일명 ‘김기남 프로젝트’로 온양에 라인 구축…애플 AP 물량 재수주 포석
삼성전자가 새해 반도체 패키지 신공정을 독자 개발한다.
대만 TSMC에 뺏긴 애플 애플리케이션프로세서(AP) 위탁생산(파운드리) 물량을 다시 수주하기 위한 방안이다. TSMC는 첨단 전 공정 웨이퍼 가공 능력에다 새로운 패키지 기술을 제안, 지난해 삼성전자로부터 애플 AP 생산 물량을 전부 빼앗아갔다.
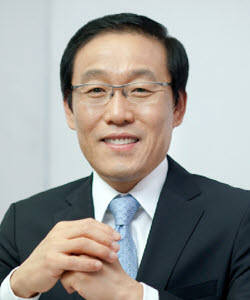
27일 업계에 따르면 삼성전자 반도체사업부는 팬아웃-웨이퍼레벨패키지(Fo-WLP) 신 공정 개발을 위해 투자하고 있는 것으로 확인됐다. 또 지난해 말 인텔에서 영입한 패키지 분야 전문가 오경석 상무(반도체연구소 담당임원)를 중심으로 관련 기술을 독자 개발하고 있다. 삼성 안팎에선 이를 '김기남 프로젝트'라 부른다. 김 사장이 올해 상반기에 이 프로젝트를 극비리 지시했기 때문에 붙은 이름이다.
패키지는 가공이 끝난 실리콘 웨이퍼에서 자른 칩(Die)을 포장하는 작업이다. 외부 습기나 불순물·충격으로부터 칩을 보호하고 메인 인쇄회로기판(PCB)과 신호를 전달할 수 있게 하는 공정이다. 집적도가 높아지면 칩 면적은 좁아지고 입출력(IO) 단자 숫자는 늘어난다. 기존 팬인 패키지로는 늘어난 IO 숫자를 감당하기 어려웠다. 이 때문에 패키지 공정 시 칩 바깥쪽으로 배선을 빼는 팬아웃 기술이 각광받게 됐다. 팬아웃 기술을 활용하면 패키지 내부에 들어가는 값비싼 패키지 PCB가 필요하지 않게 된다. 원가를 절감할 수 있고, 패키지 두께(높이)도 줄일 수 있다.
삼성 지금까지 가공을 마친 웨이퍼를 하나씩 잘라 패키징하는 다이레벨패키지(DLP) 방식을 활용했다. WLP는 기술 난도가 높지만 웨이퍼 상태 그대로 패키징을 수행, 공정 횟수를 단축할 수 있다. 원가 절감에도 유리하다. 전문 외주반도체테스트패키지(OSAT) 업체 대부분이 WLP 라인을 보유하고 있어 기술 방식도 검증됐다.
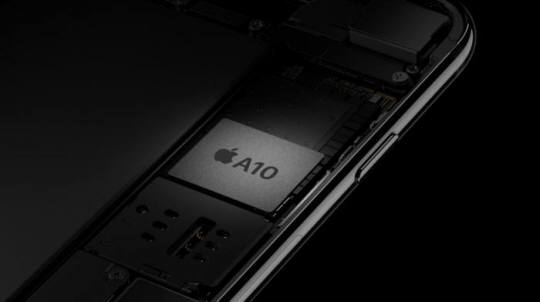
대만 TSMC는 세계에서 가장 먼저 AP용 Fo-WLP 기술을 상용화해 아이폰7에 탑재되는 16나노 A10, 아이폰8용 10나노 A11 파운드리 생산을 수주했다. TSMC는 Fo-WLP 기술을 자체 기술명 'InFO'(통합형 팬아웃)라고 부른다.
전문가는 전 공정 웨이퍼 가공 분야 경쟁력은 삼성과 TSMC가 호각을 다투고 있지만 결국 애플이 TSMC에 물량을 몰아 준 이유는 패키지 경쟁력을 높이 샀기 때문으로 분석한다. 반도체 분석 전문업체 테크인사이트는 애플 아이폰에 탑재된 신형 A 시리즈 AP 단면을 분석하면서 “InFO 기술이 적용된 덕에 AP 두께가 과거보다 현저하게 얇아졌다”면서 “TSMC가 이 기술로 애플 물량을 독점한 것으로 추정된다”고 말했다.
업계 관계자는 “그동안 삼성전자는 전 공정에 매진하고 후 공정 분야에는 큰 투자를 하지 않았다”면서 “애플 사례에서 후 공정 패키지 분야에도 대규모 투자와 기술 개발 필요성을 절감하게 된 것으로 안다”고 설명했다.
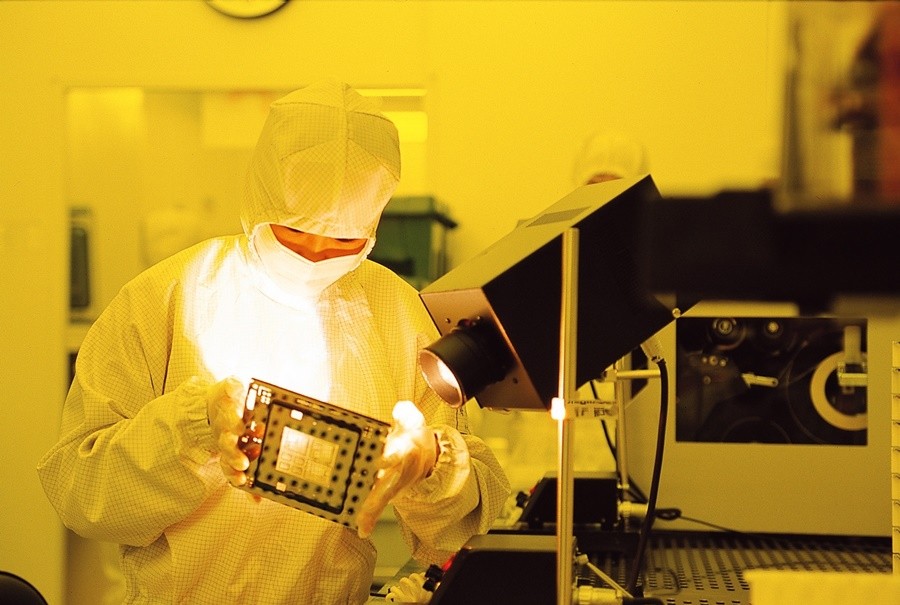
삼성전자가 독자 Fo-WLP 기술을 확보하면 삼성전기 패널레벨패키지(PLP) 사업은 위기를 맞을 것으로 보인다. PLP는 동그란 웨이퍼가 아닌 사각형 패널 위에다 칩을 놓고 패키징하는 기술 방식이다. 이전 반도체 부문장인 권오현 회장이 이 기술을 적극 밀었고 그룹 차원의 사업 조정을 거쳐 삼성전기에 이 프로젝트를 넘겼다. 그러나 처음 시도하는 기술이어서 장비, 재료 생태계가 부실해 시행착오도 많이 겪은 것으로 알려졌다.
삼성전자 반도체사업부가 이 방식에 회의감을 가지면서 삼성전기에 파견한 패키지 전문 인력 대다수를 복귀시킨 것으로 전해졌다. 삼성전자가 Fo-WLP 기술을 독자 개발하고 양산 체제를 갖추면 굳이 외부로 패키지 물량을 맡길 이유도 없어질 것으로 보인다.
한주엽 반도체 전문기자 powerusr@etnews.com