삼성전자가 휴대폰 배터리 안전성 검사공정을 완전 자동화한다. 시간과 인력이 많이 드는 병목 공정을 무인화해 검사 정확성과 생산 효율성을 높인다.
5일 업계에 따르면 삼성전자는 스마트폰 배터리 안전성 검사 자동화를 위해 구미 휴대폰 공장에 독일 다관절 로봇을 도입했다. 현재도 검사 결과를 확인하고 불량이 생기면 알람을 하는 등 일부 자동화가 이뤄지고 있지만 배터리나 완제품을 검사 장비에 연결하고 해제 작업은 사람 손을 거쳐야 했다. 이 작업에 다관절 로봇을 투입하면 사람을 대체할 수 있다. 구미공장을 시작으로 중국, 베트남, 인도, 인도네시아, 브라질 등 해외 휴대폰 생산라인에도 무인 검사 공정을 확대한다.
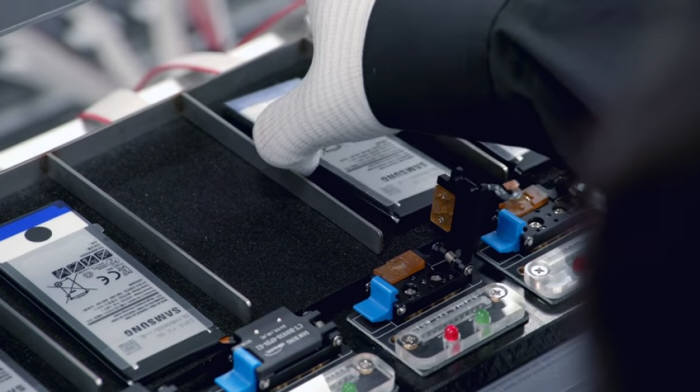
삼성전자는 갤럭시노트7 발화 사고 이후 안전성 강화를 위해 배터리 설계부터 완제품 검사까지 '8포인트 배터리 안전성 검사' 공정을 도입했다.
8포인트 배터리 안전성 검사는 △배터리의 안전성과 내구성을 검사하는 '안전성 검사' △배터리 외관 이상 여부를 평가하는 '외관 검사' △배터리 내부 극판 눌림 등을 발견하기 위한 'X레이 검사' △완제품에 대한 대량 '충·방전 검사' △배터리 누액 발생 여부를 감지해내는 '총휘발성유기화합물(TVOC) 검사' △배터리 내부 탭 융착 상태나 절연 상태, 공정 품질 상태를 확인하는 '배터리 해체 검사' △소비자 사용 환경에 맞춰 검사하는 '사용자 조건 가속 시험' △상온에서 배터리 전압 변화 유무를 확인해 이상 여부를 점검하는 '델타(Δ) OCV(Open Circuit Voltage) 측정'으로 구성된다.
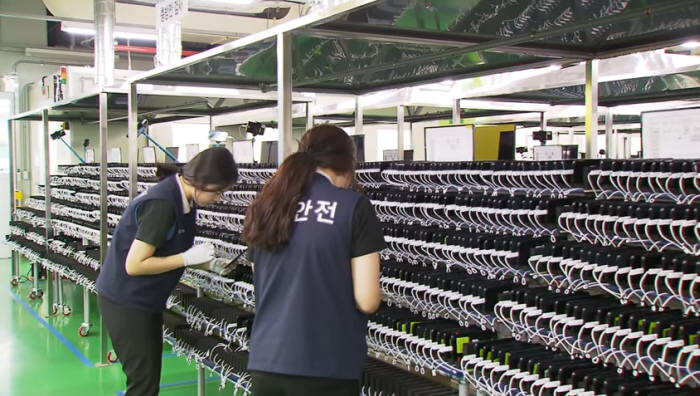
이 중 대량 충·방전 검사, TVOC 검사, 사용자 조건 가속 검사는 갤럭시노트7 발화 사고 이후 새로 도입한 공정이다. 다른 검사도 횟수와 샘플 규모를 대폭 확대하고 기준도 이전보다 엄격하게 적용하고 있다. 일부 안전성 검사는 △부품입고 △스마트폰 제조 △완제품 출고 세 단계에 걸쳐 반복적으로 이뤄진다.
이 같은 조치로 갤럭시노트7 이후 제품 결함으로 인한 배터리 폭발 등 필드사고가 한 건도 발생하지 않았다. 하지만 배터리 검사에 소요되는 시간이 대폭 길어지고 필요한 인력도 많아 검사 공정 효율성 제고 방안을 지속적으로 고민해왔다.
업계 관계자는 “검사 공정은 안전성 확보를 위해 건너뛸 수 없는 만큼 자동화를 통해 효율을 높여 리드타임을 줄이고 사람에 의해 발생하는 휴먼 에러를 줄이기 위해 노력하고 있다”면서 “보다 정교한 동작이 가능한 다관절 로봇을 도입해 검사 효율성을 더욱 높일 수 있을 것으로 보인다”고 말했다.
검사 공정 자동화는 배터리 업계에서도 이슈다. 특히 전기차용 중대형 배터리의 경우 안전성 요건이 더욱 까다롭지만 소형 배터리에 비해 양산 이력이 길지 않아 현재까지는 외관 검사 등 상당부분 검사 공정을 수작업으로 진행한다. 이를 완전 자동화하면 검사 편차를 줄이고 검사 효율성을 보다 높일 수 있는 장점이 있다.
정현정 배터리/부품 전문기자 iam@etnews.com