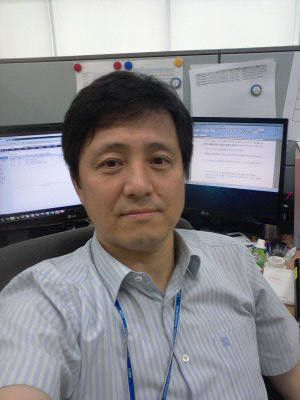
3D프린팅 기술은 원하는 형상을 정밀하게 구현할 수 있는 기술로 대량생산을 위한 제품 기술이 아닌 소량의 맞춤형 제품 생산에 적합하다. 또 금형을 활용하는 전통적 제조 기술과 달리 설계자가 원하는 형상을 직접 구현하거나, 제품 형상에 개인의 창의적 디자인과 아이디어가 결합될 수 있어 나만의 독창적 제품을 제조하기에 적합한 혁신기술이다.
도입 초창기에 3D프린팅은 제조된 물체의 표면이 거칠어 추가적인 후처리가 필요했지만 금형 제작 없이 신속한 조형물 제조가 가능해 도입이 이뤄졌다. 이후 소재와 장비 기술의 비약적 발전으로 정밀도가 향상됐고 적용되는 소재가 확대되면서 응용 범위도 넓어졌다. 최근엔 주얼리와 미니어처, 정밀 금형, 전기자동차 외형, 축구화, 의류, 인체의 장기, 화장품, 건축물, 악기, 식품과 육가공에 이르기까지 다양한 분야에 활용된 사례가 나오고 있다.
고열로 플라스틱을 녹여 분사하는 저가형 압출적층방식(FDM) 프린팅 장비의 보급으로 일반인도 장비를 활용하게 되면서 대중적 관심이 커졌다. 고출력 레이저로 금속분말을 녹여 원하는 형상의 부속품을 만드는 선택적 레이저소결 조형방식(SLS) 기술이 도입되면서 산업현장에선 타이타늄, 스테인리스 스틸 등의 금속 재료로 인공관절, 비행기·자동차 부품으로 활용 영역이 확장되고 있다. 저출력 광기술이 플라스틱 성형 기술에 도입되면서 정밀 금형제조에도 적용할 수 있게 됐다.
광기술과 잉크젯 기술이 결합한 플라스틱 기술은 여러 가지 색상으로 3차원 형상 제조가 가능해 패션형 헬멧과 맞춤형 신발 등의 제조 기술로 활용되기도 한다. 세라믹 분말로 형상을 만들고 고온에서 굽는 공정을 거치는 3D프린팅 세라믹 기술은 제트엔진의 터빈과 같은 고온용 부품과 의료용 뼈 조직을 구현하는 수준까지 시연되고 있다.
최근 무인 비행기와 웨어러블 제품에 3D프린팅 기술이 적용되는 등 항공·전자기기 영역까지 응용분야가 확장됐다.
그럼에도 아직 3D프린팅 기술은 산업적으로 괄목할 만한 성과를 못 내고 있다. 활용도를 높이기 위해 해결해야 할 선결과제가 몇 가지 있기 때문이다.
우선 3D 프린팅용 저가 소재의 개발이 절실하다. 외산에 의존하는 고가의 프린팅 소재로 다양한 제품을 생산하기는 어려운 상황으로 이를 해결하기 위한 경제적인 소재 확보가 무엇보다 시급하다. 다음으로 3D 프린팅 소재의 신뢰성 문제다. 3D 프린팅용 플라스틱 소재만 하더라도 종래의 금형 제조 소재에 비해 내구성이 떨어진다. 제품에 바로 적용하기엔 무리가 있다.
마지막으로 3D프린팅 소재의 다양성 부족이다. 3D프린팅을 이용하려는 소비자는 금속과 플라스틱이 복합적으로 동시에 구현되거나 인공장기와 유사한 감촉·물성을 지닌 플라스틱, 금속, 세라믹 재료 등을 요구하고 있다.
하지만 현재 상용 소재의 종류와 공정기술의 한계로 이 같은 소비자 요구를 충족하기 어려운 상황이다.
3D 프린팅은 개인용 맞춤 제조기술의 특성이 강하다. 사람들의 다양한 요구를 만족시키기 위해 현존하는 소재의 물성값을 충족해야 하는 것은 어쩌면 당연한 일이다. 국가적으로도 3D프린팅 기술의 후발 주자로서 핵심소재 기술 확보가 무엇보다 시급히 요구된다.
앞으로 전 세계적으로 활용되는 압출적층방식, 선택적 레이저소결 조형방식 그리고 광경화수지 조형방식 기반의 핵심 소재 기술과 차세대 3D프린팅 공정에서 활용될 다양한 원천 소재기술 확보가 핵심이다. 이를 바탕으로 3D프린팅 제조 기술의 혁신과 나아가 우리나라 제조 산업의 혁신을 주도해야 한다.
이우성 전자부품연구원 전자소재응용연구센터장 wslee@keti.re.kr