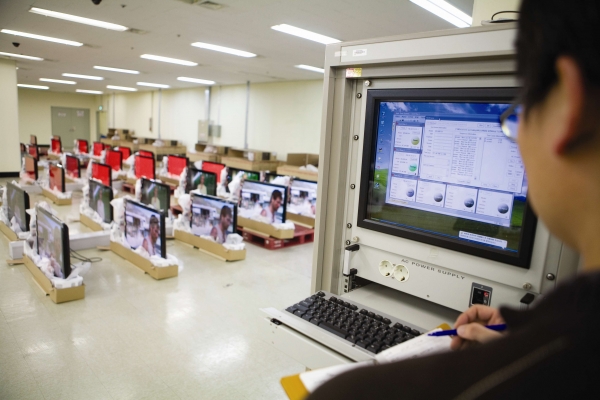
전자업계가 생산성 향상을 위해 다양한 실험에 나서고 있다.
7일 관련업계에 따르면 삼성전자는 생산성 제고의 일환으로 셀라인 방식 도입을 확대하고, 물류비용을 절감할 수 있는 다양한 운송기법을 개발·적용하고 있다. LG전자는 무인감시시스템 도입을 전세계 TV생산 공장으로 확대하면서 경비절감에 나섰다.
삼성전자는 중국 후이저후 MP3플레이어, 휴대폰 생산라인을 벤치마킹해 셀라인 방식을 확대 적용하고 있다. 셀라인은 처음 공정부터 최종 공정까지를 한 명의 작업자가 담당하는 방식이다. 작업자간 속도에 제약을 받지 않기 때문에 작업의 효율성을 높일 수 있다.
실제로 멕시코 LCD TV 공장은 기존 컨베이어에서 셀라인으로 변경한 이후 올해 생산성이 117% 향상됐다. 삼성전자 멕시코 공장은 이 같은 생산성을 바탕으로 올해 삼성이 북미 컬러TV 시장 1위를 달성하는 데 보이지 않게 기여했다.
멕시코 생산법인장을 맡고 있는 한명섭 삼성전자 상무는 “공장에서 근무하는 멕시코인들에게 권한을 주는 현지화 경영을 하고 있다”며 “셀라인 방식 역시 생산성을 높이는 전환점이 됐다”고 설명했다.
셀방식은 삼성전자 협력사로까지 확산 되는 중이다. 기지국용 안테나 등을 생산하는 케이엠더블유의 경우, 제조라인을 컨베이어 방식에서 셀방식으로 변경하면서 기존대비 30% 가량의 생산성 향상 효과를 봤다.
LG전자의 생산성 제고 노력은 품질관리에서 확인할 수 있다. LG전자는 TV품질 관리강화의 일환으로 핵심장비인 자동 불량 가능성 테스터 옐로우박스(Yellow Box) 설치장소를 해외 11개 법인으로 확대했다. 옐로우박스는 그 동안 평택 등 국내 공장에만 설치돼 있었다. 옐로우박스란 무작위로 리모컨 명령어를 송출시킨 뒤 TV에서 발견되는 여러가지 문제점을 영상비교 방법으로 발견, 버그(Bug) 데이터를 저장한다. 오작동이 발생할 경우, 테스트 제품 앞에 설치된 특수카메라가 이를 자동으로 포착해 기록해 준다. 항공기 블랙박스처럼, 모든 오작동 관련 기록이 데이터로 저장, 연구원들이 현장에서 일일이 버그를 체크하지 않아도 된다.
LG전자 관계자는 “그 동안 연구원들이 버그 발생 시 해외공장으로 출장을 가야 했다”며 “옐로우박스 설치 후 시간과 비용이 들어가는 출장을 줄일 수 있게 됐다”고 설명했다.
김원석기자 stone201@etnews.co.kr