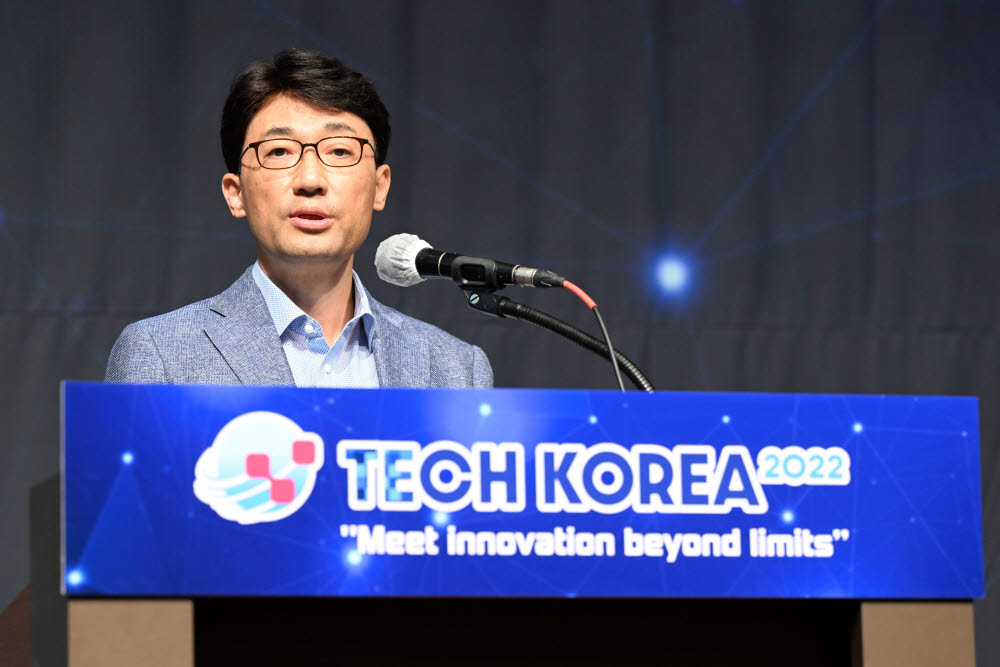
LG이노텍이 부품 개발의 '디지털 트윈' 시대를 열었다. 설계·검증·공정뿐 아니라 생산까지 가상에서 사전 진행, 신속한 제품 개발과 신뢰성을 확보한다. 다수 가상화 성과를 확보하면서 생산 비용을 낮추고 개발 기간을 단축하는 등 고객 요구에 대응할 수 있게 됐다.
강민석 LG이노텍 최고기술책임자(CTO) 부사장은 21일 테크코리아 2022에서 '스마트 산업 변화와 부품 산업의 도전과 기회'를 주제로 부품 업계가 직면한 각종 요구사항과 해결 사례를 공유했다. 강 부사장은 “디지털 기술이 확산되면서 초정밀, 초소형, 고신뢰성 부품이 요구되고 실시간으로 고객 요구사항을 반영해야 하는 상황”이라며 “부품사 역시 빅데이터와 인공지능(AI) 등 디지털 기술을 활용해 시장에 대응해야 한다”고 강조했다.
강 부사장은 급성장하는 자율주행차와 메타버스 시장을 사례로 들었다. 자율주행차는 안전에 대한 담보가 필수적이다. 이 때문에 카메라, 라이다, 레이더 등 부품은 초정밀뿐 아니라 고신뢰성·안정성을 요구받는다. 메타버스는 가상현실(VR)·증강현실(AR) 기술 완성도를 높이면서 초소형·초경량 부품이 필요하다. 강 부사장은 “부품사는 고객이 요구하는 품질 혁신을 시도하고 다양한 요구에 맞춘 유연한 설계·생산을 해야 한다”며 “이를 통해 개발과 생산 기간을 줄여야 할 것”이라고 밝혔다.
LG이노텍은 부품사가 직면한 도전 과제를 '디지털 트윈'으로 해소한다. '디지털 개발&생산(Digital Development Manufacturing)' 전략으로 부품 설계와 공정 등 여러 단계를 가상화했다. 빅데이터와 AI를 적용한 가상화 개발로 다양한 문제를 사전 검증하고 이를 실제 제품 생산에 적용한다. 강 부사장은 “실제 부품 개발 시 여러 단계 검증을 거치게 되는데 이를 가상화하면 실패 비용을 최소화하고 고객에게 빠른 피드백을 줄 수 있어 최적 공정 조건을 맞출 수 있다”고 말했다.
LG이노텍은 이미 다수 부품 개발에 가상화를 적용해 생산성을 높였다. AR 글라스 핵심 부품인 컴바이너 광효율 저하를 사전 차단하기 위해 가상 설계를 적용, 취약점을 발생시키는 설계 인자를 선별하고 수치를 정량화했다.
이를 실제 설계에 적용해 생산 불량을 최소화했다. 250m 이상 실거리 측정이 필요한 라이다 부품 개발도 가상현실에서 실거리(250미터)를 근거리로 모사, 공간과 물량 한계를 극복했다. 실제 공정 불량 검출 후 반복 실험으로 대응하면서 긴 시간이 소요됐던 기존 검사를 가상화해 수율 안정화와 납기(리드타임) 단축에도 성공했다.
강 부사장은 “디지털 개발·생산을 통해 고객사가 요구하는 각종 사양을 빠르게 만족시키면서 개발 기간도 줄여 비용 절감하고 있다”며 “유의미한 생산성 향상을 확보한 상황”이라고 밝혔다.
[글로벌 디지털 트윈 시장 규모 전망]
자료=마켓츠앤드마켓츠
![[테크코리아 2022]LG이노텍 "부품 개발에 '디지털 트윈' 적용"](https://img.etnews.com/photonews/2209/1575096_20220921161608_588_T0001_550.png)
권동준기자 djkwon@etnews.com