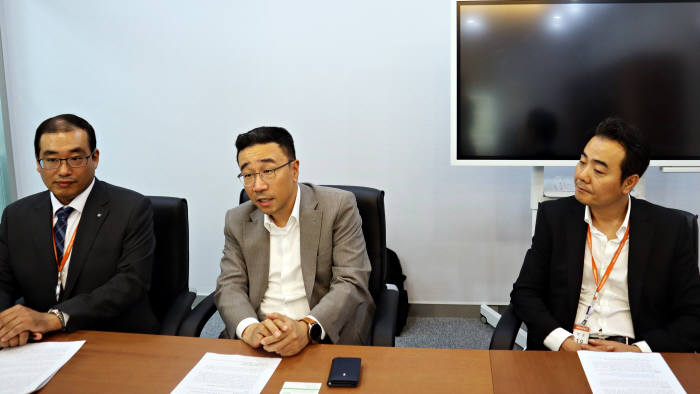
전자·자동차 부품업체 드림텍이 기존 4개 생산공장을 한 개 스마트공장으로 통합하는 데 성공했다. 드림텍과 유니퀘스트(그룹사), 슈나이더일렉트릭으로 구성된 '원팀(One Team)'이 일궈낸 성과다. 드림텍 통합형 스마트공장 프로젝트는 '에너지 효율 극대화' 차원에서 나아가 안전사고 예방·생산성 제고·제조업 경쟁력 강화 측면에서도 긍정 효과가 기대된다.
김형민 드림텍 대표는 17일 본지 기자와 만나 “4개 공장을 하나로 통합한 드림텍 아산 신(新)공장을 4차 산업혁명 시대에 부응하는 '초일류 스마트공장'으로 육성하겠다”고 말했다.
드림텍은 삼성전자·현대차 등에 핵심 부품을 공급하는 제조사로 해외에는 베트남·중국·인도(예정) 등에 거점을 두고 있다. 천안 1공장은 인쇄회로기판모듈(PBA) 등 모바일 부품을 천안 2·3공장은 자동차 부품을 생산했다. 군포 공장에서는 스마트폰 지문인식센서 모듈을 납품했다. 그러나 지난해 말부터 아산 공장에서 4개 공장 전(全) 제품을 생산·관리하고 있다.
원팀은 △다양한 제품이 생산 가능하도록 제조공정을 변경 △안정적 생산이 가능한 환경으로 전환 및 유지 △에너지비용·관리비용 절감 등에 중점을 두고 '통합형 스마트공장' 구축을 추진했다.
슈나이더일렉트릭 에너지관리통합 플랫폼 '에코스트럭처'를 핵심 기반으로 △냉·난방 △공조 △열원 △환기 △전력 △조명 △급수 등 각종설비를 통신과 연결해 원격으로 관리·제어하는 데 성공했다. 수집된 데이터를 실시간 분석, 최적화된 피드백을 제공하는 특화 솔루션도 적용했다.
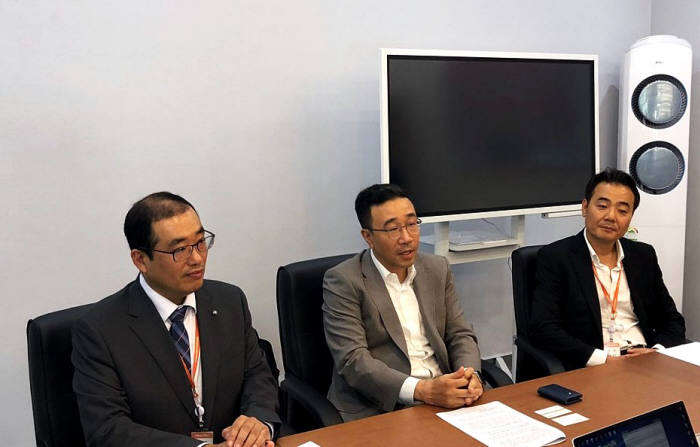
김경록 슈나이더일렉트릭코리아 대표는 “스마트공장은 각각의 기기 및 설비를 연결한 후 최적 알고리즘으로 데이터를 주고받는 업무가 핵심이기 때문에 '확장성'과 '개방성'이 무엇보다 중요하다”며 “아산 공장은 기존 4개 공장에서 사용하던 설비·생산 프로세스를 하나로 통합, 에코스트럭처를 통해 안정적으로 관리·운영되고 있다”고 설명했다.
김형민 드림텍 대표는 “공장 전력값을 확인하는 방법에는 순시값(사용중인 전력값)과 적산값(누적된 전력값)이 있다”며 “아산 공장은 전체 전력이 어떻게 사용되고 있는지 한눈에 파악할 수 있고 이를 통해 중장기 에너지효율 전략을 수립하는 게 가능했다”고 말했다. 에너지효율 이외에 부품 수율(생산율)을 99.8%까지 끌어올리는 효과도 분명했다고 덧붙였다.
그는 '스마트공장은 디자인하는 것'이라고 피력했다. 제조사가 에너지효율·제품생산성·품질관리 등 관점에서 어떤 솔루션을 접목할 것인가를 고민하고 이후 확장성·개방성·호환성을 고루 갖춘 파트너와 호흡을 맞추는 과정이 중요하다는 설명이다.
김형민 대표는 “아산공장 설비·리소스에 대한 글로벌 고객사 만족도가 상당하다”며 “파트너 요구를 반영한 결과물은 해외에서 사업 신뢰도를 높여주는 하나의 지표가 됐다”고 소개했다.
스마트공장과 일자리 창출은 '상극'이 아닌 '상생'이라는 점도 거듭 강조했다. 그는 “일각에서는 스마트공장이 일자리를 감소시킬 거란 우려가 있는데, 기존과는 다른 양질 일자리가 창출된다는 점을 고려해야 한다”며 “(스마트공장에 대한) 인식변화는 제조업의 새로운 트렌드가 될 것”이라고 내다봤다.
드림텍 그룹사인 유니퀘스트의 윤배열 이사는 “스마트공장은 해외로 이전했던 공장을 자국으로 불러들이는 '리쇼어링 현상'도 기대할 수 있다”며 “미국·일본 등 선진국에서는 이미 세제감면·공장 설립비 지원 등 혜택을 제공해 해외로 나간 생산공장을 자국으로 불러들이는 추세”라고 전했다.
그는 우리나라도 정부 차원에서 '스마트공장 육성-기업 지원책 마련-일자리 창출'로 이어지는 선순환 생태계 조성 방안을 모색해야 할 때라고 조언했다.
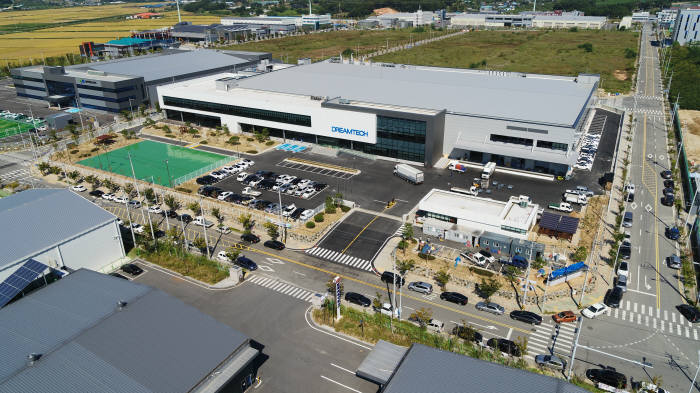
최재필기자 jpchoi@etnews.com