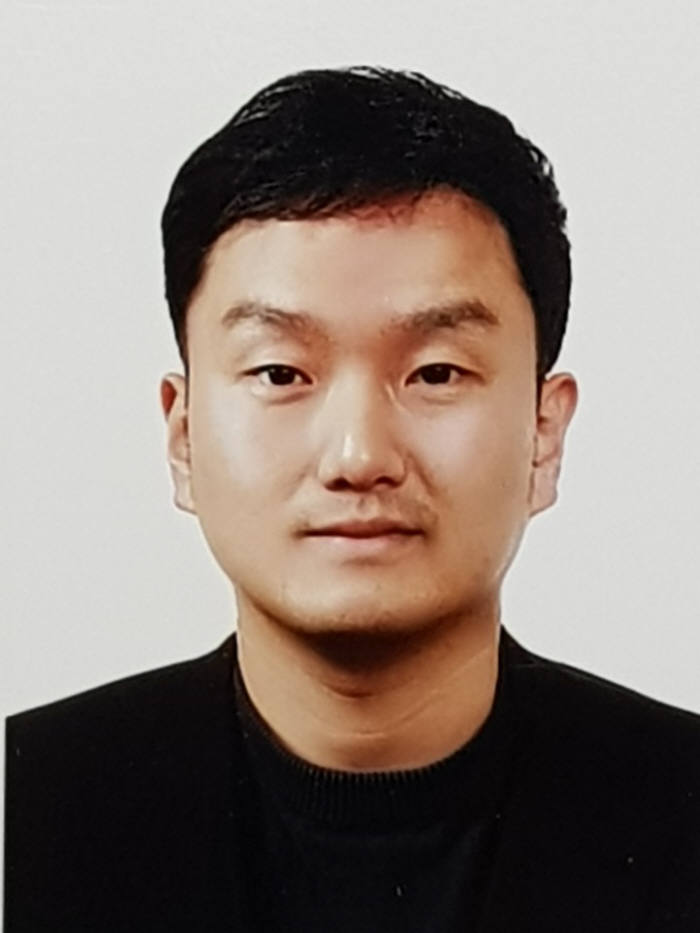
컴퓨터 연산 처리 능력이 낮던 지난날 컴퓨터 역할은 실험 데이터 수집 및 정리에 국한됐다. 그러나 컴퓨터 기능이 급격히 향상되면서 사용 범위는 점차 넓어졌다. 이제 간단한 문제는 PC를 활용하고 복잡한 문제는 워크스테이션 슈퍼컴퓨터로 계산한다. 그보다 복잡한 문제는 원격으로 접속된 클러스터 슈퍼컴퓨터를 통해 처리한다. 이뿐만 아니라 멀티코어 프로세서 개발, 병렬화 기술 개발, 클러스터링 기술 개발, 더 빠른 행렬처리 알고리즘 개발이 이뤄지면서 컴퓨터는 이제 단순한 데이터 정리뿐만 아니라 '시뮬레이션'까지 가능하다.
컴퓨터 시뮬레이션 기술은 발전을 거듭하고 있다. 재료 시뮬레이션을 예로 들어 보면 1960년대에 수백개 원자 대상으로 시작한 컴퓨터 시뮬레이션은 이제 분자동역학(MDS) 방법으로 수백억개 원자, 제1원리 분자동역학 방법으로 수천개 원자를 각각 다룬다.
MDS 시뮬레이션은 원자운동 모의실험을 통해 원자와 분자의 동태 구조 또는 물성을 연구하는 기법이다. 계산 규모가 크다는 게 장점이지만 정밀도가 낮다는 게 한계다.
반면에 양자역학을 기반으로 하는 제1원리 MDS는 정밀도를 높일 수 있지만 계산 시간이 많이 소요된다. 규모가 큰 시스템 묘사에 적합하지 않다는 단점이 있다. 정확도를 높이면서도 시간을 절감하기 위해 제안된 개념은 이들 두 개념이 혼합된 '멀티스케일 시뮬레이션'이다. 이를 활용하면 눈에 보이지 않는 원자 단위가 실제로 우리가 이용하는 자동차나 항공기 사이즈로 확장되면서 현상에 대한 이해가 가능하다.
최근 이러한 시뮬레이션 기법을 활용한 재료 분야 전산과학이 첨단과학 분야 하나로 빠르게 자리매김한 것은 결코 우연이 아니다. 선진국이 차지하고 있는 항공우주, 자동차, 국방 등 복합재료를 기반으로 한 고부가 가치 산업을 예로 들어보자. 실제 값비싼 부품 하나하나가 수개월에서 수십년 수명을 견디도록 개발되기까지는 복합재료에 사용되는 각 재료의 잠재적 해석, 형상에 맞는 모델링, 다양한 성형공법의 최적 공정해석, 최종 제품 평가와 수명 예측까지 시뮬레이션 기법이 필수 항목으로 활용되고 있다. 시뮬레이션 기법을 사용해 테스트 시간을 줄이고 비용과 노동력 절감을 통한 생산성 확대로 우수한 제품을 더욱 효율화해서 만드는 것이 가능해졌기 때문에 재료 분야에서 전산과학 발달은 필수였다.
항공기 개발 과정에서 다양한 복합소재를 개발하기 위해서는 설계 단계에서 신뢰성을 높이기 위해 많은 테스트를 거쳐야 하기 때문에 많은 비용 및 개발 시간이 필요하다. 그런데 컴퓨터 시뮬레이션을 통할 경우 이러한 시간과 비용을 절약할 수 있었다.
국내로 눈을 돌려 보자. 국내 재료 관련 시뮬레이션 기법은 아직 직접 산업에서 쓰이기는 어려운 실정이다. 항공용 설계 기술은 존재하지만 현재 복합재료 구조 개발의 핵심 기술은 온전히 미국이나 유럽 자료에 의존하기 때문에 항공기 제작 등에 직접 쓰일 수는 없는 상황이다. 국내에서도 고성능 복합소재 부품 개발을 위한 실용화 기술 및 기초 연구가 활발히 수행되고 있지만 시뮬레이션 정확성 및 효율성을 높이고 이를 통해 고부가 가치 산업의 빠른 성장을 이뤄 내기 위해서는 아직 많은 노력이 필요하다.
시뮬레이션은 원하는 현상을 가상 시험으로 그 결과를 예측할 수 있는 유효 수단이다. 회당 수천만원에서 수억원이 소요되는 자동차 충돌 시험을 직접 수행하는 것을 최소화하고, 가상 환경에서 대량의 테스트를 수행하는 것이 효율 및 합리 타당하다.
미국, 일본, 독일, 영국 등 선진 제조 강국은 이미 고성능 컴퓨팅 기반 모델링과 시뮬레이션의 산업 활용 확대를 위한 국가 지원 체제를 구축하고 있다. 우리나라 역시 이러한 세계 흐름에 발맞춰 컴퓨터 시뮬레이션 투자와 연구 지원 체계를 구축, 독자 기술 개발을 이뤄 내야 한다. 중소 제조기업의 글로벌 경쟁력을 강화하기 위해 노력해야 할 때다.
유재상 한국과학기술연구원 구조용복합소재연구센터 선임연구원 jamesyu@kist.re.kr