제조업의 경쟁력은 연구개발(R&D)에서 시작된다. 기술력을 높여야 시장에서 살아남고, 나아가 시장을 이끌 수 있다. 창조경제도 마찬가지다. 창조경제 시대를 맞아 신성장동력 발굴이라는 과제를 안은 제조업에 R&D는 출발점이다. 정부가 출연연구기관의 차세대 산업기술 R&D를 지원하고, 이를 중소·중견기업이 이전받아 새로운 시장을 창출하는 선순환 구조가 필요하다. 앞으로 5회에 걸쳐 산업기술 R&D 성공 사례를 소개한다.
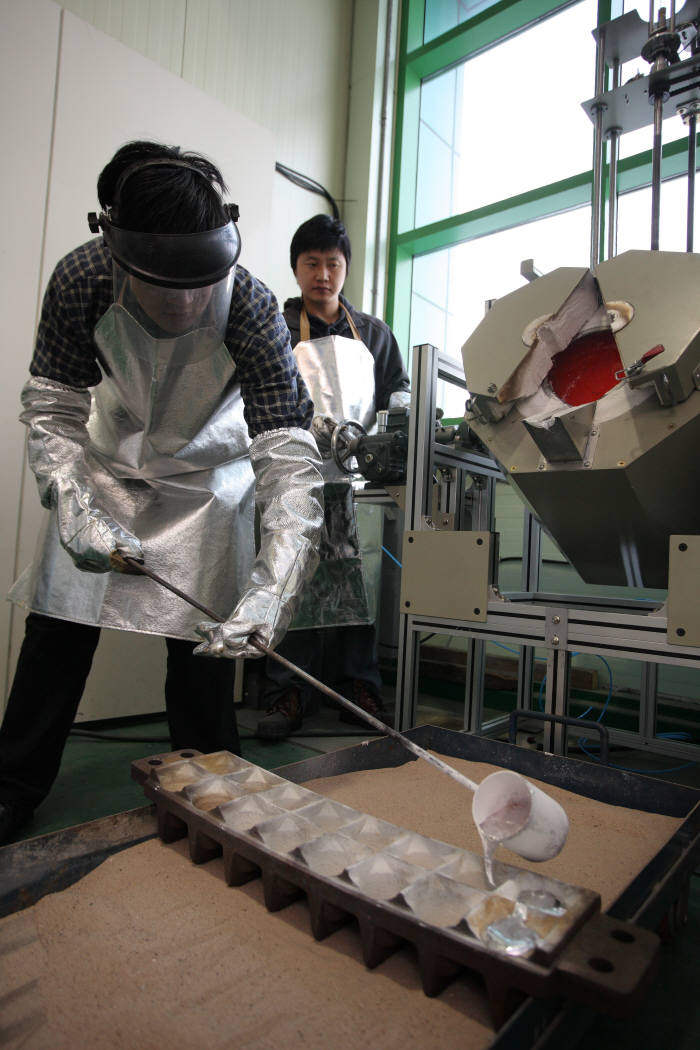
중세 유럽에서 널리 퍼졌던 연금술. 비금속을 황금(귀금속)으로 만든다는 연금술은 훗날 과학에 밀려 퇴출당할 때까지 유럽인들을 사로잡았다.
21세기에도 연금술은 존재한다. 차이가 있다면 과학을 바탕으로 실재하는 기술이라는 점이다. 한국생산기술연구원 김세광 박사팀이 개발, 세계 최초로 상용화까지 이룬 에코(친환경)-마그네슘 및 알루미늄 합금 기술은 21세기형 연금술이다.
에코-마그네슘·알루미늄은 기존 합금의 단점인 산화와 발화 문제를 획기적으로 개선했다. 기존 마그네슘 합금은 공정 중 산화와 발화를 방지하기 위해 육불화황(SF6), 이산화황(SO2) 등 보호가스가 사용됐다. SF6는 온실가스로 분류돼 선진국에선 사용이 제한된다. SO2는 인체에 유해한 가스로 철계 장비를 부식시켜 장비 수명을 단축시킨다.
에코-마그네슘 합금은 이들 가스를 사용할 필요가 없어 친환경 공정을 구현하고 생산 비용을 낮췄다. 김 박사는 이를 `SHE`로 표현했다. “공정·제품의 산화와 폭발을 막는 안전성(Saftey), 유해 가스를 사용하지 않는 건강성(Health), 온실가스를 사용하지 않는 친환경성(Environment) 세 가지를 동시에 구현했다”는 설명이다.
김 박사팀은 에코-마그네슘 합금 기술을 바탕으로 에코 알루미늄 합금 기술 개발에도 성공했다. 기존 마그네슘 대신 에코-마그네슘을 알루미늄 합금 원소로 사용했다. 에코-마그네슘 기술 덕분에 강도와 신율(재료 인장 시험 시 재료가 늘어나는 비율)이 각각 30%, 15%씩 높아졌다.
세계 최고 수준 기계적 특성을 가진 알루미늄 합금과 비교해 제조 단가는 60%에 불과하지만 강도는 오히려 5% 상승했다.
김 박사팀은 지난 2008년 에코-마그네슘 기술 최초 개발 이후 에코-알루미늄 기술 개발과 양산 및 기술 확장 노력을 이어가고 있다. 김 박사는 “친환경 기술인데다가 제조 비용을 줄이고 합금 강도와 신율을 동시에 높일 수 있어 산업계 관심이 높다”고 전했다.
◇기대 효과와 상용화 현황
에코-알루미늄·마그네슘 합금 기술은 기존 뿌리산업에 `마른수건 비틀어짜기`가 아닌 새로운 고부가가치 창출 기회를 안겨줄 것으로 기대된다. 강도·신율 향상과 경량화가 동시에 요구되는 자동차, 항공기, 휴대폰 등 국가 주력산업에 응용 범위가 넓을 것으로 보인다.
지난 2010년 국내 중소기업으로 기술 이전을 완료한 후 상용화도 빠르게 진행됐다. 에코-마그네슘 기술은 HMK, 에코-알루미늄 기술은 아이원과 GNS에 각각 이전됐다.
에코-마그네슘 소재는 LG전자 휴대폰 내외장재에 적용됐고, 에코-알루미늄 소재는 현대자동차 범퍼와 시트레일에 사용됐다.
최근엔 해외 수출도 가시권에 들어왔다. 에코-알루미늄 기술을 이전받은 아이원은 지난해 말 미국 GM의 차량용 범퍼 소재 규격으로 등록을 마쳤다. 오는 2015년부터 GM 양산 차종에 에코-알루미늄 합금이 사용될 것으로 보인다. 순조롭게 추진되면 400억~500억원에서 많게는 700억~800억원에 이르는 매출 효과가 기대된다. 연장흠 아이원 부사장은 “기존 소재에 비해 동일한 원가로 20%가량 경량화가 가능하기 때문에 시장 전망이 매우 밝다”고 말했다.
추가 기술 이전을 통한 확산 작업도 진행되고 있다. 생기원은 국내뿐 아니라 해외 기업과도 기술 이전을 협의 중이다. 생기원은 에코-마그네슘·알루미늄 합금 기술 개발에 따른 기존 시장 확대와 신시장 창출에 힘입어 5조원에 이르는 생산유발 효과를 예상했다.
이호준기자 newlevel@etnews.com