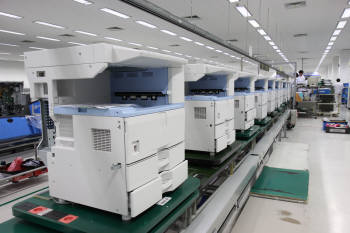
지난 19일 신도리코 충남 아산공장. 수십명의 직원들이 조립동에서 일본으로 수출될 복합기를 조립하고 있다. 아직 국내 출시도 안된 최신 제품이 완성되는 모습을 살펴보다 뭔가 이상한 점을 발견했다. 조립 라인이 너무나 단순해 보인 것이다. 첨단 제품이 이런 투박한 라인 위에서 생산된다는 사실이 믿기 어려웠다. 김문환 공장장은 “이것이 신도리코만의 독자적인 ‘무빙스퀘어’ 생산방식”이라고 소개했다.
◇무빙스퀘어, 한국형 생산시스템 전형=1983년 문을 연 아산공장은 신도리코의 핵심 생산기지다. 연간 생산능력이 디지털 복합기 70만대, 현상제 1500톤, 감광지 1만5000톤, 드럼 300만본, 부품 850만개에 달한다. 사실상 프린터와 복합기에 들어가는 모든 부품을 자체 생산하고 있다. 국내 시장 점유율 35%로 독보적인 위치를 차지하고 있는 A3 사무용 복합기도 이 공장에서 생산된다. 그런 아산공장에 3년 전 국내외 어디서도 찾아볼 수 없는 ‘무빙스퀘어’가 도입됐다.
무빙스퀘어(Moving Square)는 이름 그대로 ‘움직이는 정사각형’이다. 가로 세로 1m, 높이 1.5m 크기 작업대에 바퀴 4개가 달렸다. 아래 칸에는 부품과 모듈을 싣고 위 칸에는 제품을 올려놓는다. 위 칸은 제자리에서 360도 회전이 가능해 어느 방향에서나 작업이 가능하다. 이런 작업대가 커다랗게 ‘U’자를 그리며 공장 내부를 회전한다.
고가 장비가 사용되지 않고 아산공장에서 직접 만들기 때문에 무빙스퀘어 설치비용은 6000만원에 불과하다. 기존 컨베이어 벨트가 5억원인 것과 비교하면 10분의 1 수준이다. 잔고장이 적고 고장이 나더라도 전체 라인을 멈추지 않고 해당 작업대 하나만 빼내면 되기 때문에 유지비용도 10% 밖에 들지 않는다. 한쪽에서만 작업이 가능하던 컨베이어 벨트와 달리 양쪽에서 작업이 가능해 생산성도 20%나 높아졌다. 분당 1대의 완제품을 생산할 수 있어 월 생산량이 1만5000대에 이른다.
김 공장장은 “자체 개발 당시 제품 대신 비슷한 무게를 가진 직원들이 작업대에 올라가 무빙스퀘어를 테스트하기도 했다”면서 “비용을 절감할 수 있는 진정한 스마트가 무엇인지 보여주는 작품”이라고 말했다.
◇전산화로 스마트 생산시스템 구축 완료=아직 조립을 마치지 않은 복합기 뒷면 한 가운데에 PCB 기판이 보였다. PCB는 복합기 작동을 제어해 ‘엔진’으로 불린다. 조립오류 방지시스템(MMPS)이 적용된 이 기판에는 칩 하나하나에 생산일자 등이 기록된 바코드가 부착돼 있다.
덕분에 불량부품 유입을 원천 차단할 수 있다. 정밀측정 렌즈를 통해 부품이 제대로 조립됐는지 확인할 수 있다. 품질검사를 할 때도 직접 출력할 필요 없이 컴퓨터를 통해 검사하고 시정도 가능하다.
3중 4중 겹겹이 미세먼지 차단 설비가 설치된 통로를 지나자 3층 높이 부품 창고가 나타났다. 영화 매트릭스 한 장면을 보는 듯한 이 창고는 빈틈 없이 치밀한 설계로 효율성을 극대화했다. 8월 구축한 심플(Sindoh Manufacturing & Production onLine Execution system) 시스템을 통해 5000종의 부품이 어디에 얼마나 저장돼 있는지 한눈에 파악할 수 있다. 명령만 내리면 로봇 팔이 해당 부품을 꺼내 준다. 물론 이 부품에도 바코드가 부착돼 있어 언제 어디서 생산돼 어느 경로를 거쳐 공급됐는지까지 알려준다. 부품 고장에 즉각 대응이 가능한 것이다.
이 같은 스마트 생산시스템을 통해 신도리코는 대표적 베스트셀러 디지털 복합기 ‘디지웍스’와 레이저 프린터 블랙풋 등을 생산하고 있다. 매출의 70%를 까다로운 품질검사로 유명한 미국·일본 등 해외시장에서 올리고 있다.
김문환 공장장은 “현재 모노레일을 적용한 새로운 무빙스퀘어 라인을 구축하고 있어 또 한 번 진화하는 셈”이라며 “50여년간 축적된 신도리코만의 생산 노하우가 없었다면 불가능한 일”이라고 말했다.
아산=
김용주기자 kyj@etnews.com