〈편집자주〉 탄소소재는 미래 먹거리다. '첨단 산업의 쌀'로 평가 받는 탄소섬유를 비롯해 인조흑연, 활성탄소, 카본블랙, 탄소나노튜브, 그래핀 등이 모두 탄소소재다. 그 자체로 중요 산업일 뿐만 아니라 도심항공교통(UAM) 등 첨단 전략산업을 뒷받침하는 소재라는 점에서 중요성이 커지고 있다. 전 세계 탄소소재 시장 규모는 2030년 1070조원까지 연평균 11.3% 성장할 것으로 전망된다.
국내 탄소소재 경쟁력 강화를 위해 산업통상자원부는 'K-카본 플래그십 기술개발 사업'을 출범시켰다. 우주·항공·방산, 모빌리티, 에너지·환경, 라이프케어, 건설 등 5대 주요 산업에 사용될 탄소소재 핵심 기술을 5년 내에 확보하는 것이 목표다. 올해부터 2028년까지 1046억원의 사업비가 투입된다. 전자신문은 탄소소재 산업 경쟁력 확보를 위해 한국탄소나노산업협회와 함께 4회에 걸쳐 K-카본 플래그십 기술개발사업의 주요 내용과 목표를 조명한다.
에어버스 초대형 항공기 A380에 투입되는 소재 중 절반은 탄소복합소재다. 과거에는 항공기 소재의 90%가 금속이었지만 안전과 저에너지소비가 강하게 요구되면서 고강도·경량 부품을 만들기 위한 탄소복합소재 적용이 확대되는 추세다.
항공·우주 산업 핵심으로 떠오른 열가소성 탄소복합소재를 효율적이면서 경쟁력 있게 만들기 위한 공정 기술 개발이 추진된다. '열가소성 탄소복합재 기반 3-in-1 자동화 공정 기술개발' 사업이다. 고속 사출, 압축, 압출을 동시에 수행하는 '3-in-1' 복합 성형 시스템 개발을 목표로 한다.
탄소복합소재는 탄소소재와 다른 재료를 조합해 단일 재료보다 더 우수한 물성을 나타내는 재료를 말한다. 기본 형태를 유지하기 위한 바탕재료(모재)에 탄소섬유 같은 고성능 재료를 강화재로 써서 만든다. 탄소섬유복합재(CFRP)가 대표적이다.
탄소복합소재를 만드는 과정은 고속 사출, 압축, 압출 공정을 거친다. 현재는 고온혼합압출기, 사출성형기, 프레스 등 개별 성형 장비에서 각각 공정이 진행됐다. 그러다보니 소요되는 시간과 비용이 많이 들었는데 사출, 압축, 압출을 동시에 하게 되면 공정을 크게 단축해 생산성을 끌어 올릴 수 있다.
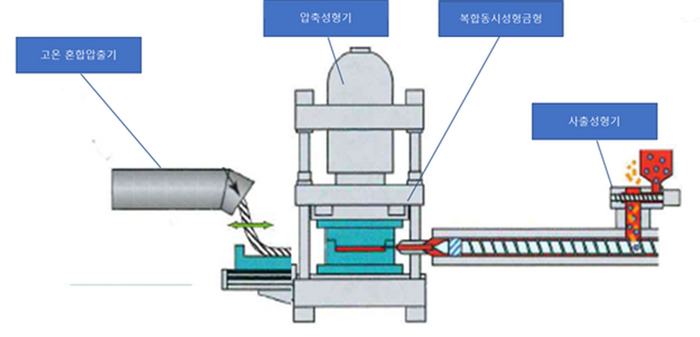
압축성형기, 고온혼합 압출기, 사출성형기 등 각 성형장비 구동 방식이 다르고 소재 특성도 다양하기 때문에 개발 난이도가 높다. 하지만 상용화에 성공한다면 우주항공을 비롯해 모빌리티, 에너지, 방산, UAM 등 분야에서 공정 절감에 따른 부품 가격 경쟁력 확보가 가능할 것으로 기대를 모은다. 대부분 수입에 의존하는 고가의 복합소재 성형장비 수입 대체도 가능하다.
또 이번 프로젝트는 공정 개발에만 그치지 않고 실제 이 공정을 활용해 발사체 인터탱크(Intertank)의 뼈대 역할을 하는 부품 '스트링거(Stringer)' 시제품도 제작할 계획이다. 과제는 삼연기술을 주관기관으로 일지테크, 한국탄소나노산업협회, 전주대, 한국탄소산업진흥원, 경북하이브리드부품연구원이 공동연구개발기관으로 참여, 상용화에 도전하고 있다.
박종수 한국탄소나노산업협회 회장은 “열가소성 탄소복합재 자동화 공정기술과 대량 양산 기술이 확보되면 항공·우주 산업 경쟁력을 향상시킬 수 있을 것”이라며 “특히 경량화 요구로 적용이 확대되는 탄소복합재 제품화, 상용화가 확산될 것으로 기대된다”고 말했다.
정현정 기자 iam@etnews.com