1. 반도체 기업 A사 클린룸 담당 임직원이 긴급회의를 열었다. 어디선가 파티클(이물, 먼지)이 유입돼 특정 시간대에 생산한 웨이퍼 수백장에 문제가 생겼기 때문이다. 클린룸은 최고 수준인 ‘클래스 1’을 유지했기에 원인을 당장 찾아내기 힘들었다. 나중에 원인을 파악해보니 반도체 제조장비 내부에 발생한 유기물이 제대로 처리되지 않고 벽에 붙어 있다 웨이퍼에 떨어져 생긴 문제였다.
2. 카메라 모듈기업 B사는 최근 고해상도 제품 비중이 커지면서 고민에 빠졌다. 화면을 확대했을 때 마치 멍이 든 것처럼 일부분이 얼룩져 보이는 현상이 발생했기 때문이다. 문제를 파악해보니 렌즈를 층층이 겹치는 과정에서 파티클이 유입된 것이었다.
반도체·디스플레이·모듈·부품 기업이 제조 클린룸에서 발생하는 파티클과 전쟁을 벌이고 있다. 반도체 공정은 미세해지고 고부가가치 디스플레이 비중이 커지면서 파티클로 인한 불량 가능성이 커졌기 때문이다.
최근 반도체·디스플레이 단가 하락으로 이익률이 낮아지면서 기업이 원가절감 차원에서 수율 확보에 비상이다. 기업 관심이 클린룸 내 파티클 관리로 이어지고 있다.
김진호 제덱스 대표는 “반도체·디스플레이 기업뿐만 아니라 최근에는 카메라 모듈을 비롯한 부품 기업도 파티클 관리 필요성에 대해 관심을 갖는 분위기”라고 전했다.
웨이퍼와 패널을 세정하고 클린룸을 설계·제작하는 기업과 달리 제덱스는 틈새 시장을 파고들었다. 반도체·디스플레이 장비 부품용 파티클 검사·세정장비, 표면 입자 검출·계수장비, 파티클 채취용 필름과 관련 재료를 공급한다. 장비뿐만 아니라 방진복과 청정용품에 대한 파티클도 검사·평가한다.
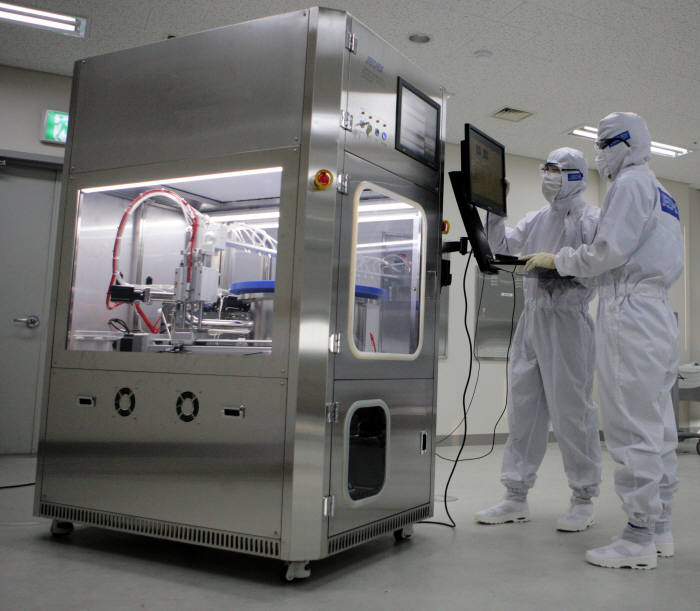
김진호 대표는 “제품 불량 원인을 파악해보면 파티클이 원인인 경우가 대부분”이라고 강조했다. 장비나 공정 이상으로 불량이 발생하는 경우도 있지만 예상치 못하게 날아든 파티클 때문에 불량이 발생하는 경우가 훨씬 많다는 설명이다.
김 대표는 지난 1983년부터 삼성전자 반도체 생산라인에서 파티클 관리 업무에 종사하며 30여년간 이 분야 경력을 쌓았다. 2009년부터 관련 장비를 개발했고 최근 국내 특허를 출원했다. 국내 반도체, 디스플레이, 부품 기업에 파티클 관리 컨설팅 서비스와 장비를 제공했다.
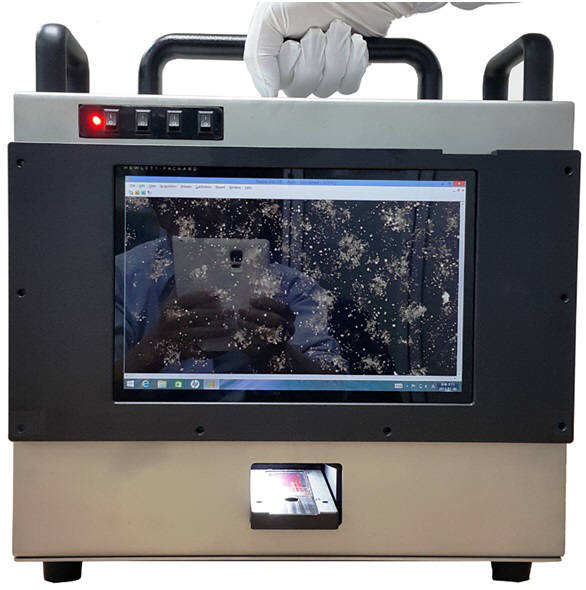
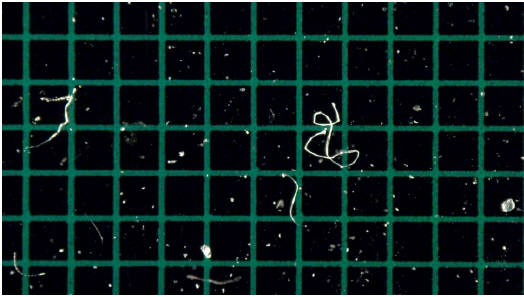
그는 ‘TCM(Total Cleanliness Management)’ 개념을 전사 차원으로 정립하고 반도체·디스플레이뿐만 아니라 다양한 업계로 확산하는게 목표다. 각 기업을 찾아다니며 교육한 내용을 바탕으로 오는 26일 이물·파티클 관리 세미나도 연다.
김 대표는 “각 업계에 최적화한 파티클 관리 방법이 필요하다”며 “장비 기업은 챔버 내에서 효율적으로 파티클을 제거할 수 있도록 설계하고 포장지 기업은 청정도를 한단계 끌어올려 장비와 클린룸에 유입하는 파티클을 최소화하는 등 TCM 개념을 확산하는 데 노력할 것”이라고 말했다.
제덱스는 국제 특허를 출원한 뒤 해외에도 진출한다는 목표다. 설비 투자가 많은 중국은 대기 오염도가 높아 공장 내외기 관리가 당면 과제다.
김 대표는 “자체 개발한 장비 기술과 서비스 노하우를 살려 국내 기업은 물론이고 해외 기업에도 TCM을 정립하고 싶다”고 포부를 밝혔다.
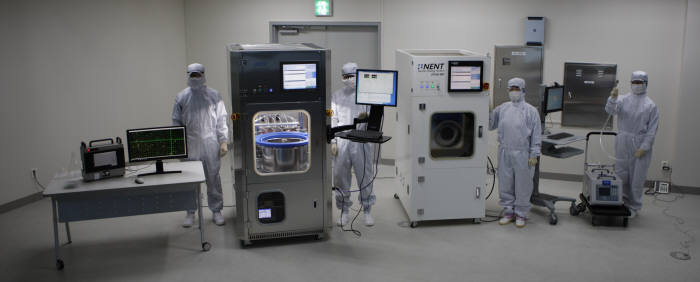
배옥진 디스플레이 전문기자 withok@etnews.com