현대위아가 공작기계와 3D프린터를 결합한 차세대 금속 가공기를 국내 최초로 개발했다.
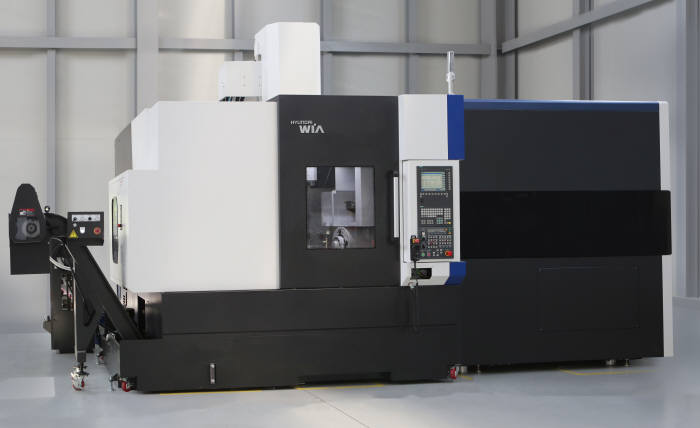
현대위아(대표 김경배)는 금속 3D프린터 전문업체 인스텍과 함께 '3D프린팅 하이브리드 가공기'를 개발했다고 11일 밝혔다.
하이브리드 가공기는 금속 분말을 쌓아 원하는 물체를 만드는 3D프린터와 금속을 공구로 깎아 가공하는 공작기계를 결합한 제품이다. 공작기계가 가진 높은 정밀도와 3D프린터의 편리함을 더한 것이 강점이다.
현대위아와 인스텍은 산업통상자원부 '글로벌 전문기술개발사업' 일환으로 2015년 개발을 시작해 4년 만에 결실을 맺었다. 양사는 오는 2020년부터 하이브리드 가공기를 상용화해 인공 고관절 제조 시장에 뛰어든다는 계획이다.
현대위아는 하이브리드 가공기를 5축 머시닝센터와 두 가지 3D프린터 모듈을 합치는 방식으로 개발했다. 5축 머시닝센터 공작기계에 '고에너지형(DED·Directed Energy Deposition)' 3D프린터 모듈과 '분말적층용융(PBF·Powder Bed Fusion)' 모듈을 붙인 것이다. 제품 특성에 따라 DED나 PBF 모듈에서 1차적으로 형상을 만든 뒤 공작기계로 정밀하게 깎아 최종 가공물을 완성하는 방식이다.
현대위아는 하이브리드 가공기의 '통합제어기'를 통해 공작기계의 주축과 3D프린터 모듈을 동시에 운용할 수 있도록 했다. 제어기가 최종 결과물을 위한 최적의 가공 공구와 방식을 판단한다. 금속 절삭이 필요하면 머시닝센터에 달린 주축이 내려와 금속을 깎고, 적층 가공이 필요할 때는 DED모듈을 이용한다. DED는 레이저 빔을 이용해 원 소재를 녹여 부착하며 모양을 만드는 3D프린팅 방식이다.
현대위아는 3D프린팅의 또 다른 방식인 PBF 모듈도 함께 사용할 수 있도록 했다. PBF 방식은 금속 분말을 베드 위에 깔고 그 위에 레이저 빔을 주사해 금속을 결합시키며 제품을 만드는 방식으로, 복잡한 형상을 만들 때 유리하다. 현대위아는 공작기계와 PBF모듈을 '자동 워크 교환 시스템'을 이용해 연결해 동시에 쓸 수 있도록 했다. PBF모듈에서 1차적으로 제작한 뒤 자동 워크 교환 시스템을 이용해 이를 공작기계로 옮겨, 최종 완성을 하는 식이다.
현대위아와 인스텍은 하이브리드 가공기를 '인공 고관절' 제작에 우선적으로 투입할 예정이다. 티타늄 소재로 만드는 인공 고관절은 3D프린터와 공작기계를 함께 이용해 만드는 대표적 금속 제품이다. 인공 고관절의 연결부위에 해당하는 '컵(CUP)'은 PBF모듈을 이용해 1차 적층 후 공작기계로 최종 가공을 해 만들고, 다리로 이어지는 뼈 부분인 '스템(STEM)' 부위는 DED모듈로 제작한 후 공작기계로 마무리해 만든다.
현대위아 관계자는 “현대위아 공작기계의 정밀 가공 기술을 기반으로 높은 완성도의 하이브리드 가공기를 선보일 수 있게 됐다”며 “인스텍과 함께 글로벌 3D프린터 시장의 새로운 지각 변동을 일으킬 수 있도록 더욱 노력하겠다”고 말했다.
류종은 자동차/항공 전문기자 rje312@etnews.com