“첨단 신소재인 에코 마그네슘 상용화는 성공을 장담할 수 없었습니다. 연구 초기에 생산기술연구원 내부에서도 거의 무시 수준에 가까울 정도로 에코 마그네슘 연구개발은 관심 밖 대상이었습니다. 하지만 실패를 해도 도전해볼 만한 R&D 과제였다고 생각했습니다.”
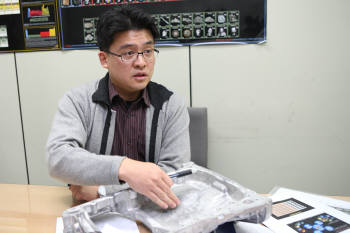
지난달 지식경제부와 미 보잉 간 소재부품 글로벌 동반성장 양해각서(MOU) 교환해 소재부품산업계를 깜짝 놀라게 하는 데 수훈갑을 세운 김세광 생산기술연구원 주조기술센터 박사는 이러한 소회를 전했다.
김 박사는 에코 마그네슘 개발 실패를 두려워하지 않고 연구개발에 지난 2004년 과감하게 도전한 지 6년 만에 세계 최초로 원천 특허를 확보했다. 덕분에 정부는 미 보잉과 손을 잡게 됐다.
그의 도전은 한마디로 마그네슘 소재가 지닌 단점을 다스리는 기나긴 싸움이었다. 마그네슘 무게는 철에 비해 4배 가벼우면서도 비강도(도 및 비중의 값)는 6배나 높다. 마그네슘의 이러한 특성 때문에 휴대폰·노트북 등 전자 제품부터 자동차까지 폭넓게 사용할 뿐 아니라 수요도 크게 늘어나는 추세다. 하지만 마그네슘엔 치명적인 단점이 있다. 공기 중에서 폭발할 위험이 있고 물에 닿으면 녹슨다. 그래서 합금처리를 해야 하는데 이 과정에서 지구 온난화를 가속화하는 슈퍼온실가스인 육불화황(SF6)과 인체유해가스인 이산화황(SO2)을 사용해야 한다. 이런 이유로 선진 기업들은 가격이 저렴하면서 특성이 우수한 새로운 마그네슘 합금 기술을 아직도 찾고 있다.
김 박사는 마그네슘 합금 과정에서 산화칼슘을 도포해 얇은 막을 형성하는 합금 기술 개발에 성공했다. 공정 과정에서 폭발을 방지하고 인체에 무해하면서 온실가스를 사용하지 않는 에코 마그네슘 합금 기술을 세계 최초로 세상에 내놓았다.
그는 이후 세계마그네슘협회(IMA) 등 해외 학회 세미나에 참석해 샘플을 세계 마그네슘 산업계에 1000여개 무상으로 공급하는 등 산업화 가능성을 타진했다. 이 과정에서 보잉 관계자를 만났다. 드디어 지난 2011년 11월 보잉 주선으로 미 연방항공국(FAA)과 마그네슘소재 항공기 사용 금지를 풀기 위한 테스트 기회를 가졌다고 한다.
에코 마그네슘은 산화칼슘 함량에 따라 발화 저항성을 조절할 수 있는 장점이 있다. 그는 산화칼슘이 0.5%, 1.0%, 1.5% 들어간 세 종류 에코 마그네슘을 테스트했다. 당시 해외 마그네슘 전문기업인 멜(MEL)이 제출한 WE43(저가인 산화칼슘 1.5%, 고가인 이트륨 4%, 희토류 3% 함유)만이 테스트를 통과한 상태였다.
이에 그는 1.5% 산화칼슘 에코 마그네슘의 테스트 통과를 확신했다. 그래도 에코 마그네슘 테스트 결과에 그는 놀랐다. 세 종류가 모두 통과한 것은 물론이고 WE43보다 우수한 발화 저항성을 보였다. 우리나라가 세계 최대 항공사인 보잉에 소재 부품을 처음으로 직접 공급하는 것이 결정되는 순간이었다.
김 박사는 “좋은 쌀(소재)도 중요하지만 밥 짓는 기술(뿌리기술)도 똑같이 중요하다”며 “국내 산업계는 신소재를 활용하는 시스템이 미비된 탓에 신소재 산업화가 더디다”며 “외국기업의 신소재 활용 시스템을 벤치마킹할 필요가 있다”고 말했다.
안수민기자 smahn@etnews.com