발사체용 엔진 컴포넌트(구성품)를 3D 프린팅으로 만들어 제작비용과 시간을 절약하는 국내 연구가 성과를 내고 있다. 한국항공우주연구원(원장 이상률)이 일부 부품 제작에 성공하고, 성능 시험도 진행 중이다.
항우연은 임병직 미래발사체연구단 책임연구원, 임하영 발사체추진제어팀 책임연구원 등 연구진이 금속 3D 프린팅 기법으로 1톤급 액체메탄(LNG)·액체산소 엔진용 연소기를 제작해 재생냉각 연소시험에 성공했다고 19일 밝혔다.
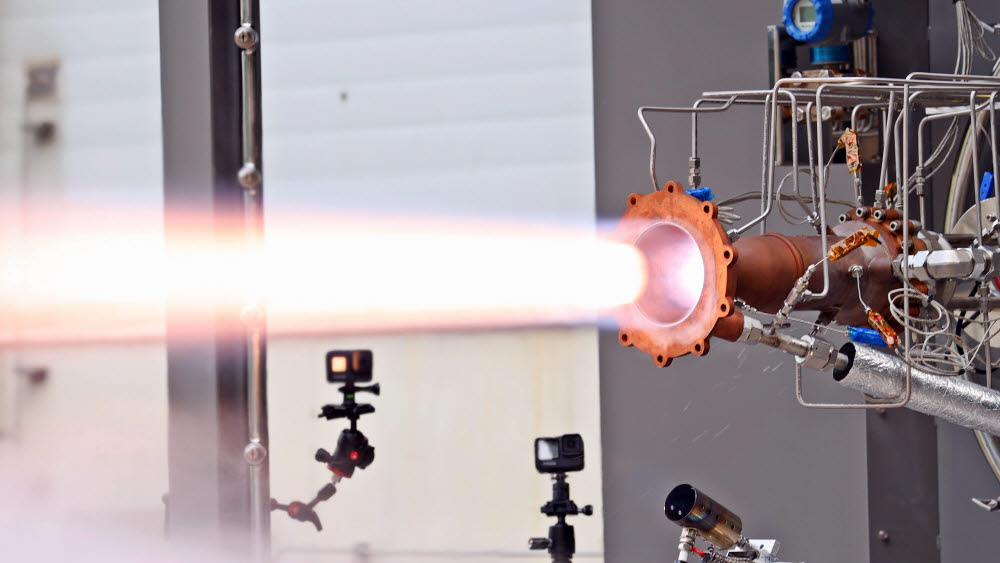
연구진은 '선택적 레이저 용융법(SLM)'을 활용했다. 레이저로 금속 파우더를 부분적으로 녹여 형태를 잡는 기법이다. 이번 시제품에는 구리와 스테인리스강을 활용했는데, 구리를 연소기 적층제작에 활용한 사례는 해외에서도 드문 일이고, 국내서는 처음이다.
시제품 제작은 지난해 말 완료했고 현재 이를 활용한 연소시험이 계속 진행 중이다. 3D 프린팅으로 만든 구성품은 시편 단위 분석 결과 강도 측면에서 기존 기계가공 방식 소재와 큰 차이가 없었다. 오히려 일부 특성은 더 우수한 것으로 나타났다.
3D 프린팅 가장 큰 장점은 짧은 제작기간이다. 기계 가공으로 수개월 제작기간이 소요되던 것을 3D 프린팅을 활용해 3분의 1 수준으로 줄일 수 있었다. 일부 표면 처리, 열처리, 인터페이스(결합면) 가공을 제외한 추가 가공 공정이 불필요하다. 전통적인 제작공정에서는 복잡한 내부 구성품을 개별 제작해 조립·접합하던 방식이었으나 3D 프린팅 제조 공정에서는 이들을 통합해 제작하는 것이 가능하다.
항우연 연구진은 이번 성과를 바탕으로 1톤 엔진에 쓰이는 터보펌프, 밸브 등 다른 요소 제작에도 도전할 계획이다. 3톤 엔진용 연소기 제작도 진행 중이며 고성능 구리합금 사용과 같은 소재 다양화 및 활용 장비 대형화를 통한 형상 단순화 연구도 계획 중이다.
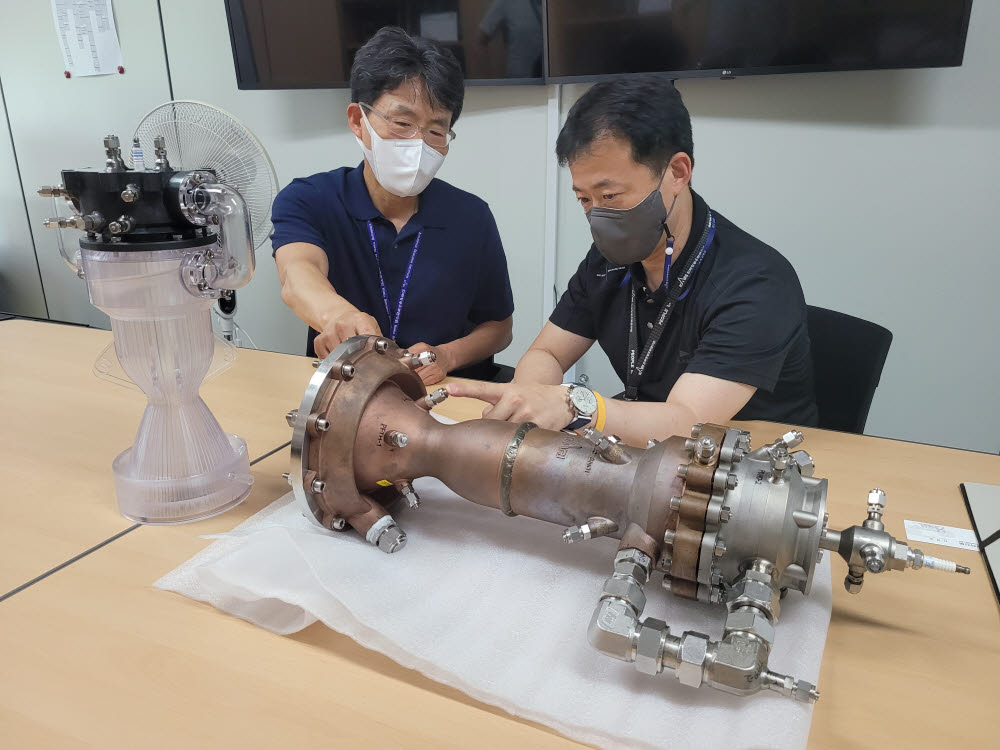
임하영 연구원은 “3D 프린팅을 활용한 엔진 구성품 제작 가능성을 확인한 것에 의미가 있다”면서 “무엇보다 그동안 축적한 기술을 바탕으로 LNG·액체산소 연소기를 설계부터 시험까지 구현한 것이 자랑스럽다”고 말했다.
임병직 연구원은 “이번 연구는 저비용 발사체 개발을 위한 핵심 기술로서 면밀한 연구를 진행하겠다”고 말했다.
대전=김영준기자 kyj85@etnews.com