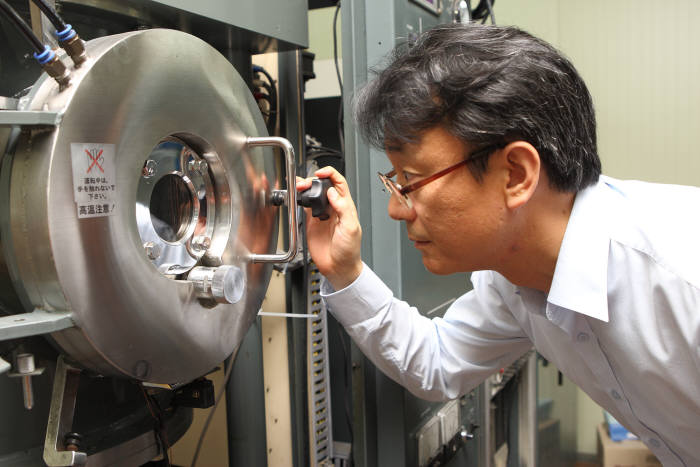
열 에너지를 동력으로 바꿀 때 손실 되는 에너지는 연료가 갖고 있는 총 에너지의 절반이 넘는다. 자동차 엔진도 마찬가지다. 미국 도로교통안전국의 지난 2011년 발표에 따르면 연료 에너지를 100%로 봤을 때 엔진에서 사용하는 에너지는 약 19%, 손실 열량은 62%가 넘는다. 연료에 응축된 에너지를 최대한 끌어내 효율을 높이는 게 자동차 업계의 영원한 숙제다. 소비자는 기름 값을 줄일 수 있고, 이산화탄소(CO2) 절감 효과도 누릴 수 있다.
연비를 높이는 다양한 방법 중 하나가 엔진 내부 벽을 덮는 코팅 재료를 바꾸는 것이다. 실린더 표면이 매끈해지면 엔진이 구동될 때 내부 마찰이 줄어 에너지 소비량이 줄어든다. 밸브 트래인(Valve Train) 등 부품끼리 맞닿는 부분 마모도를 줄여 부품 내구성을 개선하는데도 도움이 된다. 만약 마찰계수가 0.001이라면 10톤 무게를 10kg·f의 힘으로 움직일 수 있다.
◇연비 효율 높이는 저마찰코팅
지금까지 자동차 업계는 DLC(Diamond-Like Carbon) 코팅을 사용해왔다. DLC는 열과 산화에 약해 고온 엔진 내부에서는 오래 견디지 못한다.
한국생산기술연구원 신승용 박사팀은 박막을 나노 결정구조로 만들어 무른 성질을 가지면서도 단단한 소재를 개발했다. 원소, 연질 금속, 마찰계수를 낮추는 원소를 섞어 나노복합 코팅막 소재를 합성했다. 이 물질들은 서로 잘 섞이지 않고 표면을 균일하게 처리할 수 없는 한계가 있었다. 그래서 생각해 낸 아이디어가 일종의 금속유리분말(Metallic glass powder)을 만드는 것이다. 다양한 물질을 혼합해 타겟(미세한 금속과 얇은 반절연막을 포갠 구조) 물질로 합금한 뒤 급속 냉각 시키면 액체가 가지는 균일한 조성을 그대로 갖게 된다. 이렇게 만든 합금 분말에 압력을 가해 가열하면 비정질금속 덩어리를 만들 수 있다. 이를 재가공한 뒤 스퍼터링 공정을 가하면 연질 금속이 함유된 나노구조 코팅 소재가 합성된다. 4개 이상 원소가 쓰인 모물질을 개발하고 융복합 공정을 통해 고속 증착 기술을 확보했다. 만들어진 물질과 공정을 이용해 코팅막을 형성시켰다.
개발된 소재는 DLC 코팅막과 경도가 동일하지만 마찰계수는 3분의 1 내지 4분의 1로 낮다. 증착 속도는 5배 이상 빠르고 막 두께도 20μm 이상 두껍다. 50℃ 이하 저온 코팅도 가능하다.
◇7500억원대 나노코팅 시장
미국은 오는 2016년부터 연비 16.6km/l 이하 자동차 판매를 금지 했다. 5년간 석유 소비량을 18억 배럴 줄이고 배기 가스가 9억톤 감소하는 효과가 있다. 석탄 화력발전소 기준 194기를 폐쇄한 것과 마찬가지다. 미국 외에도 세계 각국이 자동차 연비 규제에 나서면서 연비 절감 기술이 가장 중요한 경쟁력이 되고 있다.
저마찰 코팅 기술은 상용 제품 개발단계에 있다. 타겟 물질을 대량 양산해 희성금속 등 타겟 업체와 동양피스톤, 유성기업 등 부품 업체, 현대자동차가 협력해 신뢰성을 평가할 예정이다. 이 외에 기존 코팅 업체들도 참여한다. 신승용 박사는 “1단계 소재 개발에 이어 2단계 상용화 사업을 추진하고 있다”며 “조만간 상용화 업체 선정이 완료될 것”이라고 설명했다.
일본 야노경제연구소에 따르면 오는 2015년 수송 분야 다기능 나노 복합 코팅 시장은 국내에서만 7500억원 규모로 예상된다. 차세대 공구·금형 소재, 전자산업 분야 등을 포함하면 약 1조5000억원에 달한다.
저마찰 코팅기술은 하나의 코팅층 내에 10나노미터(nm) 미만 크기의 다양한 성분을 결정립·비정질 나노복합구조로 구현할 수 있다. 상용화가 진척되면 다양한 분야에 응용될 수 있다. 한 층으로 이뤄진 소재가 초저마찰·내구성·초고경도, 초발수·광기능, 전도성·내식성 등 상반되는 특성을 낼 수 있기 때문이다. 전자·반도체 소자도 에너지를 절약할 수 있는 저항막 제조 기술 개발이 핵심 과제로 부상했다. 전자제품이나 자동차의 강판, 내외장재, 휴대폰 케이스 등 다양한 제품의 표면처리에 응용할 수 있는 기술도 필요하다.
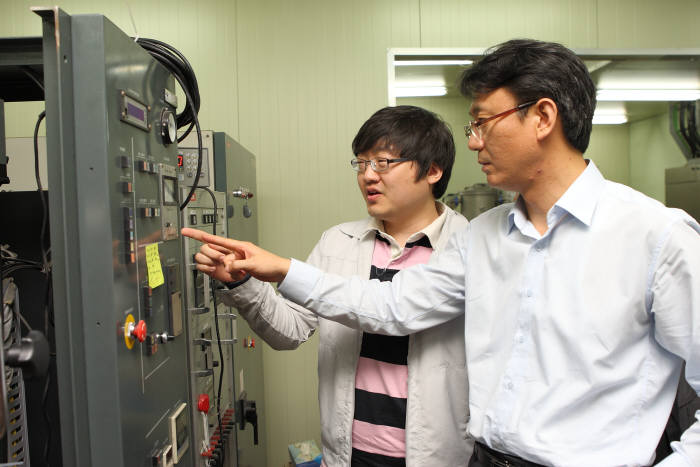
오은지기자 onz@etnews.com