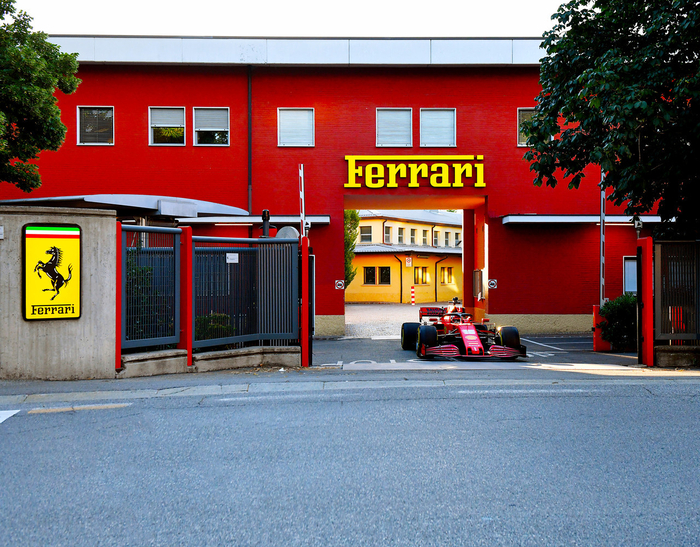
“페라리 마라넬로 공장은 꿈을 현실화해 전설을 탄생시키는 곳입니다.”
3일 방문한 이탈리아 북부 모데나도 인구 1만7000여명 소도시 마라넬로(Maranello). 세계적 스포츠카 페라리 본사와 연구개발(R&D) 시설, 공장까지 모두 이곳에 자리했다.
마라넬로 공장 관계자는 “1947년부터 페라리 차량을 생산한 역사적 공간”이라며 “단순한 자동차 공장을 넘어 페라리 브랜드와 설립자 엔초 페라리의 열정과 혁신을 담은 곳”이라고 소개했다.
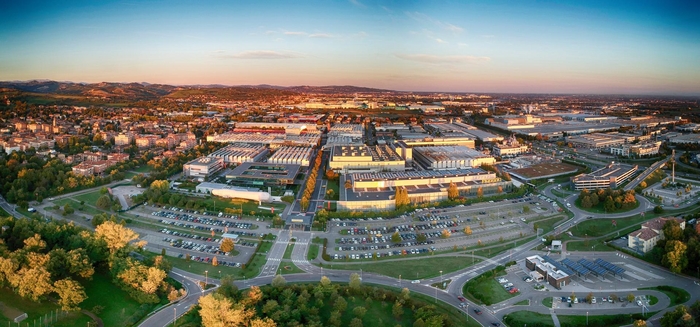
본사 인근 페라리 박물관을 비롯한 시승 체험장, 기념품 상점 등에는 평일에도 수많은 관광객으로 북적였다. 세계 최고 스포츠카 브랜드를 보유했다는 이탈리아인들의 페라리에 대한 자부심을 엿볼 수 있는 대목이다.
가장 먼저 찾은 곳은 페라리 차량의 핵심인 엔진을 만드는 '기계 공정관'이다. 약 1만5000㎡ 규모로 페라리 차량의 심장인 6기통과 8기통, 12기통 엔진 부품을 생산한다.
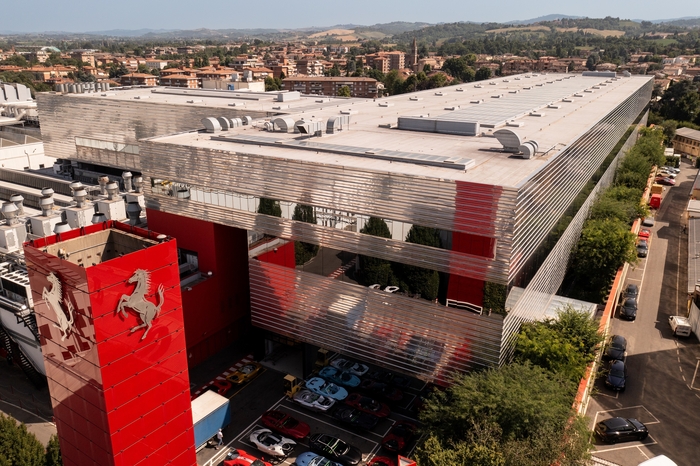
기계 공정관 관계자는 “엔초 페라리의 가장 큰 관심사는 엔진이었다”며 “'엔진을 만든 다음 바퀴를 달았다'라는 설립자의 말처럼 페라리는 외주 제작없이 모든 엔진을 직접 설계하고 만든다”고 설명했다.
페라리를 상장하는 빨간 작업복을 입은 공정별 테크니션들은 포뮬러1(F1) 레이싱팀 스쿠데리아 페라리의 경주차 'SF-25'부터 최신 슈퍼카 'F80'의 6기통 엔진을 탑재한 플러그인 하이브리드(PHEV) 시스템까지 부품별 조립 작업에 분주히 움직이고 있었다.
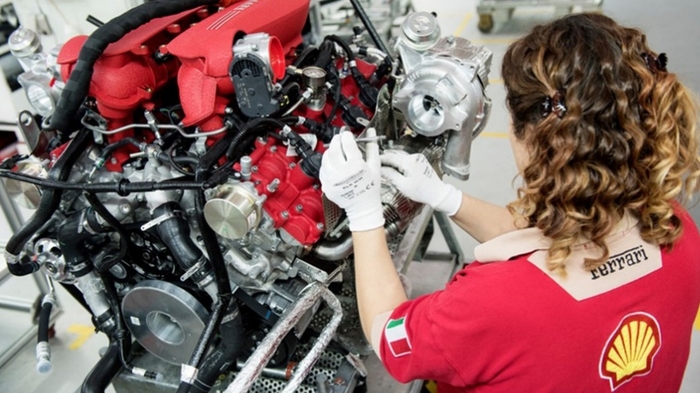
'엔진 조립관'에서는 엔진 조립에 필요한 부품들이 카트에 담겨 컨베이어를 따라 이동한다. 테크니션들이 각자 맡은 작업을 마치면 엔진이 완성된다. 엔진은 구동 이전 테스트벤치에서 점검한다.
다음은 '차체 용접 구역'으로 이동했다. 용접의 세 가지 주요 단계는 '라스트라투라(Lastratura)', '페라투라(Ferratura)', '리비지오네(Revisione)'다.
첫 단계는 기본 섀시를 적용, 측면 패널과 루프의 구조 부품을 용접한다. 두 번째는 도어와 프론트 후드 등을 추가하기 이전 표면을 세척하고 용접한다. 세 번째는 최종 품질 관리로, 특수 조명 아래 차량 내구성을 검사하고 용접 후 차량 표면을 점검한다.
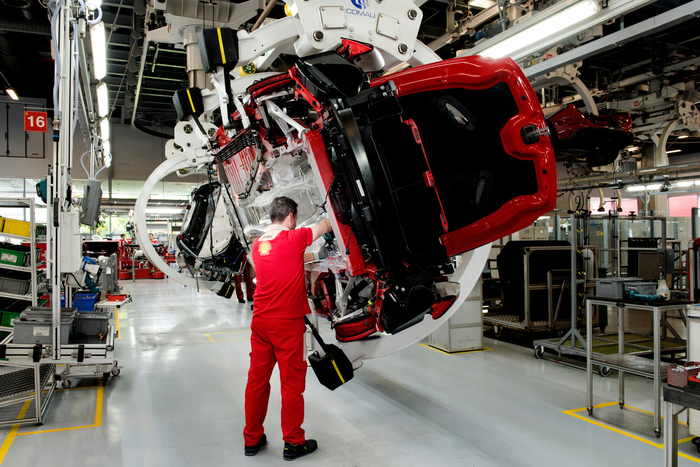
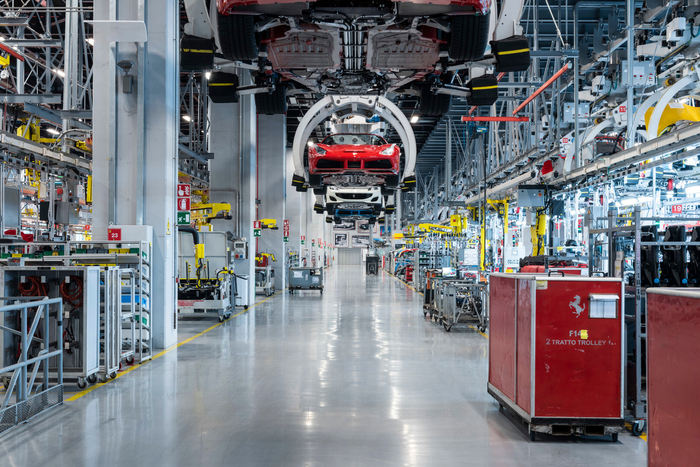
12기통 엔진의 용접 공정엔 자동화가 없다. 정밀하고 세심한 기술을 요구하기 때문에 전문가가 직접 작업한다. 용접은 두 개의 조각을 하나로 합치는 것이 아니라, 차체 자체가 하나의 완성된 형태가 되도록 진행한다.
마지막은 '차량 조립' 단계다. 테크니션들은 옷을 입히듯 엔진과 기어 박스, 전기 배선, 섀시, 실내 장식, 유리 등을 차량에 채워 넣는다. 차량의 차체와 섀시는 결혼식을 뜻하는 '일마트리모니오(Ilmatrimonio)'라고 불리는 공정을 통해 엔진과 결합된다.
탄소중립은 스포츠카를 만드는 페라리에도 핵심 과제다. 2030년까지 완전한 탄소중립 달성을 목표로 차량 생산부터 사용 단계까지 제품의 수명주기에 걸쳐 탄소중립을 이뤄낸다는 방침이다.
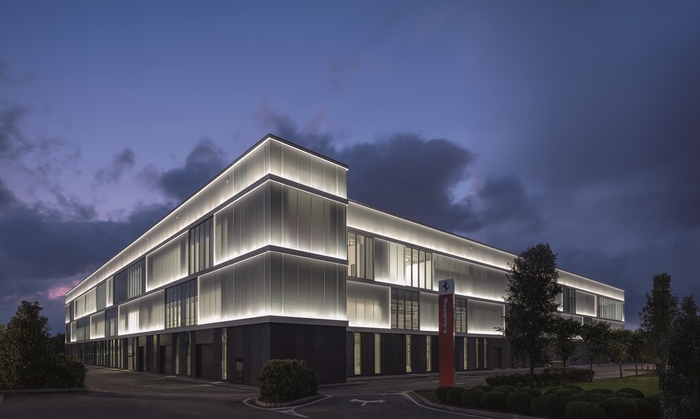
페라리는 전체 탄소 배출량의 15%를 차지하는 생산 공정 단계에서 탄소중립 공장으로 전환하기 위한 작업을 진행 중이다. 이의 일환으로 마라넬로 공장 내 1㎿ 규모의 고체산화물 연료전지공장을 건립했다.
공장 관계자는 “지난해 6월 내연기관과 하이브리드는 물론 페라리 최초의 전기차를 생산할 e-빌딩이 들어섰다”며 “e-빌딩은 지붕에 3000개 이상의 태양광 패널을 설치해 1.3㎿ 전력을 공급하며, 에너지원이 보증된 내외부 자원의 재생 에너지 전력만을 사용한다”고 말했다.
마라넬로(이탈리아)=
정치연 기자 chiyeon@etnews.com