고객과 협의 내년 7월 램프업 계획
삼성전자, 1세대 제품 내년 생산 목표
초미세 공정 양강구도 우위 점할 기회
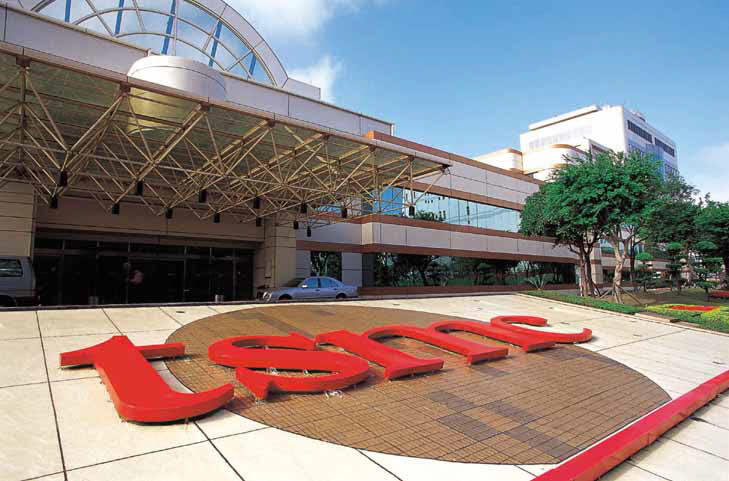
세계 최대 파운드리 업체인 대만 TSMC가 3나노(㎚) 반도체 양산 시험대에 섰다. 기술 난도가 높아 앞선 7나노, 5나노 공정보다 개발이 더 오래 걸리고 있는 것으로 나타났다. 3나노 반도체 상용화를 놓고 TSMC와 경쟁하고 있는 삼성전자에 유리하게 작용할지 주목된다.
31일 업계에 따르면 TSMC는 2분기 실적 콘퍼런스콜에서 3나노 반도체 양산 지연을 알렸다. 2분기 생산을 시작한 과거와 달리 3나노는 내년 7월 '램프업(양산 전 생산능력을 끌어올리는 작업)'할 계획이라고 밝혔다.
TSMC는 2018년 2분기와 2020년 2분기 각각 7나노, 5나노 반도체 생산을 시작했다. 이에 제품 출하 실적도 2분기에 반영됐다.
그러나 3나노 양산이 앞선 공정들에 비해 지연되는 것 같다며 이유를 묻는 한 애널리스트의 질문에 웨이저자(魏哲家) TSMC 최고경영자(CEO)는 “5나노에 비해 3나노가 3~4개월 정도 늦은 것이 맞다(about 3 to 4 months is a delay as compared with 5-nanometer)”면서 “3나노 기술이 매우 복잡하기 때문에 고객과 협의해 내년 하반기(7월) 양산을 결정했다”고 답했다.
TSMC은 지금까지 애플과 초미세 공정 개발을 함께 했다. 7나노, 5나노 최신 공정이 완성될 때마다 애플은 TSMC에 아이폰용 애플리케이션프로세서(AP) 제조를 맡겼고, 이를 최신 아이폰에 탑재했다. 가장 앞선 반도체 제조 기술로 AP를 만들어 성능이 차별화된 아이폰을 출시하려는 의도였다. 반도체는 통상 회로가 미세해질수록 트랜지스터의 집적도가 높아져 성능이 향상된다.
TSMC와 애플의 협력은 고성능 반도체를 필요로 하는 완제품 회사와 최신 반도체 공정으로 대형 고객사를 확보하려는 파운드리 회사 간 이해관계가 일치하며 시너지를 냈다. TSMC는 2년 간격으로 2분기 신형 칩 양산과 미세화에 성공하고, 애플은 3분기 경쟁사를 압도하는 성능의 신형 아이폰을 출시해왔다.
그러나 3나노에서는 변화가 불가피해졌다. TSMC의 3나노 반도체 양산 일정 변화로 완제품 출시 시점이 조정될 전망이다. TSMC는 구체적인 고객사를 공개하지 않았지만 애플이 3나노 파운드리 고객사일 경우 내년 신형 아이폰은 4분기에 출시될 가능성이 있다. 애플이 아닌 다른 기업이 TSMC의 3나노 고객일 경우에도 새로운 초미세 반도체 주문 회사가 등장하는 셈이어서 반도체를 포함한 IT 업계에 파장이 적지 않을 전망이다.
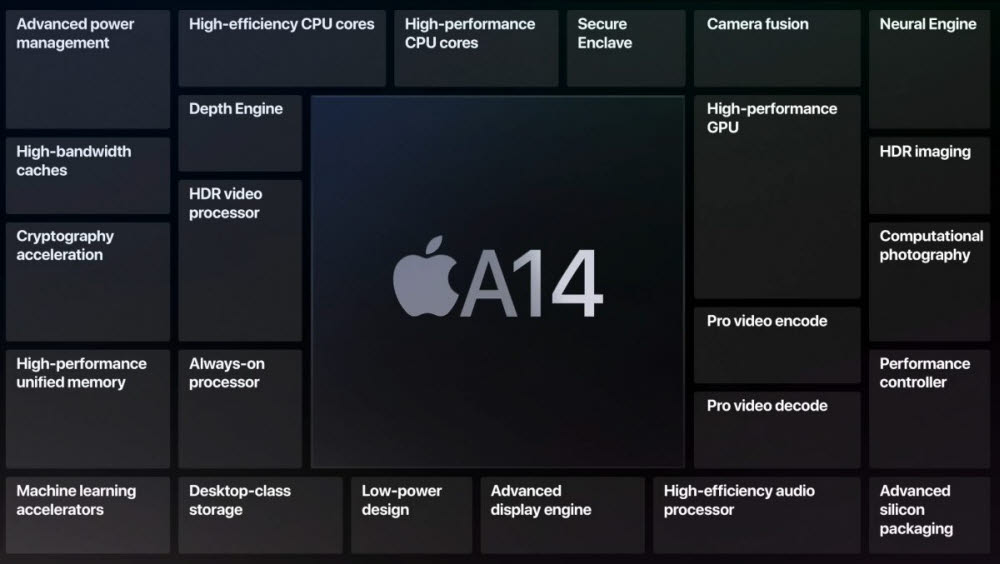
관심은 3나노 양산 경쟁에 쏠린다. 2022년 3나노 반도체 양산에 도전하고 있는 기업은 전 세계 TSMC와 삼성전자뿐이다. 초미세 공정 개발과 생산라인 구축에 천문학적인 금액이 투입되기 때문에 세계 1위 파운드리 업체인 TSMC와 메모리 1위 삼성전자가 도전하고 있다. 인텔도 3나노 경쟁에 뛰어들었지만 2023년이 목표다.
사실상 TSMC와 삼성전자의 양자 대결 구도인 가운데 TSMC의 3나노 양산이 1분기 정도 지연돼 삼성전자에 유리하게 작용할지 주목된다. 삼성전자는 아직 구체적인 3나노 가동 시점을 밝히지 않고 있다. 삼성은 지난 2분기 실적발표 콘퍼런스콜에서 “GAA(게이트올어라운드) 공정이 적용된 3나노 1세대 제품을 내년 양산할 계획이고, 2023년에는 GAA 적용 3나노 2세대 제품을 양산하는 것이 목표”라고 밝혔다.
TSMC가 기술 난도로 3나노 공정 개발에 애를 먹고 있는 것처럼 삼성전자도 어려움을 겪을 가능성도 있다.
TSMC 3나노와 삼성전자 3나노는 차이가 있다. TSMC는 핀펫 공정으로, 삼성전자는 GAA를 도입할 계획이다. 핀펫과 GAA는 트랜지스터 구조가 다르다. GAA 3나노는 세계 처음 시도되는 것이다. 양사는 보다 효율적인 전류 제어 목표로 개발을 추진하고 있다.
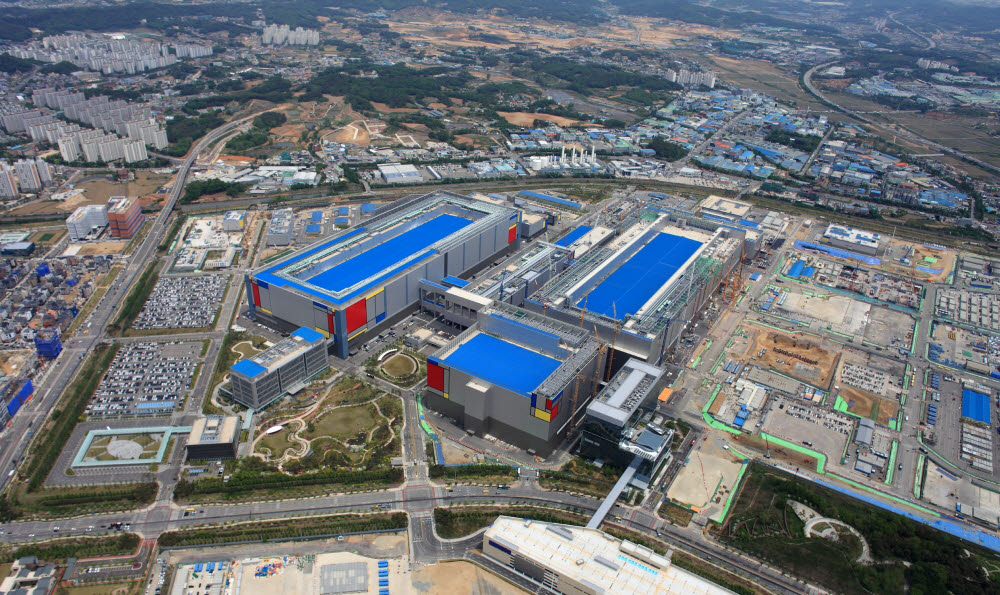
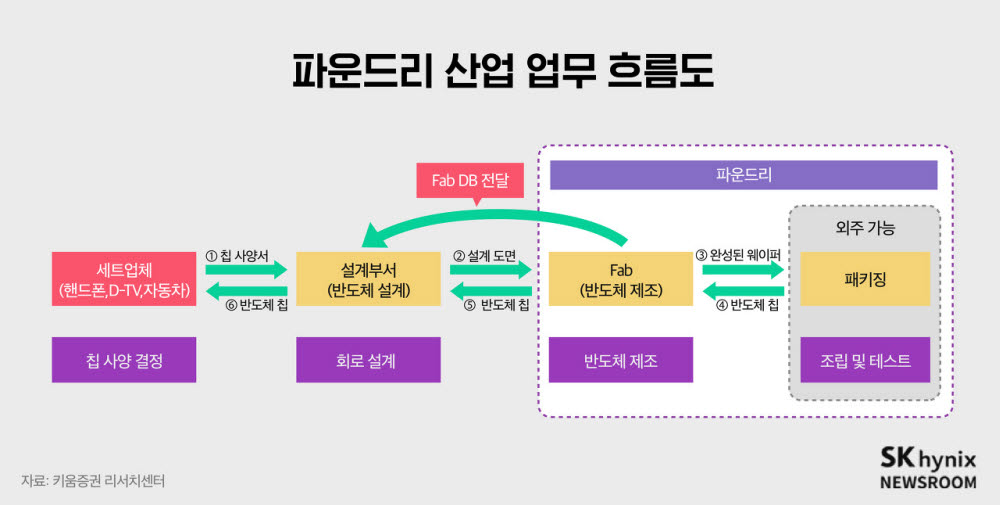
윤건일기자 benyun@etnews.com