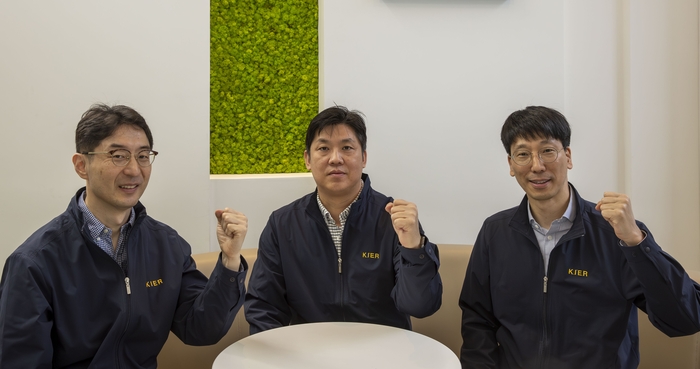
한국에너지기술연구원은 바이오자원순환연구실의 전상구 박사팀과 안정오 한국생명공학연구원 바이오상용화지원센터 박사 공동 연구팀이 가정용 혼합 폐플라스틱을 재활용해 고부가 플라스틱 원료인 '디카르복실산' 생산 기술을 개발했다고 24일 밝혔다.
플라스틱은 석유, 천연가스 등 화석연료를 통해 생산되며 폐플라스틱은 분쇄하고 녹여 새 제품을 만드는 방법으로 재활용된다. 하지만 생산·가공 과정에서 폐수와 유해물질이 방출돼 환경에 심각한 영향을 미치고 있다.
문제를 해결하고자 많은 국가와 기업이 플라스틱 순환 경제를 구축하기 위해 노력 하고 있다. 최근에는 열분해와 같은 화학적 방법을 통해 친환경적으로 플라스틱을 재활용하는 기술이 주목받고 있다.
그러나 열분해 방식도 완벽한 해결책은 아니다. 열분해 시 나오는 열분해유 중 30%의 나프타 성분만 플라스틱 원료로 재활용되고 대부분은 연소 과정에서 온실가스를 배출하는 저급 연료로 활용되기 때문이다.
연구진은 화학적 공정과 생물학적 공정이 결합된 융합 공정을 제시했다. 열분해유를 저급 연료로 쓰는 대신 미생물 반응 공정 원료인 '노르말 파라핀'으로 정제하고 이를 미생물 먹이로 활용해 플라스틱 원료를 생산하는 방식이다.
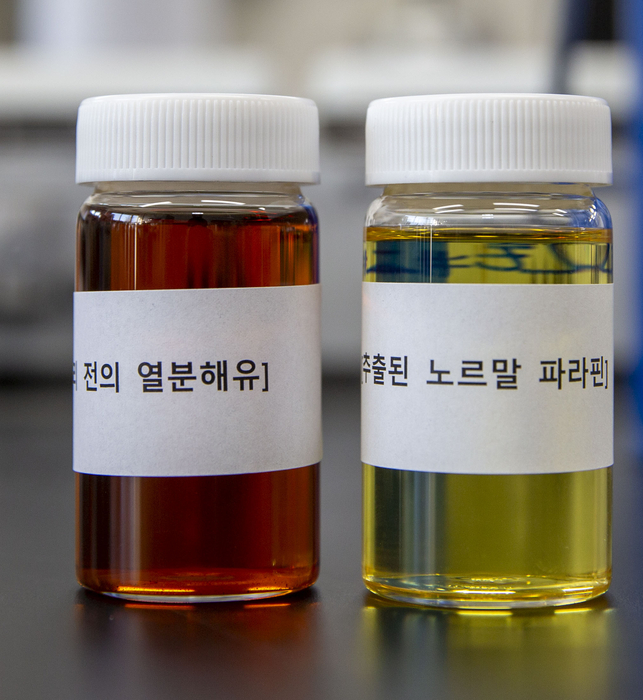
에너지연이 개발한 화학적 전처리 기술을 이용하면 열분해유에서 노르말 파라핀만을 선택적으로 정제할 수 있다. 열분해유를 수소로 가득 찬 400도 고온 환경에서 촉매와 반응시키면 불순물과 독성이 제거돼 노르말 파라핀으로 전환된다.
이후 정제된 노르말 파라핀을 미생물 먹이로 활용하면 폴리에스터(PES), 폴리아미드(PA), 폴리우레탄(PU) 등 고부가 플라스틱 원료인 디카르복실산으로 최종 전환된다.
연구진은 기술 활용을 통해 플라스틱 원료 생산 비용을 기존 석유화학 기반 생산 기술 대비 최대 40%까지 절감할 수 있을 것으로 예측했다.
또 열분해유 중 저급 연료로 활용되는 양의 30%를 플라스틱 원료로 재활용할 수 있어 국가 온실가스 저감에도 유리하다.
전상구 박사는 “이번 기술은 기존 화학적 플라스틱 재활용 방법 한계를 극복한 기술로 플라스틱 순환 경제 구축과 탄소중립 실현에 크게 기여할 수 있는 성과”라며, “최종 생산된 디카르복실산을 이용해 플라스틱을 합성하는 검증 절차를 진행하고 있으며 수요기업과의 교류를 통해 기술이전 및 사업화를 추진할 예정”이라고 밝혔다.
한편 이번 연구는 산업통상자원부의 산업기술 알키미스트 프로젝트 사업으로 수행됐으며 연구성과는 에너지 환경분야 세계적 권위지인 '저널 오브 클리너 프로덕션(IF 9.7)'에 게재됐다.
김영준 기자 kyj85@etnews.com