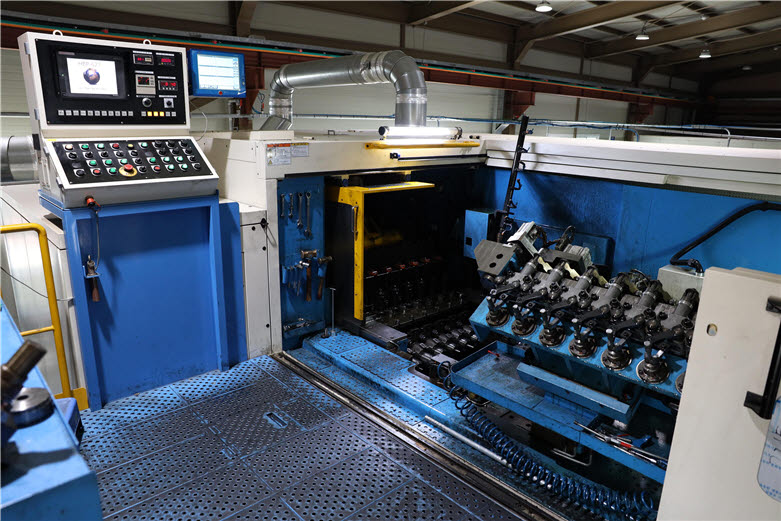
한국생산기술연구원(원장 이낙규)은 국내 최초로 금형 한계 수명의 정량적 예측과 품질 검사 자동화 시스템을 개발했다고 18일 밝혔다.
서영호 한국생산기술연구원 스마트모빌리티소재부품연구그룹 연구원팀이 작업자가 쉽게 금형 파손 시점을 감지할 수 있도록 수명을 시각화하는 모니터링 시스템을 구현했다.
반복적으로 높은 힘을 가하는 '냉간단조' 금형 공정에 활용 가능하다. 한계 수명이 예측 가능해지면 금형 파손 전 최대한 사용하고 교체하기 때문에 공정 비용을 절약할 수 있고 불량 발생도 줄일 수 있다.
기존 방식은 이상적인 공정 상황 하중치를 활용해 수명을 예측하는 방식이다. 환경변수를 고려하지 못하고, 공정 중 편차도 예측 불가능했다.
개발 모니터링 시스템은 금형에 '피에조 센서(압력이 가해졌을 때 전압이 발생하는 전기 회로)'를 설치, 전기신호를 실시간 변환해 그래프로 표현하게 했다. 환경변수와 편차 모두 반영할 수 있다.
이 결과로 압력이 반복적으로 가해질 때 금형이 단위 면적 당 받는 하중을 분석해 파손 예상 부분을 찾아낸다.
해당 시스템은 현재 자동차 부품 전문 제조업체인 이화테크원에 구축돼 자동차 조향장치에 사용되는 '볼스터드' 부품 생산에 활용되고 있다.
연구팀은 생산 제품 품질 검사를 자동화하기 위해 비전센서를 시스템에 적용할 수 있는 알고리즘도 개발했다. 검사 대상의 형태, 크기, 문자, 패턴 등을 판별해 불량품을 찾아낸다.
서영호 연구원은 “제조산업 지능화를 위한 첫걸음으로 현재 실제 현장에 적용 가능한 단일 공정 기술이 개발 완료된 상태”라며 “대규모 제조업체들과 공정 간 연계와 모듈화 작업을 추진해 글로벌 대응에 힘을 합칠 예정”이라고 밝혔다.
한편, 이번 성과는 생기원 제조혁신지원사업(2020년~2022년 예정)을 통해 수행된 '키-테크' 성과 중 하나다. 올해 2차년도 연구가 진행 중이며 현재 관련 특허 1건이 출원된 상태다.
이번 기술 개발은 산업부의 '글로벌품질대응뿌리기술개발사업'과도 연계돼 있으며, 자동차 부품 전문 제조업체인 이화테크원, 태양금속공업, 프라이맥스와 한국재료연구원이 공동 참여 중이다.
대전=김영준기자 kyj85@etnews.com