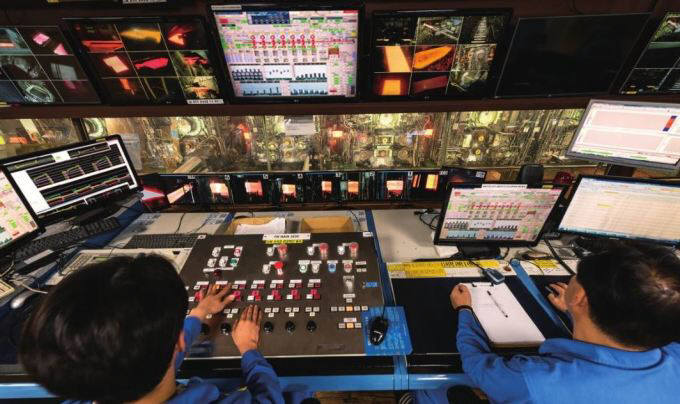
최근 제조 기업들이 잇달아 디지털 전환에 착수했다. 산업 현장 효율성과 생산성 뿐 아니라 작업자 안전도까지 높일 수 있어서다.
포스코가 대표적이다. 이 회사는 포항과 광양 두 제철소에 인공지능(AI)를 결합, 현장을 스마트화했다. 지난 7월 세계경제포럼(WEF)이 선정하는 '세계 등대공장'에 국내 최초로 선정될 만큼, 성과를 인정받았다.
포스코가 도입한 스마트 공장은 자체 플랫폼인 포스프레임을 통해 전 공장의 데이터를 수집, 정형화한다. 또 사물인터넷, 빅데이터, AI 등 신기술을 활용, 데이터를 자가 학습하고 최적 공정 조건을 계산해 이를 제어한다.
예를 들어 제철소 내 생산 계획을 담당하는 수주 공정 그룹은 시간을 가장 많이 허비했던 소Lot 주문 여부를 크게 줄였다. 소Lot은 강종별로 제철소에서 요구 최소 주문량에 미달돼 생산상 제약을 받는 주문을 말한다. 기존에는 주문이 들어오면 조건을 파악하고 이를 소Lot 기준과 일일이 비교하는 과정을 거쳤다. 처리 시간은 평균 12시간에 달했다.
하지만 AI가 자동으로 주문별 소Lot 여부를 판단해주면서 소요 시간은 1시간 내외로 크게 줄었다.
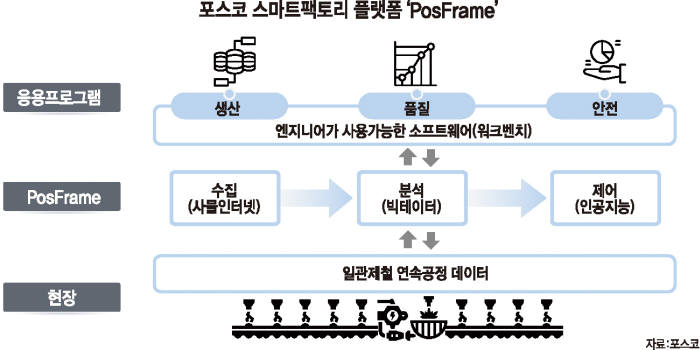
또 스마트 공장은 용광로의 통기성과 연소성, 용선 온도, 출선량 등까지 AI로 제어한다. 용광로 상태를 결정짓는 모든 변수를 정의하는 '데이터 정형화'도 구축했다. 이른 바 '스마트 고로'다. 이를 통해 포항 2고로의 경우 하루 생산 쇳물 양은 240톤 증가했다. 이 기술은 지난 7월 국가 핵심 기술로 지정됐다.
포스코 관계자는 “스마트 제철소 구축은 현재 진행형”이라며 “미래에는 설비 상태를 예지하고 자동 제어해 생산과 품질, 안전을 모두 확보하게 될 것”이라고 말했다.
국내 뿐 아니라 해외에서도 스마트 공장 도입은 활발하다. 에너지 관리·자동화 분야 글로벌 기업인 슈나이더일렉트릭은 인도네시아 바타민도 산업 단지에 위치한 바탐 공장을 스마트화했다.
이 공장은 에코스트럭처 머신을 구축해 공장 운영 성과를 실시간 확인하고 기계 성능과 유지보수 시기를 미리 예측할 수 있다. 관리자는 제조 현장 시스템 문제를 실시간 대응 가능하다. 이를 통해 유지보수 작업 시간과 낭비되는 자재를 각각 17%, 46% 절감했다. 반면 에너지 효율은 최대 5~7%까지 높아졌다. 전자기계와 센서 장비 등 생산성은 향상됐다.
슈나이더일렉트릭은 오는 2020년까지 전세계 보유 공장 200여곳 가운데 100곳을 스마트화한다는 계획이다.
업계 관계자는 “4차 산업혁명을 달성하기 위해선 스마트 공장 도입은 필수적”이라며 “전 공정에서 운영과 에너지 효율성을 크게 높일 수 있기 때문에 디지털 전환에 뒤처지지 않는게 중요하다”고 말했다.
류태웅기자 bigheroryu@etnews.com