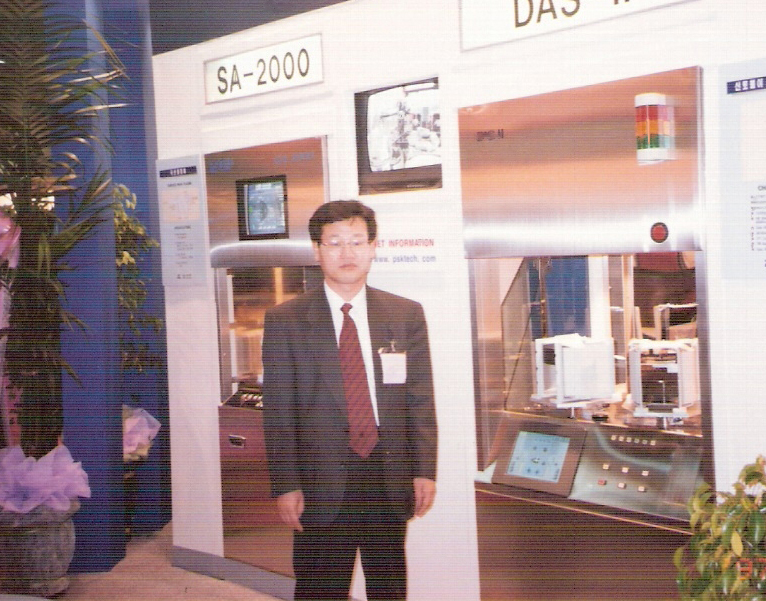
피에스케이는 반도체 전공정 핵심장비 국산화에 성공한 국내 최초의 업체라고 할 수 있다. 기술전수를 약속한 일본 업체가 뜸만 들이자 모든 것을 독자적으로 개발해야 하는 역경은 ‘해내고 말리라’는 강한 도전의식을 고취시켰고, 1996년 독자적 애셔장비 개발에 성공했다.
당시 일본에서 애셔 등을 전문으로 생산하던 PSC와 합작으로 설립되었던 피에스케이는 서로가 내면적으로 추구하는 목표가 달랐던 것 같다. PSC는 피에스케이를 성장세에 있던 국내 반도체 소자업체의 시장을 확보하기 위한 교두보로 활용할 목적이었지 기술을 전수할 생각은 전혀 없었다. 이러다가는 피에스케이가 독립적인 전공정 장비 공급업체가 아닌 PSC에 의해 예속당할 수밖에 없다는 생각에 일본업체 모르게 피에스케이 내부에 TF를 구성해 직접 장비를 개발하기로 결단하고 국산화 개발에 나섰다.
하지만 이 업체는 우리직원들에게 기술 전수는커녕 장비근처에도 가지 못하게 했다. 게다가 공급가격까지 높여 우리 업체가 개발비 확보를 못하도록 했다. 이는 오히려 우리의 위기의식을 키웠고 독자기술 개발 의지를 불타오르게 했다.
이때 누구보다 가장 고생했던 사람들이 다름아닌 우리 기술자들임을 말해 무엇할까. 낮에는 일본업체의 무시 속에서도 한번이라도 더 배우려고 기를 썼고, 저녁이면 지친 몸을 추스리고 설계도 작업을 진전시키기 위해 밤을 새우기 일쑤였다. 국내에서도 포항공대와 인하대 등 대학과 산·학협력을 맺어 연구개발에 힘을 실었다. 이런 노력이 있었기 때문에 지금의 피에스케이가 있다는 것에 감사하고 또 감사할 뿐이다.
이어 95년 PSK 연구소를 설립, 양재균 연구소장(현 부사장)을 영입해 기술 독립에 박차를 가했다. 첫째로 배치타입(batch type)에서 싱글타입(single type)으로의 전환에 나섰다. 배치타입이란 웨이퍼 50∼100장 정도를 한꺼번에 처리하는 방식이고, 싱글타입이란 웨이퍼를 한 장씩 처리하는 방식이다. 고객들도 섬세한 공정을 갖춘 싱글타입을 선호했다.
우리의 일본협력업체조차 개발에 실패하자 우리 내부에서도 회의론이 나왔다. 하지만 고객이 원하는 것이 무엇인지 알면서도 기술력이 안 된다는 이유로, 무엇보다 도전해보지도 않고 포기한다는 것은 있을 수 없는 일이라고 생각했다. 또 선발 업체가 못 이룬 것을 성공해야만 진정한 기술 독립을 이룰 수 있다는 판단에 무모하지만 과감히 기술개발에 들어갔다.
두번째는 로드로크(Load-Lock) 혁명이다. 기존 장비와 달리 진공인 상태에서 웨이퍼를 운송하는 이 로드로크 부분을 아예 없애버리고 대기압에서 웨이퍼를 운송하도록 했다. 후발업체에게 선발기업의 방식을 버린 이 방식은 혁명과도 같은 일이었다. 똑같아서는 매번 2등밖에 될 수 없다는 것이 나의 지론이었다.
결국 96년 우리 독자기술로 200㎜ 애셔장비-DASⅡ를 개발하게 됐다. 그뿐만이 아니었다. 우리의 제품차별화 전략이 인정을 받고 국내 최고의 반도체 소자업체로부터 첫 수주로 20대를 주문 받은 것이다. 이때의 기쁨을 어떻게 말로 표현할 수 있을까! 이로써 우리는 완전한 애셔장비 독립! 기술 독립을 일궈낼 수 있었다.
kspark@psk-inc.com
제목 : 반도체 전공정 핵심 장비- 애셔 독립 만세!
사진 - 1997년 세미콘 코리아에 전시된 ‘200㎜ 애싱시스템즈 DAS’와 개발 주역인 양재균 부사장.