3D프린터는 가격이 떨어지고, 가용 소재도 다양해지면서 ‘3차 산업혁명’을 주도할 도구로 주목받고 있다. 자동차 부품 업계도 시제품 제조 공정 단순화와 비용 감소 효과에 주목해 도입에 적극적이다.
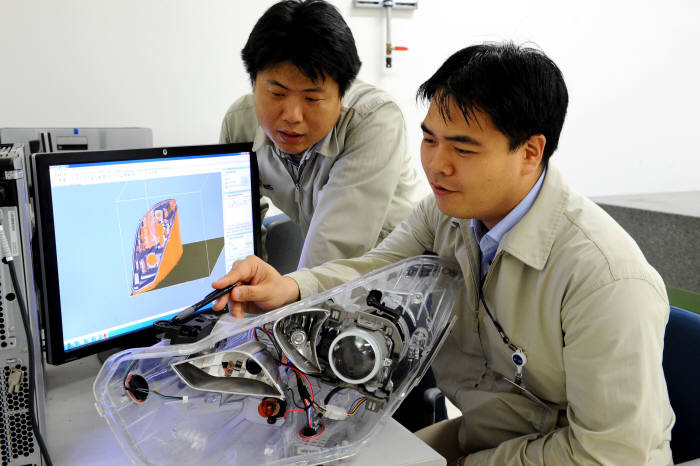
현대모비스는 지난 2002년부터 제품 연구개발 과정에서 3D프린터를 활용해왔다. 경기도 용인시 현대모비스 연구소 전장연구동에 FDM(Fused Deposition Modeling) 방식 3D프린터 2대, SLA(Stereo Lithography Apparatus) 방식 3D프린터 1대를 갖췄다.
FDM 3D프린터는 고체 수지 재료를 녹여 적층 구조를 만드는 장비로, 다양한 색깔을 낼 수 있고 비용이 싸지만 조형 속도가 느리다. 액체 소재를 사용하는 SLA 3D프린터는 정밀한 모형을 제작할 수 있고 조형 속도도 빠르지만, 자체 변형이 진행될 수 있어 후처리 공정이 필요하다.
현대모비스 시작개발팀은 개발하는 제품 종류에 따라 적절한 3D프린터를 택해 시제품을 제작한다. 현업 연구팀이 3D CAD 데이터를 시작개발팀으로 보내면, 3D프린팅 가능 여부를 검토해 제작에 들어간다. 지난해 제작 건수는 3159건으로 2011년 2119건보다 49% 증가했다.
시작개발팀 관계자는 “소프트웨어 개발을 제외한 거의 전 부문에서 3D프린팅 시제품을 의뢰한다”며 “제작이 불가능한 일부를 제외하면 거의 전 부문에서 활용하고 있기 때문에 연간 가동률이 평균 100%”라고 밝혔다.
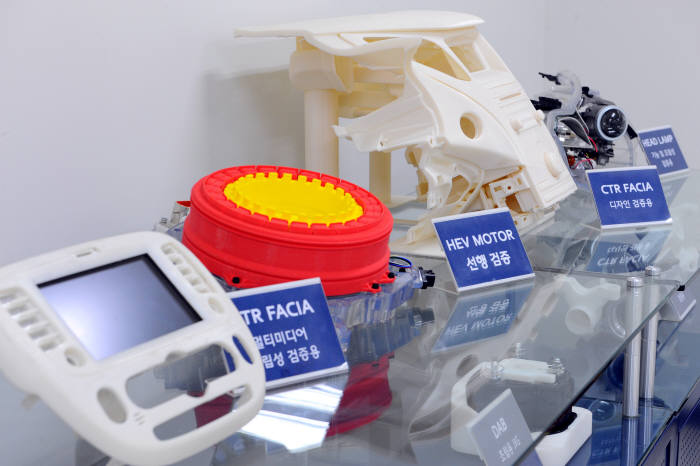
3D프린터 활용의 가장 큰 장점은 비용과 시간 절감이다. 디자인·설계를 변경할 때마다 별도 금형을 제작할 필요가 없기 때문이다. 대시보드는 2주, 램프는 1주, 에어백은 3일이면 모형을 제작할 수 있다. 헤드램프 모형은 목업 모형보다 30분의1 가량 줄어든다.
이런 장점은 설계 검증 고도화로 이어진다. 시제품 제작 기간이 짧고 비용이 낮아지면서 기존에 생략했던 부분도 검증할 여유가 생겼기 때문이다. 특히 작동 구현이나 디자인, 간섭 정도를 재확인할 때 활용도가 크다. 1m 이상 대형 모형 변형률은 1% 미만, 소형 모형은 오차가 0.089㎜ 미만이기 때문에 정밀성도 보장된다.
크기와 소재의 제한은 풀어야 할 과제다. 현재 3D프린터로 제작할 수 있는 모형의 최대 크기는 1m 남짓이다. 또 플라스틱 위주의 강도가 낮은 소재만 사용할 수 있어 작동성 검증에 한계가 있다. 기어박스 모형을 실제 구동하면 하중을 견디지 못해, 단순 작동 검사만 가능한 실정이다.
현대모비스는 개선된 소재와 이를 적용한 3D프린터가 시판 중인 만큼, 이런 한계를 극복할 수 있는 신규 장비 도입을 검토 중이다.
송준영기자 songjy@etnews.com