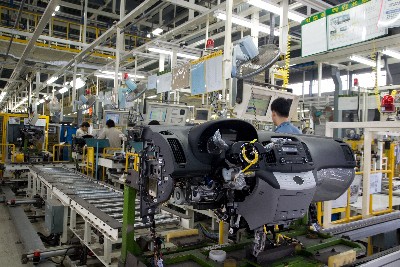
올해 회사 설립 32주년을 맞는 자동차 부품업체 덕양산업(대표 박용석 www.duckyang.co.kr)은 전형적인 제조업이면서 전 사업부문의 IT혁신(이노베이션)을 통해 나날이 고성장하고 있는 대표적 기업이다.
전세계적인 자동차산업 동반 침체를 딛고, IT활용을 통해 새로운 성장 기회 창출에 나섰다.
자동차 내부 크래쉬패드에 들어가는 속도계 같은 계기판류와 오디오, 내비게이션 등의 전장 부품류, 공조 부품 등을 생산하는 덕양산업은 자동차 부품업계에서도 드물게 JIT(Just In Time)시스템을 한 단계 더 발전시킨 JIS(Just In Sequence) 생산시스템을 운영하고 있다.
‘JIS시스템’은 자재관리, 생산관리, 품질관리 등 생산과 관련된 모든 프로세스가 완성차 제조사인 현대자동차를 비롯해 전 협력업체와 함께 연동됨으로써 생산라인의 모든 정보를 실시간으로 공유하고 생산 효율성도 높일 수 있는 핵심 인프라다. 이러한 JIS 시스템을 효율적이고 체계적으로 관리하기 위해서는 협력 업체 네트워크간 협업 IT시스템 구축이 필연적으로 수반된다.
콕핏모듈(Cockpit Module)은 최대 1400종에 이르는 다양한 사양의 제품을 90∼140분 정도의 짧은 사이클타임에 맞춰 공급해야하는 까다로운 생산 특성을 갖고 있다. 덕양산업은 지난 99년 에쿠스의 콕핏모듈 생산에서부터 현재의 아이서티(i30)용 콕핏모듈 양산까지 생산관리부문과 전산부문에서 많은 시행착오를 겪었다. 시행착오를 겪으면서도 IT를 기반으로 한 다양한 이종(異種) 및 결품(缺品) 방지시스템 구축을 포기하지 않았고, 끈질기게 밀어붙여 지난 2006년 아반떼HD 콕핏모듈 양산과 함께 RFID시스템을 본격 가동하게 됐다.
이를 통해 연간 6억원의 인건비를 절감하는 성과를 얻었다. 조립 및 검사 보조공수가 줄어 생산성도 향상됐다.
공수는 1224초/대에서 1146초/대로 6.4% 감소했으며, 전체적인 공정 불량률도 90%까지 줄일 수 있었다. 실제로 RFID기술을 적용하기 이전에 이종조립 발생은 시간당 7건 발생하였으나 RFID기술을 적용한 이후에는 시간당 3건이 발생하는 수준이다.
JIS시스템을 효과적으로 관리하기 위한 MES(Manufacturing Excution System) 구축을 통해 공정 진행 정보 모니터링 및 컨트롤, 설비제어 및 모니터링, 품질정보 트래킹 및 관리, 실적정보 집계, 창고운영 관리, 재공품 관리, 자재투입 관리, 인력관리, 공무 관리 등 생산 현장에서 발생할 수 있는 모든 정보를 통합 관리하는 시스템을 갖췄다.
이를 통해 자재보유시간을 기존 15시간에서 5시간으로 단축시켰으며, 자재 재고 회전율도 30%에서 84%로 향상 시켰다. SCM 구축으로 협력업체와 실시간 납입정보 및 결품 예측 정보를 공유할 수 있게 됐다.
덕양산업 관계자는 “더욱 완벽한 시스템을 구축하기 위해 지난해 MES서버를 이중화하는 대대적인 프로젝트를 성공적으로 수행했다”며 “완벽한 품질에 도전하는 기업으로서 IT이노베이션 활동을 지속적으로 전개해나갈 계획”이라고 말했다.
이진호기자 jholee@etnews.co.kr