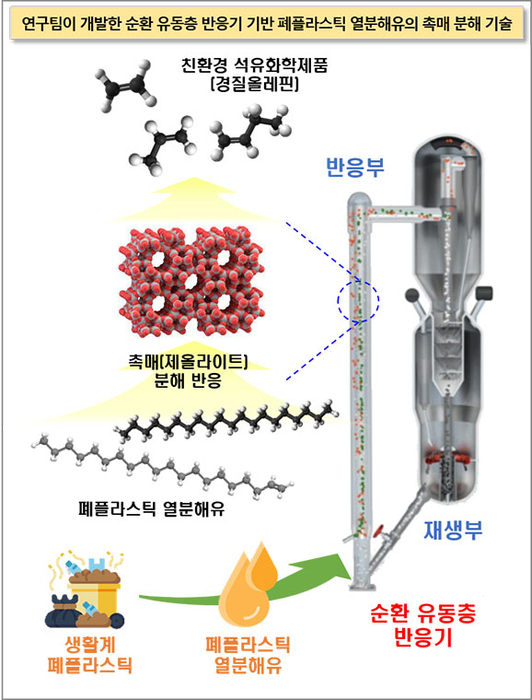
폐플라스틱을 고열 분해해 얻는 '폐플라스틱 열분해유'가 귀한 자원으로 떠오르는 가운데, 국내 연구진이 효율적으로 석유화학 제품을 생산하는 기술을 개발했다.
한국화학연구원(원장 이영국)은 김도경·박용기 박사팀이 폐플라스틱 열분해유로 플라스틱 원료인 '경질 올레핀'을 친환경·경제적으로 생산하는 촉매·반응기를 발표했다고 9일 밝혔다.
폐플라스틱 열분해유는 나프타 분해 공정(NCC) 원료(나프타) 대신 쓰여, 경질 올레핀을 만들 수 있다. 다만 나프타와 폐플라스틱 열분해유 간 물성 차이로 상업화에 한계가 있었다.
나프타는 탄소 수가 5~9개인 반면 열분해유는 5~44개로, 나프타 성분이 약 20%에 불과하다. 또 열분해유에는 나프타 분해 공정 원료로 부적합한 올레핀과 다양한 불순물이 포함돼 있다. 이를 제거하려면 고온·고압 수소화 공정이 추가로 필요하다. 게다가 기존 공정은 850도 이상 고온이 필요하다.
연구팀은 2017년 상업화에 성공한 순환 유동층 반응기 기반 나프타 촉매 분해 기술을 발전시켜 기존 기술 한계를 극복했다.
폐플라스틱 열분해유를 추가 수소화 과정 없이 사용하더라도 기존 나프타 대비 더욱 높은 경질 올레핀 수율을 얻을 수 있었다.
한편 촉매 분해 반응에서는 촉매 표면에 찌꺼기가 많이 쌓여 성능이 저하되는 문제가 있는데, 성능을 유지하려면 촉매 재생이 필수다. 연구팀이 개발한 순환 유동층 반응기는 반응 부위에서 촉매(제올라이트 성형체)와 원료가 함께 움직이며 반응하고, 재생 부위에서는 비활성화된 촉매가 연속 재생되는 구조여서 이런 문제를 해결할 수 있었다.
연구팀의 파일럿 규모 촉매·반응기로 기존 나프타 분해 공정보다 170도 낮은 680도에서 폐플라스틱 열분해유를 투입한 결과, 경질 올레핀 수율이 나프타를 사용할 때(34.6%) 보다 27% 향상(44.1%)됐다. 또 폐플라스틱 열분해유를 시간당 1㎏씩 24시간 연속 투입해도 성능이 유지됐다.
연구팀은 실용화를 목표로 후속 연구를 진행해 2030년 실증 가능성을 검토할 계획이다.
이영국 원장은 “이 기술이 국가 석유화학산업 경쟁력 강화 및 탄소중립 구현에 기여할 것으로 생각한다”고 말했다.
이번 연구 논문은 'ACS 서스테이너블 케미스트리 앤드 엔지니어링' 8월 표지 논문으로 게재됐다.
이번 연구는 한국화학연구원 기본사업, 과학기술정보통신부 한국연구재단 석유대체 친환경 화학기술개발사업 및 국가과학기술연구회(NST) 융합연구단 사업 지원을 받아 수행됐다.
김영준 기자 kyj85@etnews.com