“샘플 조사를 하느냐고요? 말도 안됩니다. 당연히 전수조사를 해야죠. 100% 전수조사를 하고 있습니다.”
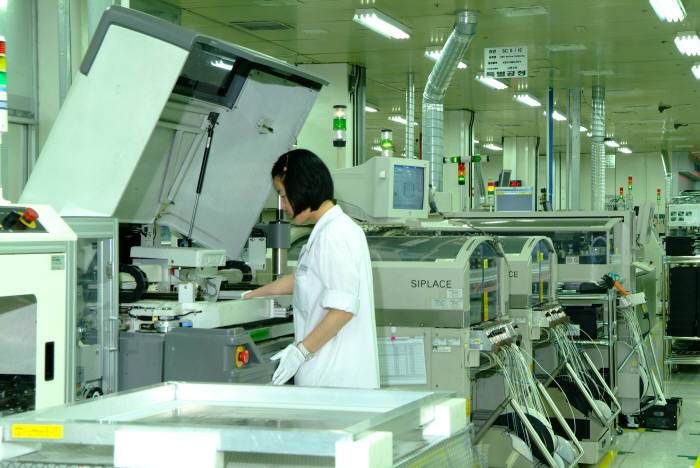
지난달 27일 찾아간 경기 이천 콘티넨탈 오토모티브 시스템(대표 선우 현) 생산공장. 1층 생산라인에선 엔진과 변속기를 통합 제어하는 전자제어장치(ECU) 생산이 한창이었다. 자동차 부품 가운데 최고난도 기술력을 요하는 제품이 정밀하게 제작되고 있었다.
이명석 생산본부 부장은 “안전과 직결된 자동차 부품을 샘플 방식으로 조사하는 것은 있을 수 없다”면서 “연간 생산하는 2000만개의 부품을 하나도 빠짐없이 점검한다”고 품질의 중요성을 강조했다.
콘티넨탈 오토모티브 시스템은 1987년 한국에 진출한 콘티넨탈 그룹 계열사 가운데 가장 규모가 큰 회사로 성장했다. 지난해 콘티넨탈이 한국에서 올린 매출 2조원 가운데 절반인 1조원가량을 담당했으며 직원 수도 1000여명으로 가장 많다. 엔진 제어장치(EMS ECU)와 연료 분사장치, 자동 변속기 제어장치(TCU), 통합형 엔진-자동변속기 제어장치, 에어백 전자제어장치 등 자동차에서 ‘핵심 중의 핵심’ 부품을 생산한다.
국내 자동차 산업이 급격히 성장하던 2000년대 초중반 콘티넨탈 오토모티브 시스템은 위기감을 느꼈다. 단순한 생산라인 증설만으로는 가격경쟁력 확보가 힘들었기 때문이다. 특히 생산량이 늘면 불량률도 덩달아 높아질 위험이 있었다. 고가의 복잡한 장비를 들여놓는다고 해결될 문제가 아니었다.
선우 현 사장은 그때까지의 방식을 버리고 당대의 자동차 선진국인 일본식 생산방식을 도입하는 과감한 결정을 내린다. 그 가운데 하나가 ‘린(Lean)’이다. 낭비와 불량률을 최소화해 생산성을 극대화한다는 게 린 생산방식의 핵심이다. 2005년부터 린 추진팀을 만들고 선우 사장을 중심으로 경영진이 강력하게 도입에 앞장섰다.
점점 린 방식이 정착하면서 놀라운 변화가 나타났다. 2005~2013년 단 한 번에 불량 없이 생산되는 비율을 의미하는 ‘초기통과수율(FPY)’은 96%에서 99%로 높아졌다. 자연스럽게 불량률이 낮아지면서 부품 100만개당 불량품 개수는 31개에서 2.5개로 뚝 떨어졌다.
생산성 향상은 더욱 놀랍다. 같은 기간 부품 생산량과 판매량은 각각 287%와 210%씩 증가했는데, 직원 수와 공장 면적은 83%, 80% 늘어나는 데 그쳤다. 대략적으로 직원 수가 갑절이 되는 동안 생산량은 네 배가 된 것이다. 10년도 안 돼 생산성이 갑절 높아진 셈이다.
특히 일본식 생산방식을 그대로 따르지 않고 이를 한국식으로 소화, 콘티넨탈 본사 차원의 경영방식인 ‘콘티넨탈 비즈니스 시스템(CBS)’을 구축하는데 큰 공을 세웠다.
이 같은 혁신을 인정받아 이천 사업장은 본사로부터 ‘모범적인 콘티넨탈 사업장’으로 뽑혔고, 베스트 퍼포먼스 상을 6년 연속 수상했다. 30여개국에서 620여명의 콘티넨탈 직원이 이천공장을 방문해 노하우를 전수받기도 했다.
회사 관계자는 “한국 내에서 가장 뛰어난 전장 부품 회사가 되는 게 목표”라면서 “자동차 전자화가 가속화됨에 따라 안전 및 편의장치 관련 전장부품을 생산하는 이천공장의 사업전망도 밝을 것으로 예상한다”고 말했다.
김용주기자 kyj@etnews.com