케이지모빌리티 창원공장에
생산성 안전성 일석이조
'디지털트윈 혁신서비스 선도사업' 성과
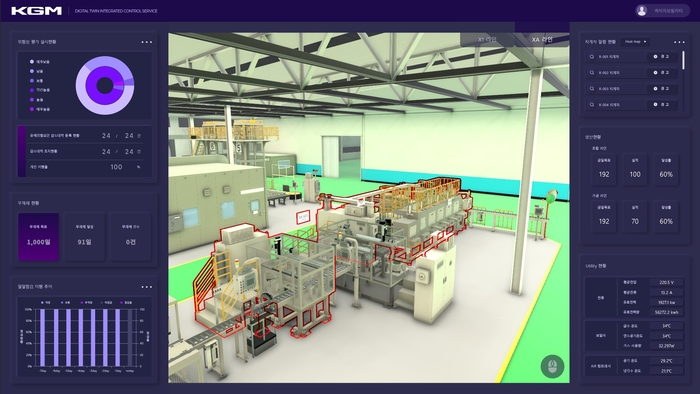
디지털전환(DX)전문기업 일주지앤에스가 자동차 엔진 생산라인을 디지털트윈으로 가상화하는데 성공했다. 단일 건물이나 제품을 디지털트윈 기술로 가상화한 사례는 있지만 디지털트윈 생산라인은 세계 처음이다.
일주지앤에스(대표 김정엽)는 '2024 디지털트윈 혁신서비스 선도(제조산업 적용실증)사업'에서 케이지모빌리티 창원공장 엔진 생산라인을 실사 수준으로 3D모델링해 생산에서 제어 관리, 안전성 확보까지 다각도로 활용할 수 있는 '디지털트윈 플랫폼'을 구축했다.
과기정통부와 정보통신산업진흥원(NIPA)이 지원하는 '디지털트윈 혁신서비스 선도(제조산업 적용실증)사업'은 디지털트윈 기술을 활용해 제조업 생산시설과 안전·운영(ESG)경영을 통합 관리할 수 있는 플랫폼을 구현하고, 특화서비스로 상용화하는 사업이다.
일주지앤에스는 이 사업에서 '제조현장 생산성 향상과 안전관리체계 구축을 위한 ESG 특화 디지털트윈 활용 실증 과제'를 수행했다. 과제 주관은 일주지앤에스, 케이지모빌리티는 참여기업으로 플랫폼 구축 실증 라인을 제공했다.
케이지모빌리티 창원 엔진공장은 디젤과 가솔린 엔진 6종을 생산한다. 현재 자동화율 50%에서 지속적인 첨단 시스템 도입으로 선도 스마트공장을 구현하고 있는 곳이다.
케이지모빌리티는 안정적인 엔진 조립 생산은 물론 상황 변화에 능동적으로 대처하고 세계적 추세인 ESG 경영에도 대응 가능한 최첨단 라인 운용 시스템이 필요했다.
생산라인 '디지털트윈 플랫폼'은 디지털트윈, 인공지능(AI), 클라우드, 사물인터넷(IoT) 등 최신 기술을 적용해 생산라인 작업 현황을 시각적으로 실시간 모니터링한다. 엔진 조립·생산 공정을 선제적으로 시뮬레이션해 공정 최적화 방안을 도출한다. 빠른 셋업, 비용 절감, 불량 감소 등으로 전체 생산성을 높여준다. 각종 장비 및 설비 가동 정보를 실시간 파악해 중대재해 사고를 예방할 수 있다.
일주지앤에스는 이 같은 플랫폼 기능을 4개 '디지털트윈 특화서비스'로 체계화했다.
'디지털트윈 통합 관제서비스'는 실사 3D모델링으로 생산라인 전반을 시각적으로 통합 관제해 이상 발생에 신속하게 대응할 수 있는 서비스다. 통합 관리로 생산 효율을 높이고 각종 설비 및 공정 데이터를 축적해 AI·빅데이터 분석 활용으로 연계할 수 있다.
'실증시설물 적용 안전 특화서비스'는 장비나 시설물 안전사고 발생 시 장소와 상황을 실시간 파악해 신속하게 처리할 수 있는 서비스다. 안전사고 발생 다발 지역 데이터 분석하고 사고 내역도 자동 등록한다.
'실증시설물 적용 제조 특화서비스'는 현장 인원의 공정별 재배치와 원가 절감 등에 활용해 생산 효율성을 최대로 끌어 올릴 수 있다. 물류 병목 현상을 비롯한 생산 효율성 저해 요인을 색출하고 해소 방안도 도출한다.
'실증시설물 적용 ESG 혁신서비스'는 실시간 안전 모니터링으로 중대재해 예방과 안전관리 업무를 고도화할 수 있다. 사업장 내 안전 점검, 비상 상황에 대응할 수 있는 체계 구축도 지원한다.
김정엽 대표는 “케이지모빌리티 창원공장 적용 및 실증 성과를 토대로 평택공장 등 다른 공장으로 플랫폼 적용 확대를 논의하고 있다”며 “창원산단 케이지모빌리티 협력사를 중심으로 산단 내 플랫폼 서비스 제공도 추진할 계획”이라고 말했다.
부산=임동식 기자 dslim@etnews.com