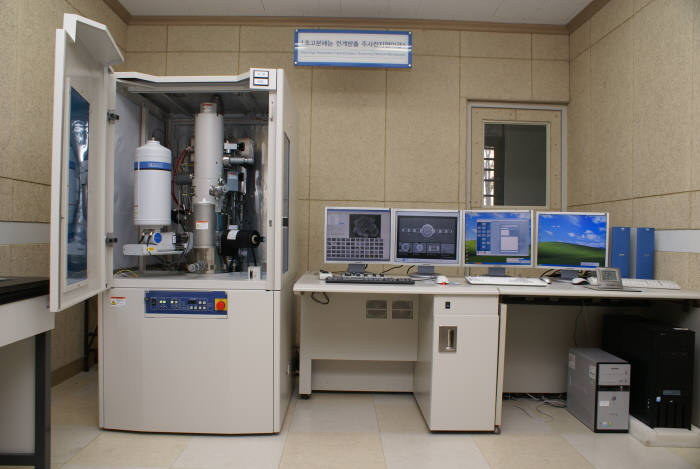
삼성전자가 최근 D램 공정에서 회로선폭 18㎚를 구현하는데 성공, 제품 양산에 들어갔다. D램 분야에서 20나노는 깰수 없는 `마의 벽`으로 일컬어지던 공정이다. SK하이닉스도 현재 20㎚로 D램을 생산하지만, 내년 초엔 10㎚대 양산을 선언한 상태다. 1㎚는 통상 머리카락 굵기 10만분의 1 크기다.
이 같은 초미세 공정 개발에 없어서는 안되는 장비가 주사전자현미경(SEM:Scanning Electron Microscope)이다. 투과전자현미경(TEM:Transmission Electron Microscope)과 함께 반도체 공정이나 신소재 개발 등에 활용되고 있다.
◇SEM 없이는 반도체 공정 없어
SEM은 가시광선을 사용하는 광학현미경과 달리 전자빔이 조사된 시료 표면으로부터 방출되는 신호(이차전자)를 검출해 데이터를 얻는다. 통상 흑백 디지털 카메라로 사진을 찍듯 시료표면에 대한 이미지 정보를 흑백으로 얻을 수 있다.
전자총(E-gun)으로부터 방출된 전자를 원뿔 모양으로 집속시켜 시료 표면을 주사(scanning)하면서 방출되는 신호를 검출해 이미지를 얻는 방식이다. SEM은 전자총의 종류와 전자방출 원리에 따라 `일반 SEM`과 `전계방출주사전자현미경(FE-SEM)`으로 나뉜다.
`일반 SEM`은 텅스텐으로 된 얇은 와이어를 헤어핀처럼 구부리고 여기에 전류를 흘려보낼 때 굴곡부분에서 저항이 생기고, 여기서 열이 발생한다. 이어 열전자가 방출되는 메카니즘으로 작동된다.
반면에 `FE-SEM`은 텅스텐 재질로 된 전자총(tip)으로부터 전자를 방출시키는 원리다.
SEM 국내 시장은 대부분 일본 히타치나 제올, 독일 칼 짜이즈, 네덜란드 FEI, 체코 테스칸 등이 장악하고 있다.
◇SEM 상용화모델은 영국이 처음 만들어
SEM 상용화 모델은 1962년 영국 캐임브리지 인스투루먼트에서 처음 제작해 1964년 미국 듀퐁에 설치했다.
1966년에는 일본 제올에서 SEM(JSM-1, 분해능 50㎚)을 처음 시판했다. 고압전자현미경(HVEM)은 1965년 가속전압 500kV짜리를 일본 히타치가 처음 개발했다.
FE-SEM)은 1972년 일본이 개발했다. 꿈의 분해능이라 여겨졌던 0.1㎚를 1984년 일본 히타치가 돌파했다. 당시 히타치는 0.072㎚ 분해능을 갖는 모델(H-800/200kV)을 선보였다.
국내 최초 전자현미경은 1958년 히타치가 경북대 안영필 교수에게 기증한 HM-3 모델이다. 1970년대 이르러 널리 사용하게 됐다.
국내에서는 1976년부터 1998년까지 일본 아카시가 마산 수출자유공단에서 전자현미경을 주문자상표부착생산(OEM)방식으로 제작해 수출한 바 있다.
◇SEM 세계수준 어디까지 왔나.
FE-SEM의 인-렌즈 타입(in-lens type)이 가장 좋은 분해능을 발휘한다. 0.4㎚다.
인-렌즈 타입은 렌즈 사이로 시료가 들어간다. 대신 시료 형태나 크기에 제약이 있다. 큰 시료는 분석이 되지 않는다. 자장이 있는 시료는 분석이 불가하거나 어려움이 있다.
자동차에서 F1급 차는 실제 도로에서 활용이 어렵지만, 속도라는 측면에서 보면 최고다. 차와 비교하면 `FE-SEM/인-렌즈 타입`은 `현미경계 F1`으로 보면 된다.
세미-인-렌즈 타입은 큰 시료 또는 여러개 시료 분석이 가능하다. 0.8㎚ 고분해능을 갖는다. 최근 국내 많은 연구자들이 구매하는 SEM이 여기에 속한다.
전자현미경 분야에서 세계적 기술을 보유한 일본은 `FE-SEM/인-렌즈타입`을 300여대 보유하고 있다. 이 가운데 10여대는 일반 연구자 접근도 허용돼고 있다. 나머지 290대 정도는 기업과 연구소 등에 보급돼 있다.
배태성 한국기초과학지원연구원 전주센터 분석연구부장은 “일본에서 일반이용자 접근이 허용된 장비가 10대라는 것이 높지 않은 것으로 보일 수 있지만, 뒤집어보면 그만큼 초고분해능 주사전자현미경이 많이 보급돼 일반인에게 허용된 초고분해능 주사전자현미경이 많지 않아도 된다는 것을 의미한다”고 말했다.
배태성 부장은 “현재 해외 제조사들은 FE-SEM 제작 기술을 보유하고 직접 제작하고 있지만, 국내는 일반 SEM만 제작·판매하고 있다”며 “FE-SEM은 제작이 매우 어려운 것으로 알려져 있다”고 덧붙였다.
◇전자현미경 국내 제작, 누가 어디까지 왔나
본격적인 전자현미경 국산화는 한국표준과학연구원 조양구 박사 팀에서 2001년부터 시도했다. 2005년 10만배 영상 획득이 가능한 디지털 SEM 시제품을 개발했다.
최근에는 코셈, 새론테크놀로지, 나노스코프시스템즈, 세크, 펨트론 등 벤처기업이 산학협력을 통해 전자현미경을 개발, 공급하고 있다. 일부에선 세계 정상급 초고해상도 전자현미경도 제작 중이나, 전반적인 수준은 아직 미흡하다.
국내 현미경 제작업체는 대부분 `W-건`으로 된 일반 SEM을 제작하고 있다. 본체 크기를 작게해 책상 위에 올려놓을 수 있는 크기(미니-SEM, 테이블 톱 마이크로스포프)를 주로 제작한다.
일반 SEM은 최고 분해능이 3.0㎚ 정도다.
최고분해능을 발휘하는 `FE-SEM/인-렌즈 타입은 국내 30대 정도가 설치돼 있다. 일부 국내 업체도 제작한 곳이 있다.
국내 연구자들이 활용할 수 있는 장비는 한국기초과학지원연구원 전주센터에 설치돼 있는 것이 유일하다. 나머지 장비는 국내 기업에 설치돼 있어 접근이 제한적이다. 25대 정도가 S기업 및 관련 기업에 설치돼 있다. 나머지는 국내 반도체 관련 회사에 설치돼 있어 일반연구자 접근이 제한적이다.
국내에 도입된 SEM은 대략 3000대가 넘는 것으로 추정된다. 현재 가동이 되고 있는 SEM은 약 1800대 정도로, 이중 국산 SEM은 200~300대 정도로 추정된다.
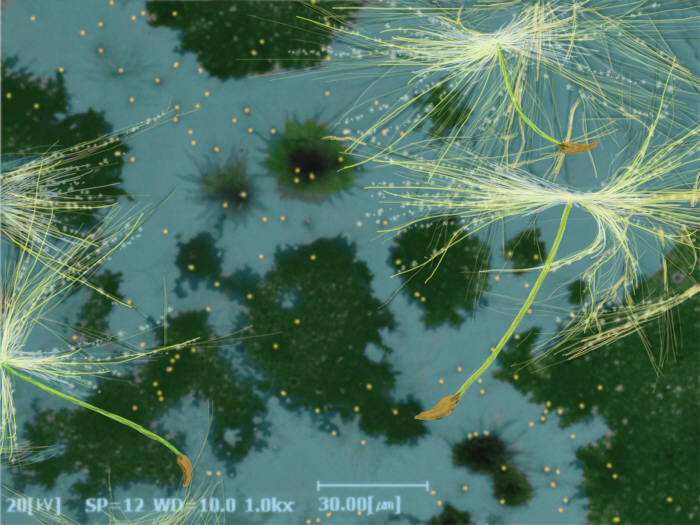
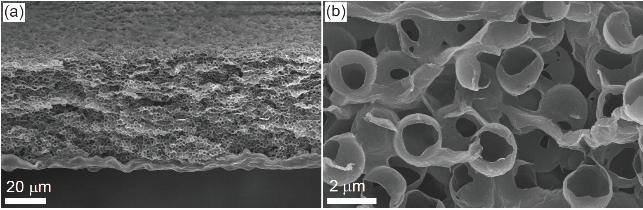
대전=박희범 과학기술 전문기자 hbpark@etnews.com