현대자동차그룹이 전기자동차 핵심 부품인 배터리 시스템을 모듈화한다. 배터리 시스템을 모듈화하면 설계 유연성, 생산 속도, 원가 경쟁력을 동시에 높일 수 있다. 현대차그룹이 독자 개발한 차세대 배터리 시스템 모듈은 올해 현대·기아차가 출시할 2세대 장거리 전기차(주행 거리 300㎞ 이상)에 처음 탑재된다.
6일 업계에 따르면 현대차그룹은 올해 양산을 앞둔 2세대 장거리 전기차 신차 3종에 배터리 시스템을 모듈화해서 양산한다. 배터리팩 크기와 부피 등 규격을 통일, 여러 차종과 부품을 공유하는 방식이다. 배터리팩을 얹는 하부 프레임 부품도 일원화했다.
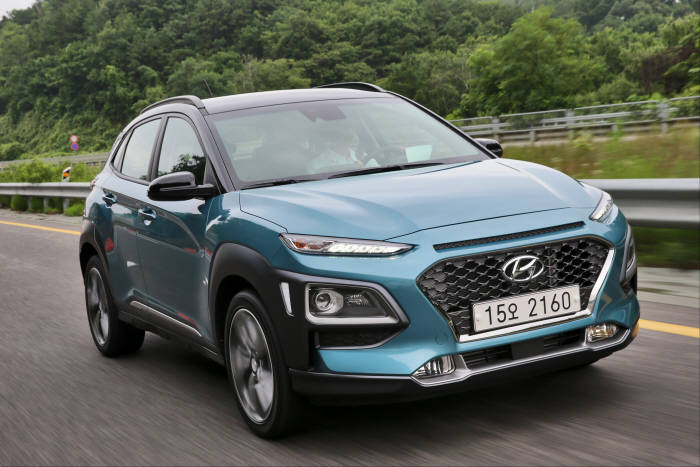
배터리 모듈화는 타 전기차 제작사도 진행하고 있지만 현대차는 한발 더 나아가 배터리 용량 5㎾h 이하 수준의 자체 모듈화를 통해 디자인 설계 등 유연성을 극대화했다. 배터리 채용에 따른 공간 활용은 물론 차량 무게 배분에도 유리하다. 전기차 전용 플랫폼이 아닌 내연기관차 플랫폼을 활용한 전기차의 약점을 보완한 전략으로 풀이된다.
배터리 모듈화로 현대·기아차 2세대 전기차는 주행 거리를 더 간편하게 줄이거나 늘릴 수 있다. 하부 프레임에 모듈화한 기본 배터리팩 탑재로 1회 충전 시 약 200㎞를 주행한다면 배터리팩을 추가했을 땐 400㎞까지 주행 거리를 늘리는 방식이다.
이를 통해 전기차를 도심 단거리용과 고속 장거리용 두 가지로 구분, 판매한다. 최근 예약 판매에 들어간 '코나EV'는 39.2㎾h 배터리(주행 거리 240㎞ 이상)를 탑재한 기본형과 64㎾h 배터리(390㎞ 이상)를 얹은 항속형 두 가지 모델로 출시된다.
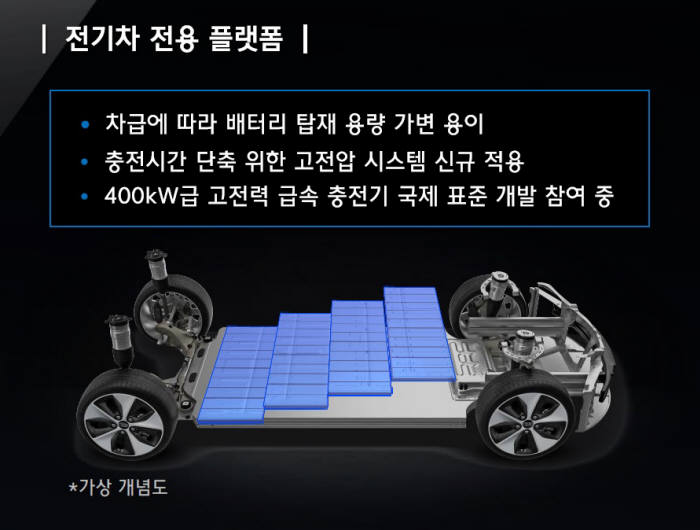
현대·기아차는 그동안 차종별 전용 배터리팩과 하부 프레임을 개발, 장착해 왔다. 그러나 배터리 시스템 모듈화로 기존의 내연기관차를 활용한 최적화 설계가 가능해졌고, 생산 효율성도 극대화됐다. 부품 생산과 재고 관리 등이 원활해져 원가 경쟁력도 높일 수 있다.
부품 모듈화는 현대차그룹이 글로벌 자동차 업체로 도약한 주요 배경으로 꼽힌다. 현대차그룹은 모듈화 전략을 통해 품질 개선, 생산성 제고, 원가 절감 측면에서 큰 효과를 거뒀다. 현대차그룹은 기아차를 인수한 1999년을 기점으로 생산 합리화 전략을 통해 자동차 공정의 주요 부분에 부품 모듈화를 도입했다.
이후 섀시 모듈, 운전석 모듈, 프런트 엔드 모듈을 생산하며 자동차 3대 핵심 모듈의 자체 생산 체계를 구축했다. 모듈화 전략에 힘입어 현대차그룹은 2014년 글로벌 판매 800만대를 돌파했다.
현대차그룹은 올해 배터리 시스템 모듈 생산 라인 증설에 속도를 낸다. 올해까지 배터리 시스템 모듈을 7만대 이상을 생산하도록 라인을 증설, 글로벌 전기차 시장 수요에 유연하게 대응할 계획이다.
현대차그룹은 부품 모듈화와 전기차 전용 플랫폼을 통해 2025년까지 글로벌 전기차 시장 톱3 진입을 목표로 한다. 지난해 2종에 불과하던 전기차 라인업을 2025년까지 14종으로 확대할 계획이다.
업계 관계자는 “전기차 부품 모듈화와 전용 플랫폼 전략은 이미 글로벌 자동차 업계가 추구하는 기술 트렌드로 자리 잡았다”면서 “전기차에 최적화된 플랫폼에 모듈화된 배터리팩과 모터를 결합하면 세단과 스포츠유틸리티차량(SUV), 스포츠카 등 다양한 차량을 양산할 수 있다”고 설명했다.
정치연 자동차 전문기자 chiyeon@etnews.com