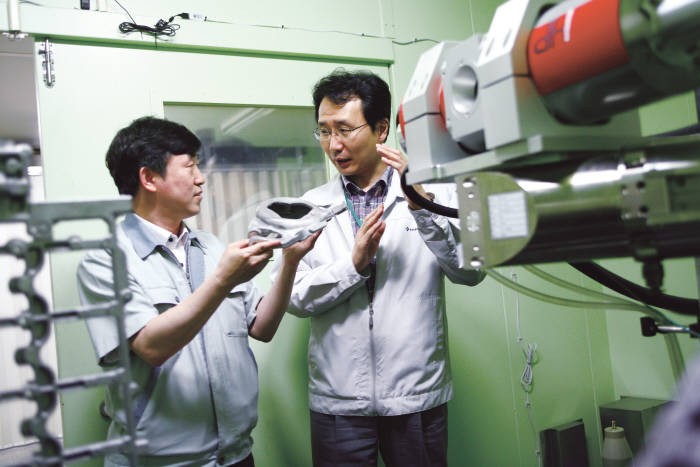
1895년 독일 뢴트겐이 엑스레이(X-ray)를 발견한 이래 물체의 내부를 들여다 볼 수 있는 기술은 끊임없이 진화했다. 기존 2차원 엑스레이 촬영으로는 신체 장기·뼈·조직이 겹친 부분을 검사할 수 없었다. 3차원(3D) CT 기술이 개발되면서 문제는 해결됐다. 1970년대 영국에서 개발한 의료용 컴퓨티드토모그래피(CT) 시스템은 신체의 내부를 마치 잘라서 본 것 같은 3D 영상을 구현해 의료계에 일대 혁명을 불러왔다.
2000년대 들어 3D CT 시스템은 의료 분야에서 산업 현장으로 확산됐다. 미국·독일·일본이 경쟁적으로 산업용 3D CT 시스템을 개발하면서 기술 발전은 더욱 가속화됐다.
현재 산업용 3D CT 시스템은 IT·섬유소재·자동차·우주항공 등 대부분의 산업 현장에서 쓰인다. 부품의 내부를 꿰뚫어볼 수 있어 미세한 결함까지 찾아 불량을 예방할 수 있기 때문이다. 3D CT 시스템은 정밀 부품을 측정·검사하는 수준을 넘어 역설계하는 단계까지 진화됐다.
산업용 3D CT 기술의 중요성은 점차 커지고 있지만 우리나라는 이 분야에서 걸음마 수준에 불과하다. 과거 국내 기업이 산업용 3D CT 시스템을 내놓기는 했지만, 핵심 부품을 수입해 조립하는 수준에 그쳤다.
2000년대 후반 산업용 3D CT 시스템을 국산화해야 한다는 각계의 목소리가 커졌다. 우리나라는 IT·자동차·조선 등 제조업이 주력 산업인 국가다. 제조업을 고도화하려면 소재·부품 산업 경쟁력을 강화해야 한다. IT·자동차 부품이 고도화·정밀화되면서 외형 진단 수준을 벗어나 내부 결함까지 찾아내야 한다. 3D CT 시스템이 중요한 이유다.
지난 2010년 우리나라는 3D CT 시스템 기술 개발에 뛰어들었다. 선진국보다 출발은 늦었지만 성과는 빠른 속도로 일궈내고 있다.
3D CT 시스템이 산업원천기술개발사업으로 선정되면서 국산화에 가속도가 붙었다. 한국생산기술연구원 주관으로 쎄크·서울대·서울여대·현대모비스·엔에스씨인더스트리·쓰리디산업영상 등 산학연 연구팀이 구성돼 3차원 투과영상 기반의 제품 검사 플랫폼 기술 개발 과제에 착수했다. 2년 만에 원천 기술을 잇따라 확보하는데 성공했다.
산학연 연구팀이 개발한 핵심 기술은 크게 세 가지다. △강한 엑스레이를 쏘아 부품의 내부까지 투과해 촬영할 수 있는 3D 스캐너 △촬영된 데이터를 3D 영상으로 보여주고 고속으로 결함을 찾아내는 소프트웨어 △산업 현장의 생산라인과 연계해 부품을 전수 검사할 수 있는 인라인 검사 플랫폼이다.
3D 스캐너를 제작한 쎄크는 생산 비용의 절반을 차지하는 엑스레이 튜브를 세계 네 번째로 개발하는 성과를 일궜다.
김형범 쎄크 부설연구소 실장은 “3D CT 시스템을 국산화했을 뿐 아니라 이를 수출하는 데도 성공했다”며 “최근에는 선진국 시장에 역진출하는 쾌거를 거뒀다”고 말했다.
소프트웨어 개발은 서울대·서울여대·쓰리디산업영상이 담당했다. 이번 과제로 개발된 SW는 속도면에서 선진국 기술을 넘어섰다. 공동 연구팀은 그래픽프로세서(GPU) 가속 기술로 4GB 분량의 데이터를 처리하는 시간을 1분 이내로 줄였다. 기존 외산 SW보다 20배 이상 빠른 수준이다. 부품 내부에 생긴 기공, 이물질도 자동으로 잡아낸다.
유승목 생기원 주조기술센터 센터장은 “부품 검사 때 소요되는 시간은 전수 검사에서 중요한 부분 중 하나”이라며 “연구팀이 개발한 SW는 생산라인과 연계해 부품을 전수 검사할 수 있는 성능을 갖췄다”고 설명했다.
하드웨어와 소프트웨어를 엮어 만든 3D 산업용 CT 시스템과 생산현장을 연계하는 솔루션을 개발하는 작업은 모비스와 엔에스씨인더스트리, 생기원 미래융합연구그룹(황정호 박사)이 맡았다. 생기원 주조기술센터(센터장 유승목)가 내년 완료를 목표로 참여 기관을 총괄 지휘하고 있다.
연구팀은 내년까지 분석 용량을 키운 3D CT 시스템을 개발하고, 제품의 균열 검사 기능을 보완할 계획이다.
이형수기자 goldlion2@etnews.com