 장비는 개발 막바지 단계다. LED 제조업체가 4인치, 6인치 웨이퍼 대응을 요구하면 더욱 시장이 커질 것으로 기대했다.
이호덕 SSADT 대표는 “공정 난도가 높아지면서 작년부터 LED PSS 임가공 업계 어려움이 가중됐다”며 “업체 수 자체가 적어지는 상황이지만 임프린트 공정을 상용화하면 가격, 품질 경쟁력은 오히려 커질 수 있어 기회로 판단했다”고 설명했다.
초미세 패턴 기술을 B2C 제품에도 적용했다. 손톱 광택 용품 `나노 글리터` 양산 채비를 갖췄다. 손톱 위를 문지르면 연마제를 바른 것처럼 광택이 나는 미용 제품이다. SSADT는 올해 이 제품을 약 40만개 생산할 계획이다.
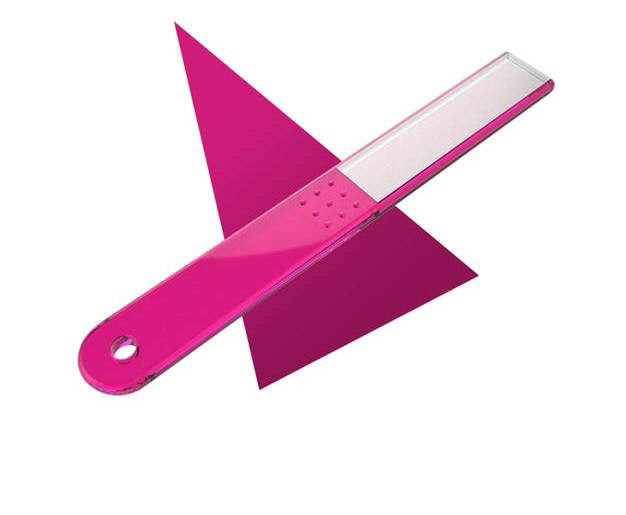
패턴 공정을 개선하고 플라스틱 소재를 접목해 생산 단가를 절반에서 4분의 1수준까지 낮췄다. 중금속인 크롬이 전혀 남지 않는 친환경 제품으로 개발했다. 플라스틱으로 된 손잡이 부분에는 항균 소재를 도입했다.
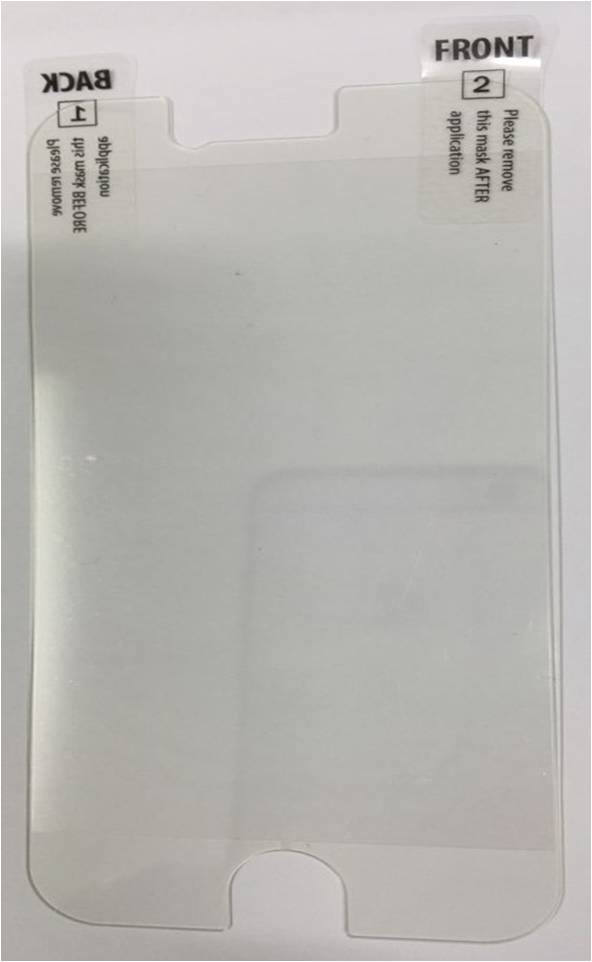
회사 두 번째 B2C 제품이다. SSADT는 2013년부터 싱가포르 나노뷰에 무안경 3D필름을 독점 공급해 지금까지 20만장 이상 팔았다. 스마트폰이나 태블릿PC 글라스에 필름을 씌우면 안경을 쓰지 않아도 3D콘텐츠를 즐길 수 있다.
올해 홍콩 업체와 50만장 규모 추가 공급을 논의 중이다. 이 회사 필름은 표면 거칠기가 10나노미터(㎚)수준이어서 3D화면 구동 전 2D화면 왜곡이 없다. 100~500㎚ 정밀도를 갖춘 경쟁사 제품과 기술 격차가 크다.
송준영기자 songjy@etnews.com