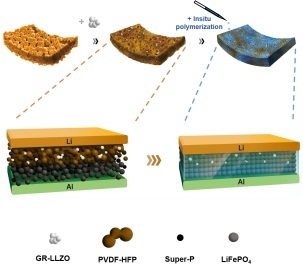
전고체전지는 액체전해질 대신 고체전해질을 사용해 온도변화로 인한 전해액 증발이나 외부 충격에 따른 누액 위험이 없어 안전성 높은 차세대 전지로 주목 받고 있다.
전고체전지에 사용되는 고체전해질은 크게 산화물계, 황화물계, 고분자계, 그리고 2가지 이상의 전해질을 동시에 사용하는 복합 전해질로 구분된다.
이 중 산화물과 고분자를 결합한 복합 고체전해질의 경우 고분자계 고체전해질의 기계적·화학적 안정성과 이온전도도 향상의 장점을 가진 반면 전극 내 입자 간, 또는 전극-전극 간 계면 저항 문제가 단점이 돼 왔다.
계면 저항으로 인해 전지의 출력 특성이 떨어지고, 복합 고체전해질의 두께가 얇아질수록 리튬 수상 돌기(Li dendrite)로 인한 단락이 발생해 전지 수명이 줄어들기 때문이다.
한국생산기술연구원(원장 이상목)이 현장 열중합 방식을 적용해 높은 기계적 강도를 가지면서 계면저항 문제를 획기적으로 개선한 복합 고체전해질을 개발했다.
생기원 에너지나노그룹 임진섭 수석연구원 연구팀은 현장 열중합 방 식을 이용해 액상의 모노머 용액을 고분자로 중합시켜 계면 저항을 원천 차단하는 새로운 형태의 복합 고체전해질을 개발했다고 밝혔다.
연구팀은 이를 위해 먼저 산화물계 고체전해질과 고분자계 고체전해질을 결합한 복합 고체전해질을 제조했다.
산화물계 고체전해질은 갈륨, 루비듐을 도핑한 리튬-란타늄-지르코늄 -산소(GR-LLZO)로, 상온에서 높은 이온전도도(1.35x10-3 S ㎝-1)를 나타낸다.
또한 전위 안정성이 넓어 고에너지 밀도를 갖는 전지설계에 유리하고, 황화물계 고체전해질보다 대기 중 안정성도 높다.
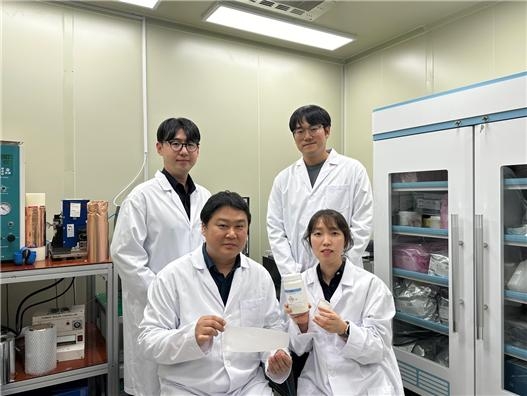
연구팀은 TDL과의 공동 연구를 통해 쿠에트-테일러 공침반응으로 GR-LLZO를 합성하고, 여기에 고분자계 바인더인 폴리플루오르화비닐리덴-헥 사플루오르프로필렌(PVDF-HFP)을 결합했다.
이후 현장 열중합 방식을 도입, 20마이크로미터(㎛) 두께의 복합 고체전해질 박막 제조에 성공했다.
현장 열중합 방식을 적용하면 액상의 모노머 용액이 양극에 함침 된 후 열을 가해 고분자로 중합되는 과정에서 복합 고체전해질과 전극 간 높은 계면 저항을 감소시켜 전지의 출력 특성이 크게 향상된다.
연구팀이 현장 열중합 방식을 적용해 개발한 복합 고체전해질은 두께는 상용화된 리튬 이온전지의 분리막과 비슷한 수준이면서, 리튬 수상 돌기에 대한 내구성이 높아 70℃의 고온에서 150 사이클 후에도 93.2%의 용량 유지율과 높은 출력 특성을 보였다.
전위 안전성도 기존 4.0볼트(V)에서 5.1V로, 기계적 강도는 7.01 메가파스칼(MPa)에서 9.12 MPa로 향상돼 실험 결과 구부리거나 자르고 불 이 붙는 상황에서도 전지가 안정적으로 작동되는 것으로 나타났다.
또 전극 제조와 전지 조립 공정이 기존 리튬 이온 전지 개발 공정과 유사해 양산라인을 새로 설치할 필요가 없어 공정비용도 줄일 수 있다.
임진섭 수석연구원은 ”전해질의 두께를 최소화하면서도 리튬 수상돌기 문제를 해결한 복합 고체전해질을 개발하는 것이 가장 어려운 목표였다”고 말하며 ”핵심 기술을 확보한 만큼 전고체전지 실용화를 앞당기기 위한 후속 연구에 주력할 계획”이라고 밝혔다.
이번 연구 성과는 3월 13일 재료화학 분야 세계적 학술지'머티리얼스 케미스트리 A' 온라인 판에 게재됐다.
김영준 기자 kyj85@etnews.com