반도체 성능과 집적도를 높이기 위해 3차원으로 칩을 적층하는 3D TSV(반도체 칩에 전기적 연결을 위한 수직관통 구멍), 패키징과 팬아웃 웨이퍼레벨 패키징(FoWLP), 팬아웃 패널레벨 패키징(FoPLP) 기술을 향상시키고 효율화하려는 업계 노력이 지속되고 있다.
코스텍시스템(대표 배준호)은 FoWLP과 FoPLP에 모두 사용할 수 있는 반도체 팬아웃 패키지용 웨이퍼 임시 본더·디본더 장비인 '타우루스-300FOB(팬아웃 본더)'와 '타우루스-300FOD(팬아웃 디본더)'를 개발하고 국내 기업에 양산 적용했다. 전량 수입에 의존하는 장비여서 추후 국산화 성과 확대가 기대된다.

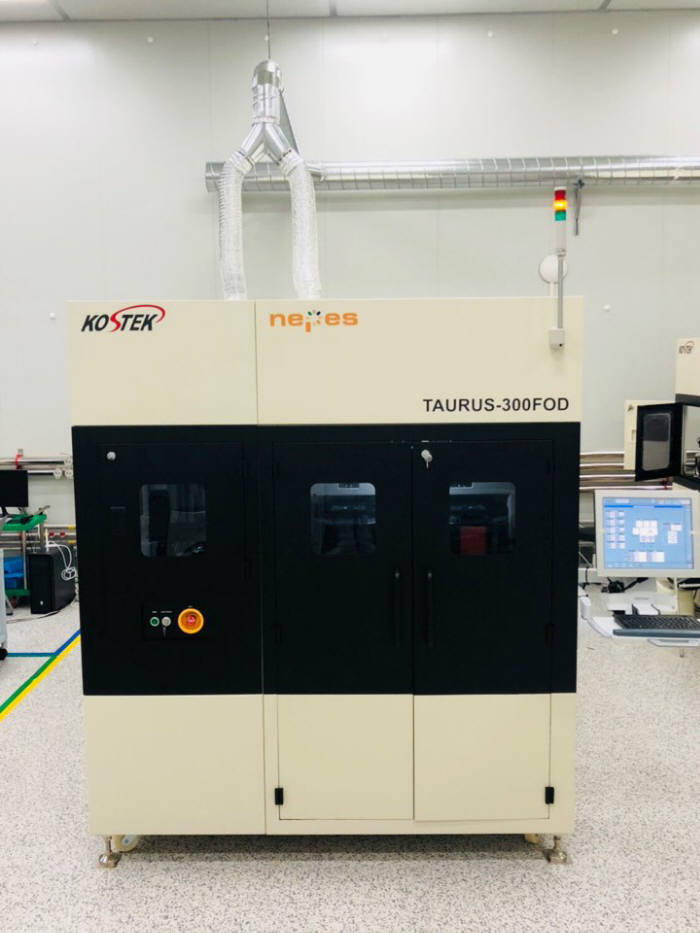
코스텍시스템의 웨이퍼 임시 본더·디본더 시스템은 팬아웃 패키징 공정에서 사용할 수 있다.
TSV 패키징은 여러 칩을 적층하기 위해 디바이스 웨이퍼의 후면을 갈아내고(백그라인딩) 칩을 관통하는 구멍을 뚫은 후 구리 배선을 연결한다. 이 과정에서 디바이스 웨이퍼가 휘지 않도록 지지대 역할을 해주는 캐리어 웨이퍼를 디바이스 웨이퍼의 앞면에 액상이나 필름 형태 임시 접착제로 부착한다. 이 때 본더 장비를 이용해 캐리어 웨이퍼를 부착해준다. 이후 디바이스 웨이퍼 후면을 갈아낸 뒤 배선과 범핑 공정이 끝나면 캐리어 웨이퍼를 떼어낸다.
팬아웃 패키징은 완성된 칩을 원형이나 네모 형태로 재배치하고 칩 바깥으로 배선을 빼내는 방식이다. 이 때 에폭시 몰딩을 하는 과정에서 웨이퍼 휨(Warpage) 현상이 발생하는 문제가 생긴다. 이 때문에 웨이퍼 후면에 캐리어 웨이퍼를 본딩해 휨 현상을 제거한 뒤 배선과 범핑 공정을 거치고 캐리어 웨이퍼를 제거한다.
코스텍시스템은 본딩 챔버 안에서 두 웨이퍼가 일치하도록 정렬하는 기술, 본딩 시 웨이퍼에 가하는 압력을 고르게 분포하는 기술, 웨이퍼 두께를 균일하게 유지하는 기술, 필름을 웨이퍼에 붙일 때 기포 등 빈 공간이 생기지 않도록 하는 기술 등 여러 핵심 기술을 자체 개발해 적용했다. 관련 기술도 다수 특허 출원해 등록했다.
이 본딩 기술은 마이크로LED 디스플레이 제조 공정에도 사용된다.
크기가 10~100마이크로미터(㎛) 수준으로 작은 마이크로LED를 제조하려면 웨이퍼 상에서 공정을 진행해야 한다. 지지대 역할을 하는 캐리어 웨이퍼를 본딩해 후속 패터닝 공정을 한다.
이 기술을 사용하면 마이크로LED 제조 공정에서 가장 어렵고 비용이 많이 드는 칩 전사공정에도 사용할 수 있다. 한 번에 수십만개 마이크로LED 칩을 동시에 전사할 수 있어 제조비용을 획기적으로 줄일 수 있다.
현재 국내 반도체 제조사 3D 칩과 인터포저(회로 기판과 칩 사이에 들어가는 기능성 패키지판) 제조 라인에 적용된 웨이퍼 임시 본더·디본더 장비는 전량 해외에 의존하고 있다. 독일, 일본, 오스트리아 기업이 이 시장을 장악했다. TSV 본더·디본더 장비는 1000만달러대 수준의 고가이고 반도체 공정에서 중요도가 높은 만큼 향후 수입 대체 효과를 기대할 만하다.
코스텍시스템은 이번에 양산 적용한 제품에 필름 형태 접착제를 사용했다. 액상 접착제를 적용한 장비도 개발하고 있으며 국내 기업과 양산·신뢰성 검증에 나설 방침이다.
코스텍시스템 관계자는 “FoWLP와 FoPLP 공정에 모두 적용할 수 있고 전량 수입에 의존하는 장비를 국산으로 대체할 수 있는데다 추후 TSV 패키징과 마이크로LED 패키징에도 적용할 수 있어 확장성이 기대된다”고 말했다.
배옥진기자 withok@etnews.com