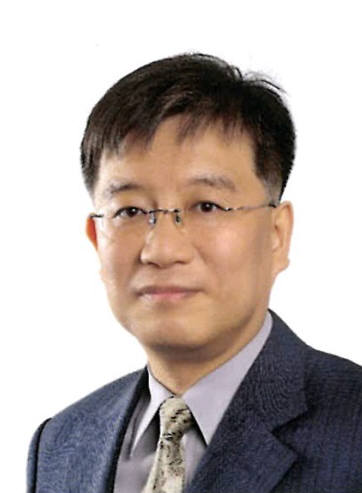
강하면서 가볍고 환경 친화적인 재료들이 철강을 대체하며 주목받고 있다. 대표적 재료 중 하나가 탄소섬유 복합재다.
탄소섬유복합재는 탄소로만 구성된 머리카락 굵기 10분의 1인 섬유로 형상을 짜서 만들고 여기에 고분자 수지를 입혀 만든 강하고 가벼운 재료다. 경주용 자동차, 첨단 항공기, 고가의 자전거나 스포츠용품을 만드는 데 주로 사용된다. 연간 6만톤 정도가 생산되고 있으나 기술이 발전함에 따라 사용량이 수십배 확대될 것으로 기대되는 재료다.
우수한 품질의 탄소 섬유를 값싸게 만들 수 있는 기술을 개발하고 복합재료를 대량으로 만들 수 있다면 시장을 선점할 수 있다. 선진 업체 간 치열한 경쟁이 펼쳐지고 있다. 이 때문에 많은 업체나 기관이 관련 공장과 연구소를 외부에 개방하지 않는다. 기술 개발 내용 역시 철저히 보호한다.
우리나라는 탄소 섬유를 국산화하려는 노력을 1990년대 본격적으로 시작했다. 지난해부터 태광, 효성 등에서 3000여톤을, 도레이첨단소재 구미공장에서 2700톤을 생산하기 시작했다. 조만간 우리나라에서만 1만톤 생산시대가 열릴 전망이다.
2012년까지만 해도 국내 수요인 연간 2700톤을 일본 도레이 등 해외 업체에서 전량 수입했다. 이를 바탕으로 국내에서 7억달러 규모의 복합재료와 부품을 제조했다. 앞으로 탄소섬유 공급이 국내 수요의 4배를 넘어서면 심각한 공급과잉도 나타날 수 있다.
탄소섬유를 이용해 탄소섬유강화복합재를 만들면 가격이 10배 이상 뛴다. 주요 부품을 만드는 때에는 30~40배의 부가가치가 만들어진다. 전형적인 고부가가치 기술 집약적 산업인 것이다.
우리나라에서 진행하는 우주항공산업, 친환경자동차 등에 가장 중요한 핵심 소재를 자급할 수 없다면 첨단 산업에서의 경쟁력을 확보할 수 없다.
고강도 경량소재인 탄소섬유복합재료가 사용되는 현재의 주요 용도는 자동차, 항공기 등 수송기기들이다. 이들은 안전이 가장 중요하다. 운행 중에 파손되지 않아야 하기 때문에 재료의 신뢰성 확보가 중요하다. 기존 재료를 탄소섬유복합재로 대체하기에는 초기 비용도 많이 든다. 이러한 이유로 전문 중소기업만으로 관련 시장을 확대하기 어렵다.
탄소섬유복합재 분야 시장을 국내에서 먼저 조성하고 이를 기반으로 원천기술을 확보한 우수한 전문 기업을 육성해야 한다. 대폭 확대되는 탄소섬유 및 복합재의 세계 시장을 이끌어갈 수 있도록 해야 한다.
탄소섬유복합재 시장은 2012년 12조원 규모에서 2030년에는 100조원으로 대폭 확대될 것으로 예상된다. 탄소섬유복합재 시장을 선점하기 위해 선진국에서도 미래 전략소재 산업으로 육성하기 위한 정책을 추진하고 있다. 우리나라도 탄소섬유복합재 관련 민간 기업들이 선도적으로 투자할 수 있는 여건을 만들고, 복합재가 사용될 수 있는 시범사업 ‘탄소섬유복합재료’ 플래그십 프로젝트도 시작됐다.
택시와 버스에 사용되는 천연가스압력용기, 승용차용 파노라마 선루프 프레임과 프런트 모듈, 범퍼 백빔, 국내 개발 항공기에 탄소섬유복합재를 활용하기 위한 시범사업으로 1조3000억원 정도의 탄소섬유복합재 시장이 새로 만들어질 수 있다. 이 사업이 우리나라가 탄소섬유 및 복합재료 분야의 경쟁력을 확보하고 글로벌 시장을 선도하는 데 기여할 것으로 기대한다.
홍경태 KIST 미래성장동력 첨단미래소재추진단장 kthong@kist.re.kr