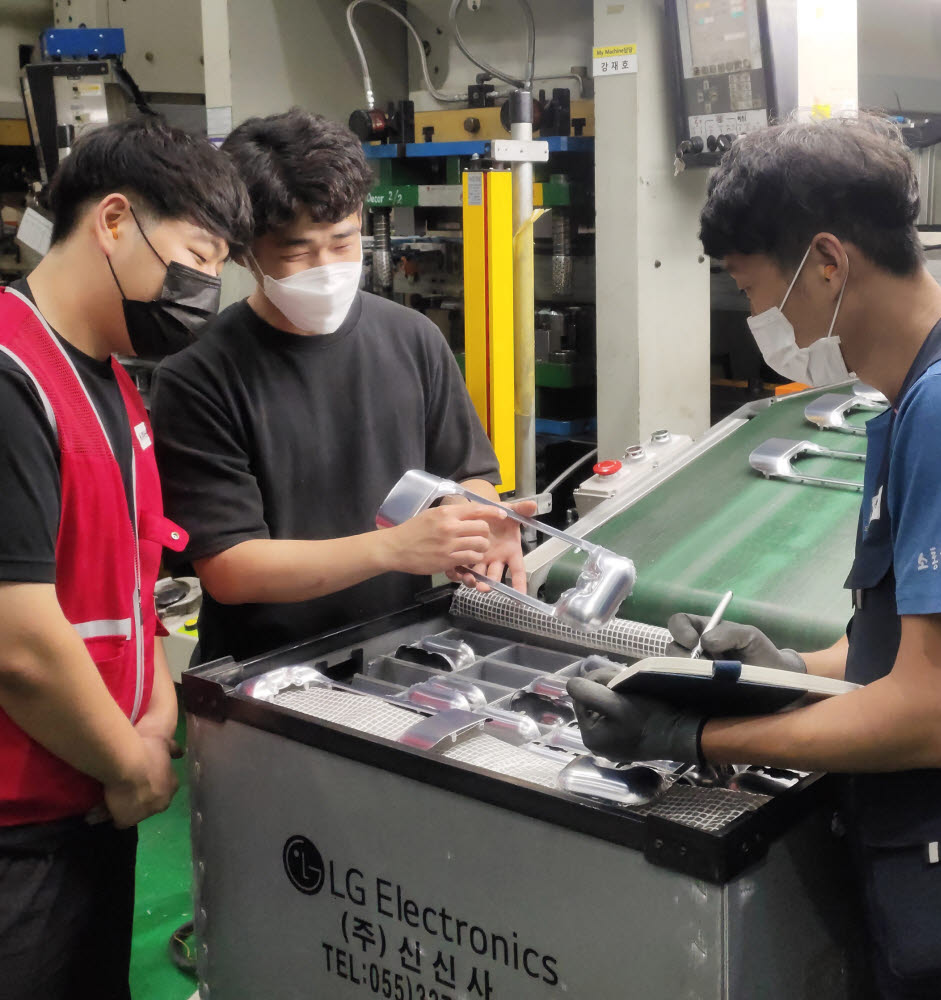
제조 혁신은 이미 시작됐다. 디지털 전환을 통한 제조혁신, 즉 스마트공장은 수요기업의 적극적 관심과 정부, 대기업 지원이라는 삼박자가 맞아떨어지면서 제조 현장 깊숙이 스며들고 있다. 스마트공장 도입으로 생산성 극대화라는 '맛'을 본 기업들이 스마트공장에 더욱 관심을 갖는 선순환이 이뤄질 것으로 기대를 모은다.
가전 부품 전문회사인 신신사(Sinsinsa)는 2020년 디지털 기술을 적용한 설비관제시스템을 체계적으로 구축해 생산 효율을 극대화했다. 경남 김해에 위치한 이 회사는 제조 과정을 분석, 생산이나 품질에 영향을 주는 요소를 찾아내고 온도, 압력, 수평도 등을 감지하는 센서를 적용해 실시간 모니터링이 가능하도록 했다. 그 결과 불량 등의 이유로 생산중단에서 재가동까지 소요되는 시간이 전년 대비 20% 감소했다. 센서를 통해 수집한 각종 데이터는 향후 불량 예측 등에 활용할 계획이다.
신성오토텍은 원재료부터 생산설비, 완제품까지 데이터 기반 품질관리 시스템을 구축했다. 원재료를 보관하는 창고의 온도와 습도, 금형 온도, 완제품 크기와 중량 등 생산과정 전반을 디지털화해 관리하고 있다. 데이터에서 비정상 값을 발견하면 바로 개선할 수 있어 생산경쟁력이 향상됐다.
극적 사례는 마스크 제조업체에서 일어났다. 솔젠트는 자제와 제품 구분관리를 위해 바코드 시스템을 도입, 물류 동선을 148미터에서 98미터로 34% 단축했다. 라벨 검사기 등 생산공정 전반에 스마트 시스템을 적용해 주당 1만1900키트에서 2만571키트로 생산성을 73% 끌어올렸다. SD바이오센서는 스마트공장 구축을 통해 설비당 순간정지 회수를 시간당 4회에서 1회로 줄이는 등 하루 10만키트의 생산량 향상을 나타냈다.
손세정제를 생산하는 앤제이컴퍼니는 스마트공장 구축을 통해 생산량이 월 5톤에서 50톤으로 무려 10배 성장했다. 첨단장비 도입은 최소화하면서 물류 동선 최적화, 충진장비 도입 등을 통해 생산성 향상을 이뤄냈다.
중소기업은 투자나 인력 부족 등을 이유로 생산공정이 낙후됐으나 자체 해결능력을 보유하지 못한 곳이 많다. 앞서 예로 든 앤제이컴퍼니의 경우 스마트공장을 구축하기 전에는 주전자로 손세정제 원액을 날랐을 정도다. 단 두 명의 직원이 모든 공정을 처리하다보니 스마트공장은 엄두도 내지 못했던 것이다. 정부는 이런 현실을 파악하고 중소기업 생산성 향상을 위한 다양한 정책을 펴고 있다. 특히 세계 최고 수준 제조 경쟁력을 갖춘 대기업 멘토를 활용한 스마트공장 지원 사업이 힘을 얻고 있다.
중소벤처기업부는 2018년 중소기업 스마트 제조혁신 전략을 발표하고 2022년까지 스마트공장 3만 개를 보급한다는 목표를 세웠다. 이는 국내 제조 중소기업의 50%에 해당한다. 중기부는 당시 대기업 참여를 유도하기 위해 상생형 스마트공장 구축 시 대기업에 동반성장지수 평가 우대라는 '당근'을 제시했다. 이 같은 정책에 힘입어 2019년까지 1만2660개의 스마트공장을 보급했고 2020년에는 5600개를 잠정 보급했다.
삼성전자, LG전자 등 대기업도 중소기업 스마트공장 구축에 적극 나서고 있다. 삼성전자는 5년 동안 1000억원을 투자해 2500개 중소기업에 스마트공장을 구축한다는 계획을 2018년 발표했다. 스마트공장지원센터를 사내 설치하고 지원 체계를 마련했다. 2015년부터 시작한 자체 사업을 포함하면 삼성전자는 현재까지 2157개 중소기업의 스마트공장 구축을 지원했다. LG전자는 2020년 64개 협력사에 스마트공장 구축을 지원해 공장 자동화율을 40%대로 끌어올려 시간당 생산량을 20% 이상 향상시켰다. LG전자는 2018년부터 매년 약 60개 협력사를 대상으로 생산공정 디지털 기술 적용을 지원하고 있다.
김용주기자 kyj@etnews.com