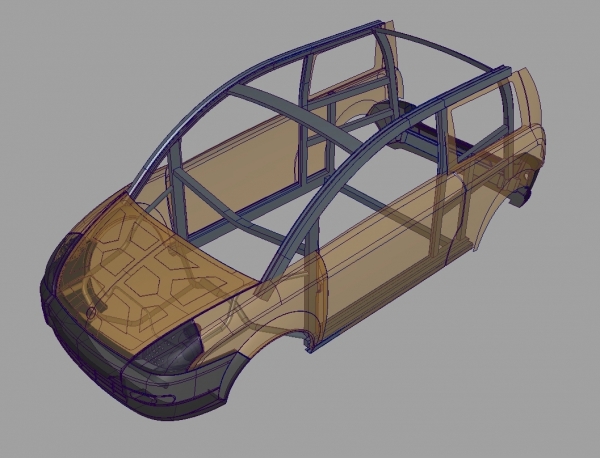
전기자동차 기술 개발은 사실 오래전부터 진행돼 왔지만 그 기술이 실제로 사용되는 단계에 이른 것은 최근이다. 전기차 파워솔루션과 관련된 기술 중에서 가장 큰 난관은 배터리 파워팩이었는데 최근 고출력에 가볍기까지 한 리튬이온 배터리가 개발되면서 급속 충전이 가능해지고 라이프사이클도 혁신적으로 늘어나고 있다.
이제 전기차 보급에서 남은 난관으로 거론되는 사항은 어떻게 하면 차량의 무게를 줄일 수 있는지다. 세계 유수의 자동차 회사들은 전기차 이전에도 경량화에 초점을 두고 총력을 기울여 왔다. 크라이슬러는 이미 1995년도부터 콤퍼지트 플라스틱 바디를 연구해 최근까지 많은 노하우를 쌓아놓고 있다. 플라스틱 차체에서 금속을 완전히 제거한 일체형 조합은 두 사람이 양 손으로 거뜬히 들 수 있을 만큼 경량화가 가능했다. 문제는 초창기엔 내연기관 엔진을 사용했기 때문에 엔진의 진동과 열로 인해 플라스틱 차체에 변형이 와서 실제 구현이 어려운 상황이었다. 최근 전기 자동차로 바뀌면서 전기모터는 진동과 열이 적기 때문에 콤퍼지트 플라스틱 바디 차체가 실제로 상용화될 기회를 맞고 있다.
또 포드나 GM은 차체의 뼈대 격인 프레임바디를 알루미늄 합금 또는 강화 마그네슘 등으로 만들고 패널은 엔지니어링 플라스틱으로 마감해 경량화 차체를 만들어 기존 차량에 비해 약 50% 이상의 무게 절감효과를 가져온 것으로 보고된다.
다행히 국내에서도 중소기업 기술로 세계 최초로 알루미늄에 카본나노튜브(CNT)를 적용한 고강도 알루미늄합금(기존 알루미늄 강도의 두 배)을 개발했다는 소식이다. 전남 신소재기술 산업화 센터는 기존 마그네슘의 밀도보다 4배나 높은 고강도 마그네슘을 개발해 과거 꿈도 꿀 수 없었던 마그네슘을 이용한 압출 및 프레스 가공이 가능해졌다. 이러한 소재 경량화 기술이 전기자동차 또는 전자·항공·철도 등에 적용되게 되면 실질적인 에너지 사용 감소효과를 가져올 수 있다. 또 전기자동차 관련 소재 연구에 긍정적 요소로 적용될 수 있어 앞으로 국내 자동차 부품산업에도 큰 자극이 될 것으로 기대한다.
이정용 레오모터스 대표 jyl2000@paran.com