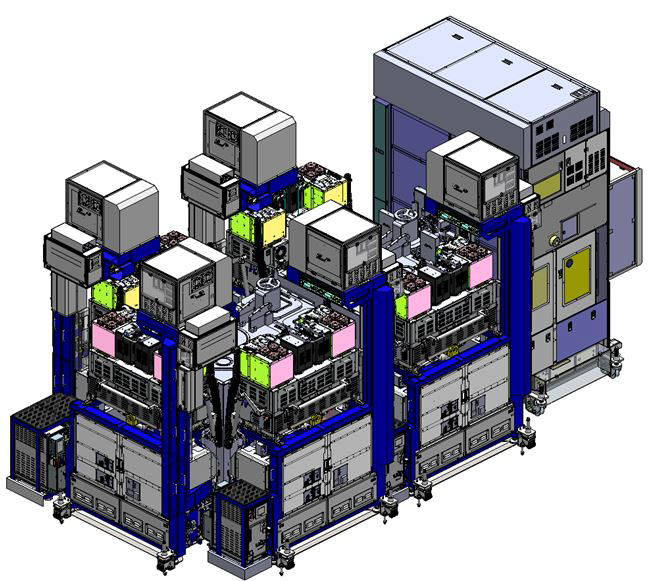
반도체 장비 업계에 `실시간 공정진단`에 대한 관심이 높아지고 있다.
원익IPS가 관련 분야에서 성과를 냈기 때문이다. 실시간 공정진단 기술이 적용된 원익IPS의 플라즈마화학기상증착장비(PECVD) `마하(MAHA) MLT 몰드` 시스템은 국내 고객사 3D 낸드플래시 핵심 생산 장비로 자리를 잡았다. 발 빠르게 기술 개발에 성공한 덕에 상당한 수입대체 효과를 거둘 수 있었다는 것이 장비업계 관계자 설명이다.
원익IPS는 이 분야 매출을 확대하기 위해 본격 나서고 있다. 최근 마하 MLT 몰드 장비 경쟁력을 높이기 위한 태스크포스(TF)를 꾸렸다. 고객사 시설투자가 3D 낸드플래시에 집중된 것을 감안, 관련 장비의 경쟁력을 해외 경쟁사 이상으로 높이기 위한 조치다. 원제형 부사장(반도체1사업본부장)이 TF팀 총괄장을 맡았다.
마하 MLT 몰드 시스템은 여러 층을 겹쳐 쌓아도 균일한 박막을 구현하는 것이 최대 특징이다. 3D 낸드플래시 구조는 흔히 아파트로 비유된다. 과거 2D 낸드플래시는 1층짜리 집이 횡 방향으로 건설되는 구조였다. 3D 낸드플래시는 위로 쌓는 종 방향이다. 핵심은 층간 균일성. 아파트는 천정 높이는 물론, 윗집과 아랫집 간 벽돌 두께가 균일해야 한다.
3D 낸드플래시도 마찬가지다. 그러나 증착 공정을 여러 회 수행하다 보면 웨이퍼뿐 아니라 웨이퍼가 가공되는 챔버 내에도 박막이 쌓여 내부 환경(임피던스) 변화를 야기한다. 이 때문에 동일 웨이퍼에서 박막 증착 공정을 여러 회 수행하면 막 두께가 두꺼워지는 경향이 있다. 한 장 웨이퍼 가공이 끝나고 난 후 다음 번 웨이퍼를 가공할 때는 박막 두께가 얇아지는 것도 문제다. 이런 문제를 해결하려면 증착 시간을 늘리거나 줄이는 등 보상 기법을 적용해야 한다. 그러나 눈으로 직접 볼 수 있는 아파트 건설 현장과는 달리 반도체 웨이퍼는 챔버 속에서 가공되기에 작업 종료 전까지 언제 어떻게 보상을 해야 될 지 알아내기 어렵다.
원익IPS는 박막 생성용 가스와 반응하는 플라즈마 상태를 실시간으로 모니터링하기 위해 시중에 나와 있는 다양한 센서 제품군을 하나씩 탑재해 보며 장기간 연구개발(R&D)을 진행했다. 플라즈마를 생성하는 RF 장치의 전압(V)과 전류(I)를 측정하는 VI 프로브를 챔버 위쪽에 탑재해 데이터를 축적했고 전기적 특성 변화 값을 분석해 적절한 증착 시간 보상 기법을 구현했다. 고객사는 이 장비 우수성을 호평했다.
현재 고객사 3D 낸드플래시 양산 라인에 공급된 마하 MLT 몰드 시스템은 VI 프로브를 통한 실시간 진단만이 가능하지만 플라즈마 빛 정도를 모니터링해 가스 흐름을 측정하는 OES(Optical Emission Spectroscopy) 센서와, SP-OES 센서를 활용하는 실시간 공정 진단 기술도 개발 막바지 단계에 접어들었다고 원익IPS는 밝혔다.
플라즈마 밀도 등을 직접적으로 분석하는 기법도 개발 중이다. 비접촉온도센서를 활용해 챔버 속 샤워헤드(가스가 나오는 곳)의 온도를 측정할 수 있는 기술도 내년 완료를 목표로 개발 중이다. 샤워헤드 온도를 측정하면 웨이퍼 박막 상태를 간접적으로 알 수 있다.
왕현철 원익IPS 선행기술파트장은 “궁극적으로는 웨이퍼 박막 두께를 직접 관찰할 수 있는 진단 기술을 구현하기 위해 R&D 역량을 높여나가고 있다”라면서 “국내 장비 업체가 해외 경쟁사를 누르는 궁극적 무기는 바로 이러한 실시간 공정진단 기술이 될 것”이라고 말했다.
이내일 원익IPS 선행설비개발팀장은 “기술 난이도가 높은 3D 낸드플래시 증착 장비에서 진단 기술을 완벽하게 개발해 두면 다른 장비로도 수월하게 관련 기술을 전파할 수 있을 것”이라고 말했다.
업계 관계자는 “국내 반도체 장비 실시간 공정진단 분야에선 원익IPS가 가장 발 빠르게 대응했고, 일정 부분 성과를 낸 것이 주목된다”라며 “최근 피에스케이도 이 기술에 대응하기 위해 전담팀을 꾸린 것으로 안다”라고 말했다.
한주엽 반도체 전문기자 powerusr@etnews.com