국내 연구진이 인공뼈 이식 부작용을 크게 줄일 수 있는 기술을 개발했다. 임상시험을 거쳐 이르면 3년 뒤부터는 활용할 수 있게 될 것으로 전망된다.
타이타늄 합금으로 제작되는 인공뼈는 이식할 때 염증이 생겨서 신체와 결합이 안 되는 부작용이 발생할 수 있다. 이런 부작용이 발생하면 임플란트를 제거해도 재이식이 불가능하다는 단점이 있었다.
한국생산기술연구원(원장 이성일)은 김현종 표면처리그룹 박사팀이 골절을 치료할 때 활용하는 타이타늄 재질의 인공뼈(임플란트) 안에 기공을 생성시켜서 약물을 넣는 방식으로 이식 수술 부작용을 예방할 수 있는 '약물방출형 다공성 임플란트' 제조 기술을 개발했다고 11일 밝혔다.
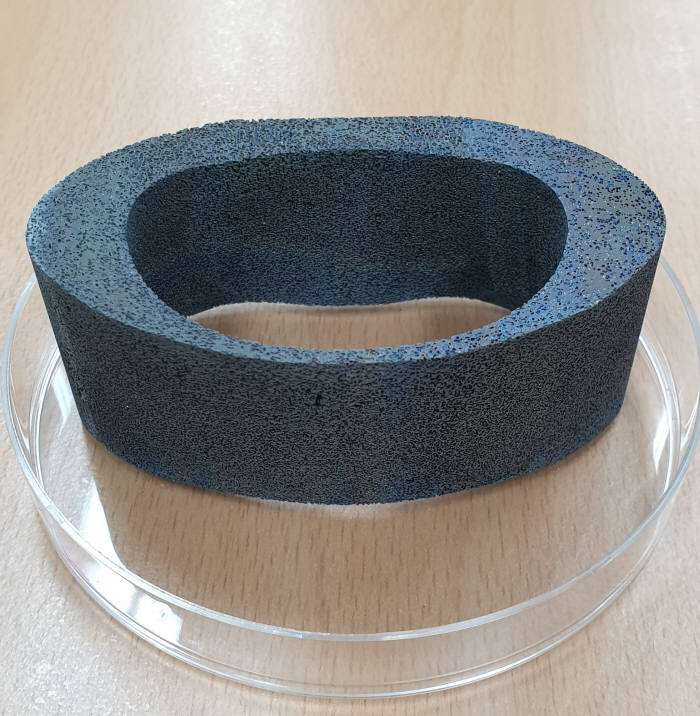
이 기술 가운데 기술 완성도가 높은 주조 공정 기술은 우선 기업에 이전하고, 표면처리 기술은 내년부터 3년 동안 임상시험을 거친 후 기업에 이전해서 상용화할 계획이다.
연구팀이 개발한 임플란트는 약물을 담을 수 있도록 다공 구조로 만들고, 그 위를 특수 코팅해서 기공에 담은 약물이 서서히 방출되도록 설계했다. 물이 얼 때 기포가 생기는 원리를 이용한 '동결 주조' 방식으로 다공 구조를 만들었다. 약물을 담은 후에는 그래핀 소재인 에어로겔과 밀착성이 좋은 하이드로 겔로 복합 코팅, 약물이 한 번에 방출되는 것을 막았다.
기공에는 항염증제, 골 형성 촉진 단백질, 줄기세포 등을 담았다. 수술 초기의 이식 부위 염증 발생을 억제하고, 임플란트가 주변 조직과 결합하도록 돕는 약물이다. 이들 약물은 열흘 동안 서서히 방출된다.
타이타늄 합금으로 제작해 강한 탄성을 유지하면서도 실제 뼈와 유사한 기능을 하도록 한 것도 장점이다. 기존의 타이타늄 합금은 탄성이 강해서 외부 자극을 흡수하지만 연구팀이 개발한 임플란트는 탄성이 뼈와 유사하다.

세계에서 처음으로 전자기유도장치와 수소플라스마 기반의 연속 주조 방식을 적용해 공정 효율을 극대화하고, 금형 몰드를 적용한 대량 생산 기반을 확보하는 등 제조 원가도 기존의 50% 정도로 대폭 절감했다.
김현종 박사는 “그동안 전량 수입해 온 임플란트를 국산화하고, 제조 공정 효율을 높였다”면서 “임플란트뿐만 아니라 스텐트, 인공장기, 바이오센서 등 광범위하게 활용할 수 있는 기술”이라고 설명했다.
대전=김영준기자 kyj85@etnews.com