국내 연구진이 산업용 부품 표면의 마찰 저항을 줄이거나 광 효율을 높이는 등 다양한 특성을 부여할 수 있는 기술을 개발했다. 또 이 같은 특성 부여에 필요한 여러 가지 가공 공정을 하나의 장비에서 처리할 수 있는 시스템 기술도 개발, 민간 기업에 이전했다.
한국기계연구원(원장 박천홍)은 박종권 초정밀시스템연구실 박사팀이 각종 부품 표면에 '스마트 서피스 텍스처링'(SST)을 구현할 수 있는 융·복합 가공 기술과 시스템을 개발, 일부 기술을 민간에 이전해 상용화했다고 18일 밝혔다.
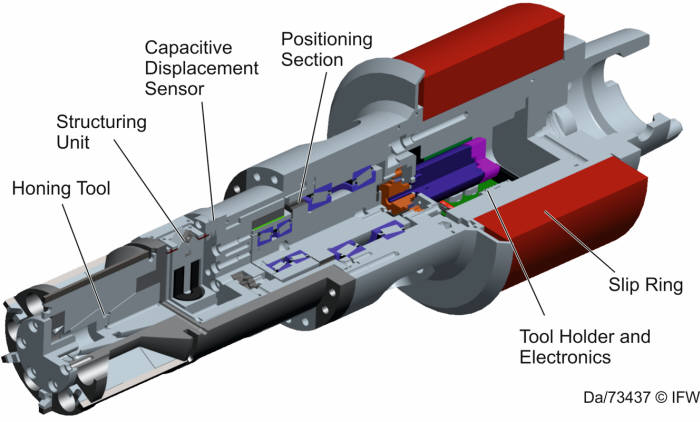
SST는 표면에 미세한 홈이나 돌기를 만들어서 마찰 저항을 낮추거나 높은 광 효율 특성을 부여할 수 있는 기술이다. 초발수 및 항바이러스 특성을 부여하는 것도 가능하다.
주로 자연에서 접할 수 있는 표면 형태를 모사한다. 상어 비늘의 미세돌기를 모사해 유체 저항을 낮춘 '샤크렛 패턴'이 대표 사례다.
에코·바이오 분야를 비롯해 다양한 산업용 부품의 부가 가치를 높이는데 활용할 수 있을 것으로 기대된다.
그동안에는 밀링, 터닝, 그라인딩, 초음파, 레이저 등 다양한 가공 공정을 따로 따로 진행해야 해서 가공 공정이 길고 비용도 많이 들었다.
연구팀은 이 문제를 해소하기 위해 각 공정을 모듈화하고, 필요한 공정을 합쳐 하나의 장비에서 구현할 수 있도록 시스템화 기술도 개발했다. 초음파 진동으로 나노미터(㎚) 크기의 미세 가공도 가능하다.
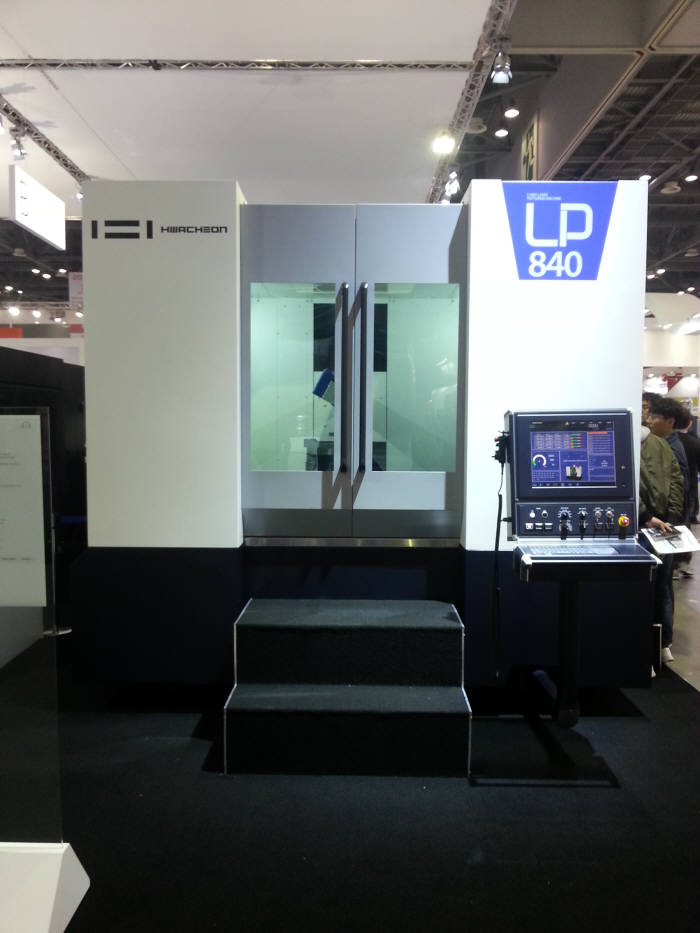
이 가운데 절삭, 연마, 열처리 공정을 하나로 융합한 '5축 머시닝센터 기반 복합 가공 시스템'은 화천기공에 이전했다. 화천기공은 이 기술을 사업화로 연결, 최근까지 70억원에 이르는 매출을 창출했다.
최근에는 테크맥에 '광 기반 복합가공 시스템', 스맥에 '초정밀 터닝 가공시스템', 한국공작기계에 대형 부품 복합가공시스템을 각각 기술 이전했다. 현대자동차와는 엔진 실린더 마찰을 저감시켜서 연료 효율을 높이는 연구를 진행하고 있다.
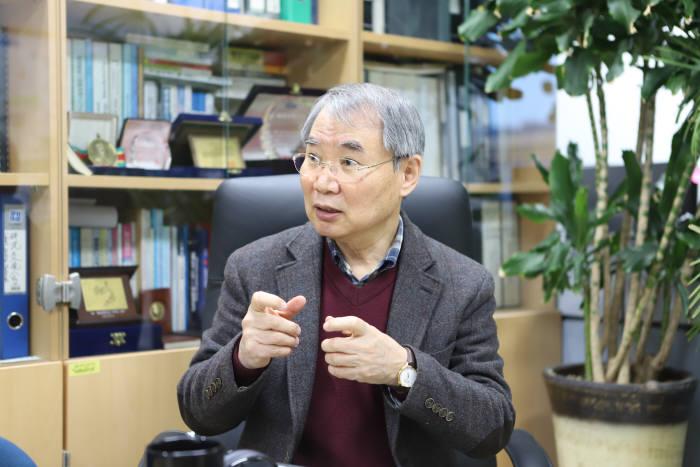
박종권 박사는 “에코·바이오산업 분야 신성장 동력을 마련하고 생산시스템 효율 제고에 크게 기여할 수 있는 성과”라면서 “그동안 개발해 온 기술로 지난해 '국가 연구개발(R&D) 우수 성과 100선'에 이름을 올리기도 했다”고 말했다.
대전=김영준기자 kyj85@etnews.com