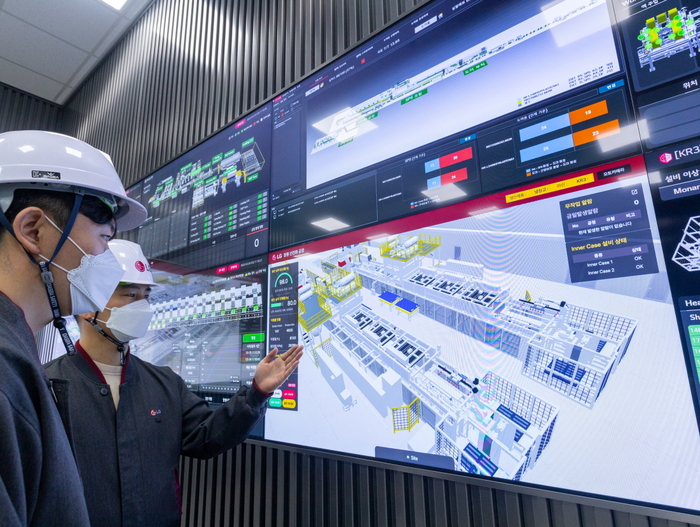
국내 기업들이 제조 현장에 스마트팩토리와 인공지능(AI) 등 첨단 기술을 대거 적용, 생산성 개선에 뛰어들었다. 첨단 기술 도입으로 근본적인 제조 경쟁력을 높여 위기에 대응하려는 시도다. 대내외적으로 시장 불확실성이 커지면서 산업 전망이 어려운 가운데, 제조업 전(全) 분야에서 이같은 첨단 기술 접목이 이뤄지고 있어 생존 전략으로 빛을 발할지 주목된다.
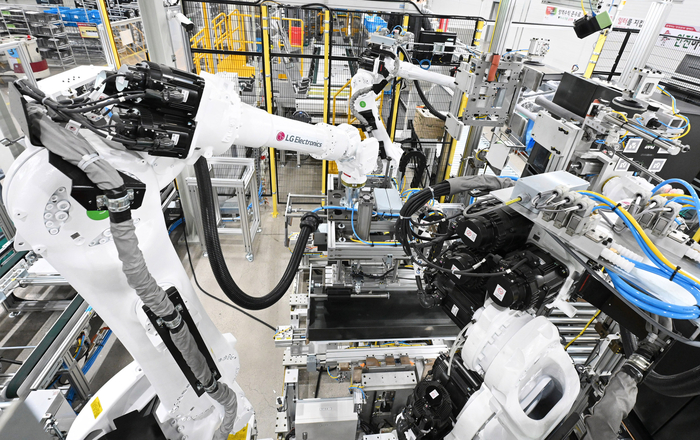
◇LG전자·SK온, 스마트팩토리 전환 '박차'
LG전자는 제조·생산 경쟁력 강화 차원에서 스마트팩토리로 구축하고 있다. 국내 뿐 아니라 글로벌 생산 거점까지 스마트 팩토리 전환 속도를 높이고 있다. 스마트팩토리란 공장 설계·구축·운영 등 모든 단계에서 자동화와 지능화 솔루션을 적용, 생산성과 품질을 획기적으로 끌어올리는 것을 뜻한다.
LG전자의 스마트 팩토리 핵심 기술은 디지털 트윈이다. 현실과 동일한 대상을 디지털 가상 공간에 만들고 AI와 빅데이터를 결합해 생산 현황과 설비 이상 유무를 분석·예측하는 기술이다. 30초 간격으로 공장 안 데이터를 수집해 10분 뒤 상황을 예측, 제조 과정의 각종 문제를 사전에 해결하도록 했다.
경남 창원에 위치한 LG전자 스마트파크와 미국 테네시 공장은 이같은 스마트팩토리 기술력을 인정받아 세계경제포럼(WEF)의 등대 공장에도 선정됐다. 등대 공장은 첨단 기술을 접목해 세계 제조업의 미래를 밝히는 공장을 의미한다.
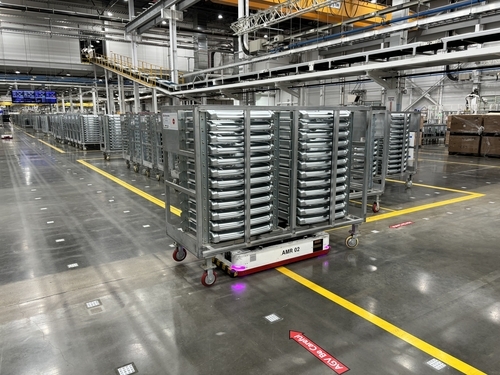
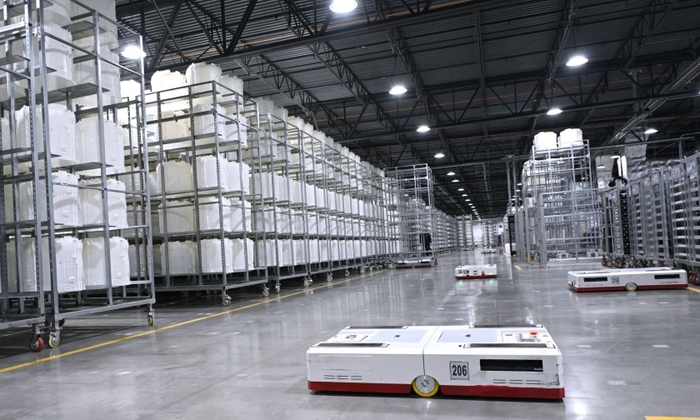
SK온도 스마트팩토리 전환으로 배터리 생산성을 끌어올리고 있다. 회사는 충남 서산 배터리 공장에 디지털 트윈 기술을 선제 도입한 뒤 미국과 헝가리 등 글로벌 생산 라인에 확대 적용할 방침이다. 가상 환경에서 실제 현장을 실시간으로 모니터링해 장비 보전 시간이나 운영비 등을 크게 절감할 수 있을 것으로 기대하고 있다.
또 국내외 협력사와 배터리 생산 장비 지능화도 전개하고 있다. 장비 제어를 관장하는 컨트롤러, 모니터링을 위한 스마트 센서 등 핵심 부품의 성능을 높이고, 네트워크 시스템을 발전시켜 장비 효율과 생산성을 끌어올린다는 전략이다.
배터리 업계 관계자는 “이차전지 생산 공정 기술이 안정화 단계에 접어들면 수율을 계속 높이는 것도 한계가 있다”며 “정보통신기술(ICT)을 활용한 생산성 개선으로 원가 절감과 제조 경쟁력 확보를 꾀하려는 것”이라고 말했다.
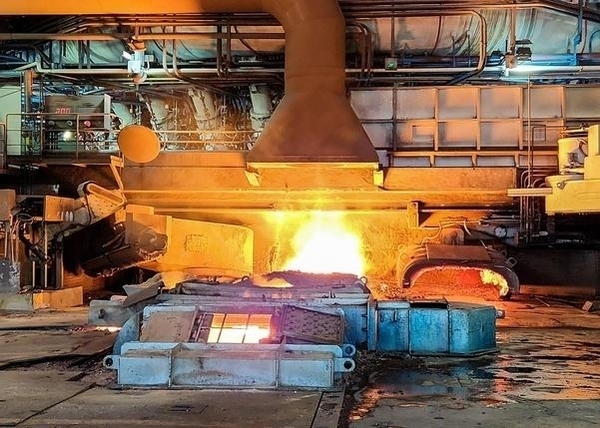
◇AI 적용 확대…“생산성 30% 개선 가능”
제조 공정에 AI를 적용하는 움직임도 활발하다. 생산성을 높이고 안전한 작업 환경을 조성하는 한편 원가 절감으로 가격 경쟁력을 확보할 수 있어서다. 한국전자기술연구원(KETI)에 따르면, 제조 현장에 AI를 도입할 경우 제품 결함과 제조 비용은 각각 60%와 30% 이상 줄 것으로 예상된다. 생선성은 30% 이상 끌어올릴 수 있다.

포스코는 AI가 연료와 원료 투입 비율을 최적화하고 통기성·출선·용선 온도 등 용광로 상태를 결정하는 변수를 파악하는 시스템을 도입했다. AI가 자동으로 최적의 결과값을 산출하면서 연간 쇳물 생산량이 8만5000톤 늘었다. 이는 승용차 8만5000대를 추가 생산할 수 있는 물량이다.
또 포스코는 제선·전로·압연 공정 등 고위험 설비에 AI 시스템을 적용, 작업자 안전을 확보하고 있다. 설비 상태를 실시간으로 모니터링해 고장을 예측하고 유지보수를 자동화하는 방식이다.
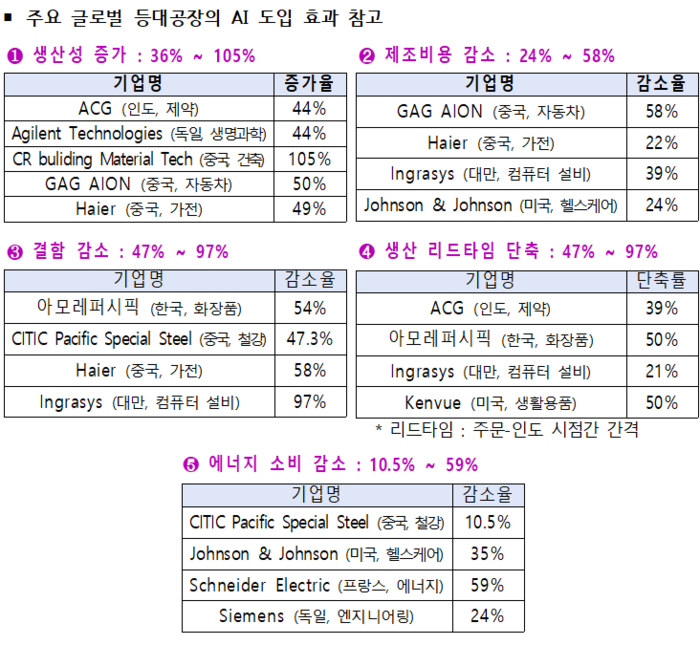
LG이노텍은 원자재 입고 시스템에 AI를 접목했다. 기존에는 공정 투입 전 원자재를 육안으로 검수했지만, 소재 정보 기술과 AI 영상처리 기술을 융합한 원자재 입고 검사 시스템으로 반도체 기판 불량 검출률을 높였다.
AI가 머신러닝으로 양품에 적합·부적합한 소재 구성을 형상화한 데이터 수만장을 학습하는 방식이다. 이를 기반으로 1분 만에 정확도 90% 수준으로 원자재 불량을 분석할 수 있다고 회사는 설명했다. 불량 원인 파악에 소요되는 시간은 기존 대비 90% 줄었다.
LG이노텍 측은 “불량 원인 해결을 위해 추가 투입되던 비용도 절감할 수 있게 됐다”며 “향후 원자재 입고 검사 AI 시스템을 반도체 기판 이외에 카메라 모듈 등 다른 분야로 확대 적용할 계획”이라고 밝혔다.
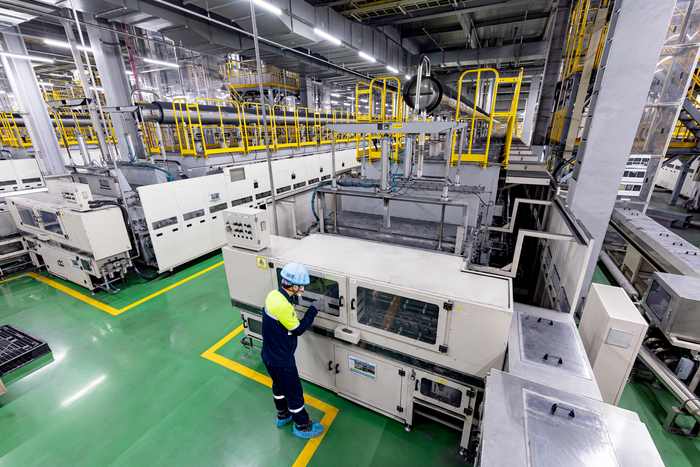
◇이차전지 소재사, 로봇 도입으로 물류 자동화·무인화 구현
배터리 소재사들은 생산 라인에 로봇과 무인운반차(AGV)를 도입, 물류 자동화를 꾀하고 있다. 작업자가 지게차로 원재료를 운반하는 기존 방식 대신 물류 무인화와 자동화를 구현하면 효율성을 높일뿐만 아니라 사고 위험도 줄일 수 있다.
포스코퓨처엠은 전남 광양 공장에서 양극재 샘플을 담는 용기의 운송을 자동화했다. 과거에는 작업자가 샘플을 들고 공장에서 품질 분석실을 오갔지만, 이제는 에어슈팅(공기 압력을 이용한 이송 장치)이 파이프라인을 따라 초당 5m 속도로 이동, 공장 내부를 1분 안에 이동한다.
샘플을 분석하는 공정이나 소모품인 용기를 교체하는 일도 사람이 아니라 로봇이 수행하고 있다. 로봇 팔이 입자 크기와 성분별로 샘플을 정확하게 계량해 측정 설비로 보내고, 용기도 폐기 처분한다. 포스코퓨처엠은 이를 통해 인력 활용 효율성을 높이고 작업자 근골격계 질환을 줄일 수 있다고 강조했다.
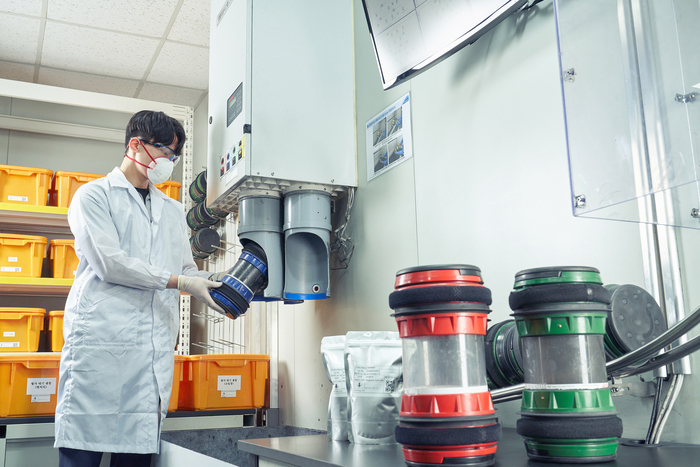
에코프로는 양극재 핵심 생산 거점인 포항캠퍼스를 자동화 솔루션을 갖춘 최첨단 공장으로 구축했다. 생산 라인에서 AGV가 원자재를 옮기고, 중앙 시스템에서 운반 과정을 모두 추적해 물류 효율성을 개선했다. 양극재 완제품을 이동형 대형 포장재에 담을 때 고객사별 정보를 부여하는 제품 라벨링도 사람이 아니라 협동로봇이 담당해 무인화를 실현했다.
업계 관계자는 “기존에 사람이 수행하던 일을 자동화하면 기존 인력을 고부가 업무에 재배치해 배터리 소재 품질과 안정성을 높일 수 있다”며 “이는 글로벌 배터리 시장에서 근본적인 경쟁력을 제고하는 방법이 될 수 있을 것”이라고 말했다.
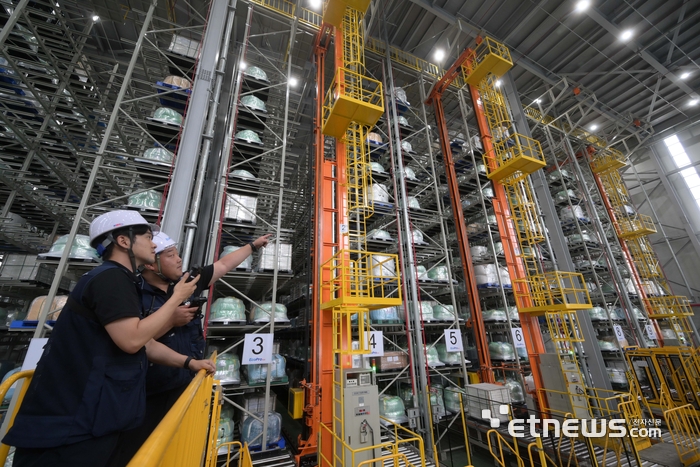
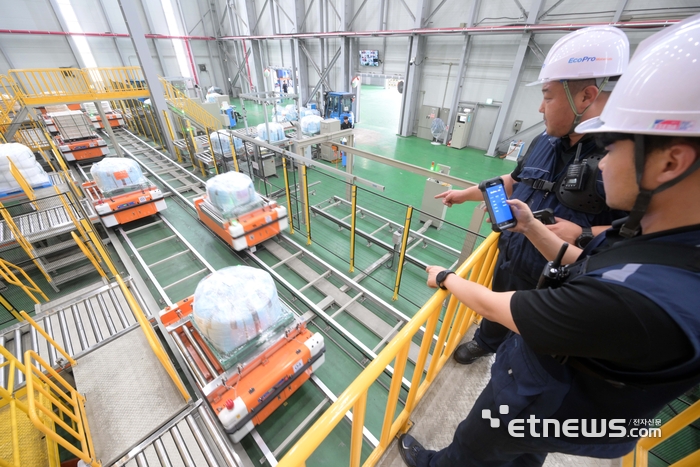
이호길 기자 eagles@etnews.com